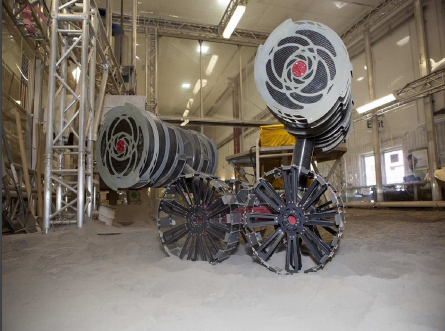
to the moon
grabcad
No changes on the NASA design which have been tested intensively will be made. As little change to the existing design as possible and as much improvement through extension without exceeding the weight limit is desired. The size & position of the scoops, speed of the rotation and the whole concept of the rover and the necessary mechanics are well tested. That's why the focus of my approach lies on the inside design of the bucket-drum. In my opinion, the maximum efficiency can be achieved through arrangement of the baffles. The scoops should have the smallest possible width to reduce useless spar-room in any given position. No movable parts for the solution approach will be used because unnecessary wear and tear on an off-world mining-robot is not desired. What leads to the following solution approach for the inside of the bucked-drum / divide et impera. First, by dividing the whole bucked-drum into 4 vertical sections, to maximize the efficiency of each section. Each section will be separated by partition walls through the given width of 90 millimeters per scoop. Second, by separating the inside of each section through the baffles in the form of a dual spiral to the center, which will increase fill ratio through separation. The dual spiral is defined through the size & width of the scoops. Through my investigation, I came to the following conclusion for average granulation of lunar regolith: A nominal regolith density of 1.5 grams per cubic centimeter may be assumed. Based on the requirements needed for submission: Maximum total width of scoops engaged at any given time: 175 mm Maximum bucket drum mass: 5 kg Maximum bucket drum diameter: 450 mm Maximum bucket drum length: 360 mm A minimum volume of regolith captured: 17.6 liters. I made the following rudimentary mathematical starting positions: The maximal mathematical volume per bucked-drum by 450 mm x 360 mm results in 57.22 liter volume which equals to 85.83 kg regolith, which equals at a fill ratio of 50% in 28.61 liter or 42.915 kg per bucked-drum. In order, I decided to calculate the two following use cases based on the width of the scoops for: 30 mm what would result at a fill ratio from minimum 50% in 17.19 liter or 25.78 kg of regolith. 50 mm what would result at a fill ratio from minimum 50% in 21.72 liter or 32.58 kg of regolith. First of all, the scoops should be designed so that blockages can be prevented. The advantage is that useless spar space at any given position of each section of the bucket drum is reduced to a minimum in correlation with the average granulation of the lunar regolith. Please apologize for the poor visualization. It was great fun to do some number crunching for a real project.
With this file you will be able to print to the moon with your 3D printer. Click on the button and save the file on your computer to work, edit or customize your design. You can also find more 3D designs for printers on to the moon.