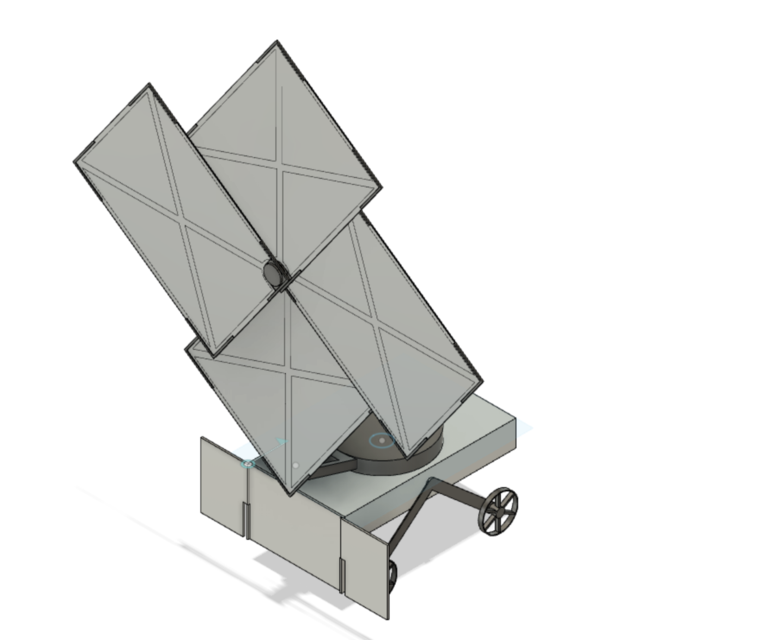
TORCH Submission
grabcad
This heliostat uses a hard surface reflector for its preciseness. The design hinged on the following idea: How to obtain a 10m2 aperture with 1.5*2 dimension with minimum chances of failure. Only four facets are used since that is the minimum required to obtain a 10m2 aperture. Unlike other designs, all facets are directly attached to the support structure, since facet-facet connections lead to error compounding. The facet would be attached to the structure via a single spot of adhesive at the center. The edges would be supported by the frame in which they can slide. The internal dimensions of the frame are slightly greater than the facet and are lined with a soft material to allow for thermal expansion. Only three of the facets need to be rotated during deployment. Facet 0 remains in the same position, thereby reducing the requirements for the central hinge. By using a single hinge mechanism all development effort can go into ensuring its good functioning rather than developing multiple compound deployment mechanisms. The elevation and azimuth drives used for deployment are the same one used for tracking, thereby reducing complexity. PV panels are fitted directly onto the main body to lower stress on the heliostat supports, and because the heliostat normal vector will not point to the sun.
With this file you will be able to print TORCH Submission with your 3D printer. Click on the button and save the file on your computer to work, edit or customize your design. You can also find more 3D designs for printers on TORCH Submission.