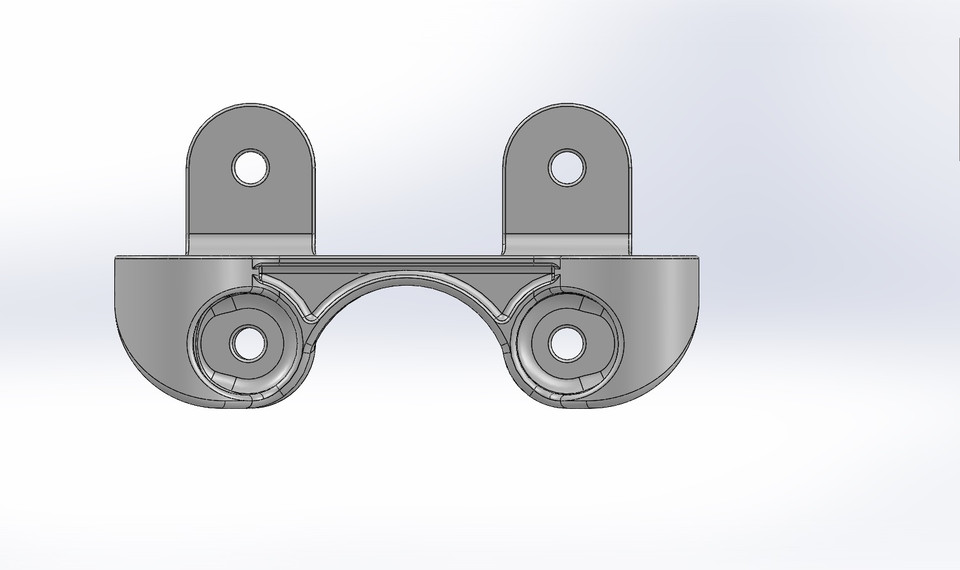
ULA Challenge Bracket
grabcad
In this design challenge, a bracket was created with a focus on stress considerations, meeting minimum edge distance requirements and fitting within the material envelope. The part's shape demonstrates that a bridge is the most efficient load-bearing shape, with forces being counteracted by two supports. A curved I-beam was used to support the load and connect both sides of the bracket, while an I-beam design was also used to carry the moment and connect to the bridge piece at the supports. Fillets were applied wherever possible to negate stress concentrations. Clearance holes for fasteners were specified, accounting for washer use and socket clearance for nut access. Load calculations were performed using Solidworks Simulation with hole pattern D fixed geometry, generating excessive loads that were largely ignored in the uniform load applied on datum B. The simulation results indicated that the bracket is about to fail at the ultimate load, verifying the initial prediction of a bridge as the most efficient load-bearing shape. Areas of poorly loaded material exist but are necessary to satisfy minimum edge requirements or stiffen parts to distribute load. A decision was made to eliminate small pockets to reduce print time and labor without affecting stress considerations. The final bracket has a mass of 0.0897 lbs, volume of 1.853 cubic inches, and meets all design constraints.
With this file you will be able to print ULA Challenge Bracket with your 3D printer. Click on the button and save the file on your computer to work, edit or customize your design. You can also find more 3D designs for printers on ULA Challenge Bracket.