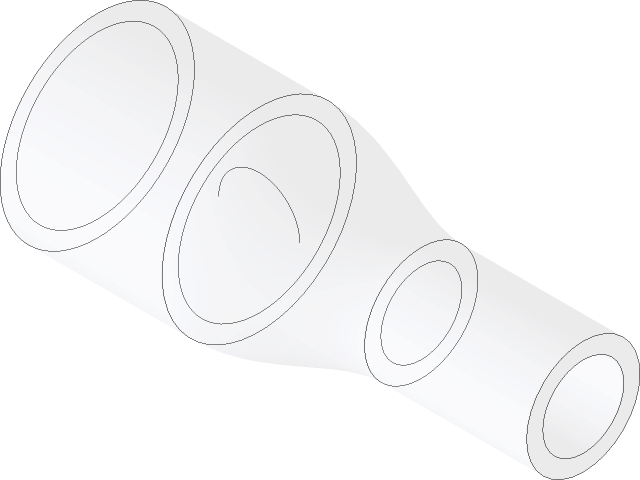
velocity,pressure & temperature distribution in nozzle
grabcad
In this model a nozzle designed in SolidWorks with an inlet velocity of 2.5 m/s. The velocity, pressure, and temperature distribution play crucial roles in understanding the flow behavior and performance of the nozzle.Velocity Distribution:As the fluid enters the nozzle, it undergoes a process of acceleration due to the converging shape of the nozzle. The velocity distribution describes how the fluid velocity changes along the length of the nozzle. In this case, with an inlet velocity of 2.5 m/s, the velocity will gradually increase as the fluid flows through the converging section, reaching its maximum at the nozzle throat. After passing through the throat, the fluid expands in the diverging section, resulting in a decrease in velocity.Pressure Distribution:The pressure distribution in the nozzle is influenced by the shape and dimensions of the nozzle, as well as the fluid properties and flow conditions. In general, as the fluid accelerates through the converging section, the pressure decreases. At the nozzle throat, where the velocity is maximum, the pressure reaches its lowest point. In the diverging section, as the fluid expands, the pressure gradually increases. The pressure distribution in the nozzle is essential for determining the forces acting on the fluid and the performance of the nozzle.Temperature Distribution:The temperature distribution in the nozzle is primarily affected by the energy exchange between the fluid and its surroundings. Depending on the specific application and the properties of the fluid, the temperature distribution can vary. However, in general, the temperature is expected to remain relatively constant along the length of the converging section. As the fluid passes through the nozzle throat and into the diverging section, the temperature may experience some changes due to expansion or compression effects.SolidWorks, as a powerful computer-aided design (CAD) software, can simulate fluid flow and provide insights into the velocity, pressure, and temperature distributions in the nozzle. By analyzing these distributions, engineers can optimize the nozzle design for desired performance characteristics, such as maximizing thrust, minimizing pressure losses, or achieving efficient heat transfer.
With this file you will be able to print velocity,pressure & temperature distribution in nozzle with your 3D printer. Click on the button and save the file on your computer to work, edit or customize your design. You can also find more 3D designs for printers on velocity,pressure & temperature distribution in nozzle.