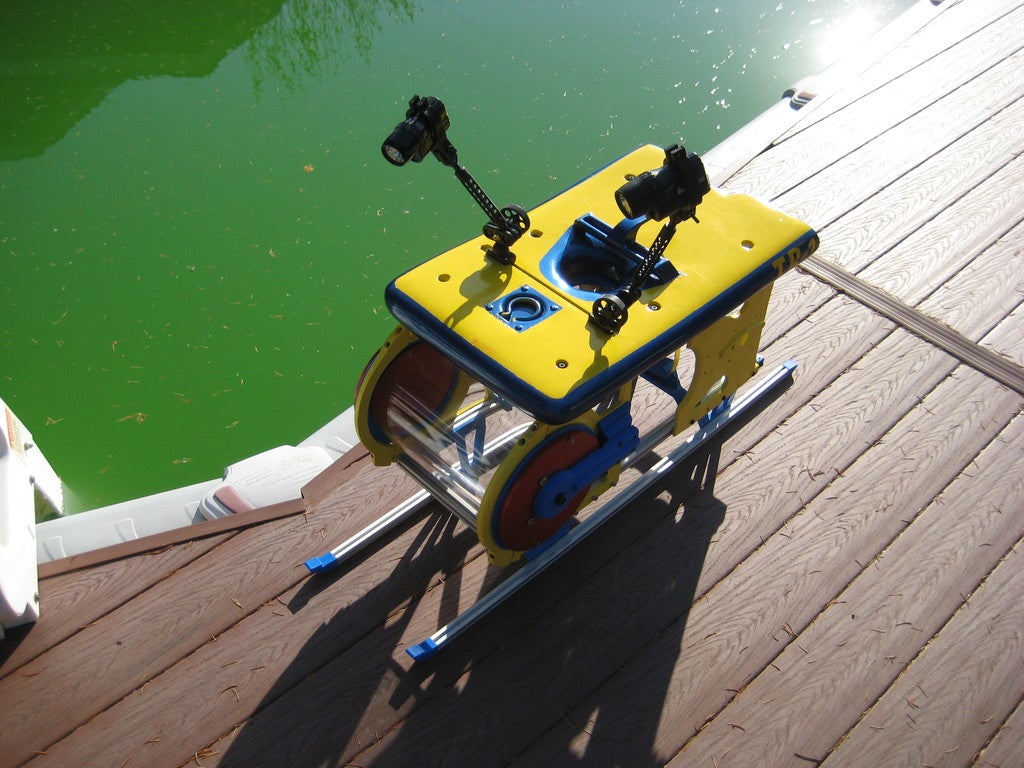
TimROV - An Open Source Scout Class Remote Operated Vehicle
prusaprinters
<p>This is a Scout class ROV designed for printing on a 300mm x 300mm<br/> bed printer, Such as a Lulzbot TAZ or Similar. It is Very much a work<br/> in progress. It is designed to use 4 Blue Robotics Thrusters, the<br/> Electronics package from the Open Source OpenROV, Some Large<br/> clear plastic Tube, and a 3D printer's worth of Aluminum Extrusions<br/> and hardware. This project is not for the faint of heart!</p> <p>Updated the base files, removed the old ones, and uploaded the complete electronics enclosure files.</p> <h3>Print instructions</h3><p>Unassociated tags: #ArtProject, #DesignProject, #EngineeringProject, #EnglishProject, #HistoryProject, #MakerEdChallenge2, #marinearcheology, #MathProject, #RoboticsProject, #ScienceProject</p> <h3>Category: Robotics Summary</h3> <p>This is a Scout class ROV designed for printing on a 300mm x 300mm<br/> bed printer, Such as a Lulzbot TAZ or Similar. It is Very much a work<br/> in progress. It is designed to use 4 Blue Robotics Thrusters, the<br/> Electronics package from the Open Source OpenROV, Some Large<br/> clear plastic Tube, and a 3D printer's worth of Aluminum Extrusions<br/> and hardware. This project is not for the faint of heart!</p> <p>Updated the base files, removed the old ones, and uploaded the complete electronics enclosure files.</p> <h3> How I Designed This</h3> <p><strong>Design of the ROV</strong></p> <p>The ROV was designed to be the largest feasable ROV that could be printed on a large 12" 3d printer, and powered with the new at the time Blue Robotics thrusters. I eventually also determined that the crustcrawler 8" pressure housing was going to be the most economical housing for the front electroncis. From there, I took my basic demension ideas and developed an overall structure: I wanted a ROV that could land on the bottom. I wanted one with a large camera view out front, potential for a robot arm mounted underneith, and a large rear payload area for additional batteries or scientific equipment. It needed to be large enough that it could be useful, but small enough that it could be transported in your average car trunk.</p> <p>I knew from the start that the OpenROV electronics package was going to be the least cost, most support option for a control package, so I designed the pressure hull segments to conform around that option. I also knew that the bluerobotics thrusters were the least cost, most effective option out there for propulsion, so I designed integrated mounts for them as well.</p> <p>I modeled the entire ROV in Autodesk Inventor, then started printing parts out on my Lulzbot Taz 3 at the time printer. Right away it became apperent that I was going to need additional internal structure, so I added more bracing, reinforced the structural hardpoints, then completed the float and took it out for an electronicsless test float. The measurements I aquired from that test let me make some additional changes to the structure and layout for better stability, better skid design and a stronger overall ROV.</p> <h3> Instructions</h3> <p>More instructions to come, for now, you will need 4 2' long 20mm extrusions, 2 3' long 20mm extrusions, 1 pack of Square Buna-N O-rings 7 1/2" OD, One large Acrylic Tube 8" OD 7 1/2" ID, 4 Blue Robotics Thrusters, a 1" diameter strain relief fitting for your teather, and your electronics package of choice. The Thrusters will be a direct bolt on fit to the mounts. Other thrusters may be adapted. You will also probably need some sort of floating buoyancy material, source and type as yet to be determined. All of the parts should print without support. Other part formats are available upon request. Pieces that do not exist yet: 1. {endcap completed) , 2. Tube electronics tray and camera mount, 3. A carrying handle of some sort. 4. A robot arm of some sort - Future project. 5. Some lower cross spars (likely aluminum, not 3d printed). I expect this thing to weigh 7-12 pounds when done, but also to be neutrally buoyant. Please do request any add-ons that would be useful. My intent is to present a small ROV that can be created on a University budget easily and<br/> with plenty of room for upgrades.<br/> The endcap design shown is designed for being milled out of aluminum. I don't think a printed plastic endcap of that size will take the pressure at full depth. That design should work as is for a shallow depth ROV (40 feet and above) but you will need to drill a hole for your cable pass through. I personally plan to use a LEMO series connector for that bit.</p> <h3> Project: TimROV - An Open Source Scout Class Remote Operated Vehicle</h3> <p><strong>Project Name:</strong></p> <p>TimROV - An Open Source Scout Class Remote Operated Vehicle</p> <p><strong>Overview & Background</strong></p> <p>The intent of this project is to prove that a functional 3d printed underwater exploration robot chassis is feasable and within the realm of possibility for most high school and university programs. With the advent of easily available pressure hulls and electronics components, as well as useful and accurate scientific instruments, it is not unreasonable to believe that a program with minimal funding can still provide a platform to collect meaningful and valuable scientific data not otherwise available (water quality at depth, underwater terrein mapping, etc)</p> <p><strong>Objectives:</strong></p> <p>The primary objective is for a student to learn enough to build a functional robotics platform that can operate in the depths required for their project, with sufficient payload capacity to allow for future expansion. A student completing this project will have mastered printing large flat 3d objects (which is in itself a challenge), dealing with buyancy and balast, electrical and propulsion system building and or modification, effective means to implement underwater pressure housings, and computer and control interface programming via the openROV interface.</p> <p><strong>Audiences:</strong></p> <p>This project is a very involved project, and would be best suited for a team of gifted Jr. High to upper level University students. A variety of skills and talents will be required, from basic mechanical assembly, electrical assembly, computer work and upper level 3d printing skills, to advanced fabrication techniques such as use of syntactic foam compounds.</p> <p><strong>Subject(s*:</strong></p> <p>Science, Math, Engineering, Physics, To a lesser degree english and communications (we took the ROV out and found this, now here's our presentation on it!, etc.). Users of the resulting platform may include Life sciences such as marine biology or underwater geology or archeology. Potentially even marine paleontology. Art Too (Painting)</p> <p><strong>Lesson / Activity:</strong></p> <p>This is a large, open ended project with multiple lessons for multiple disciplines. Starting with the build and engineering aspect a class should perform the following steps:</p> <ol> <li>Perform a feasability study. What will it cost to create this ROV. how much plastic, what components, what changes need to be made to perform the mission you would like to embark on. What is your timeline. how will you define success of the project, etc. </li> <li>Depenending on the changes made to the ROV to accomodate your equipment, you should spend a module performing rough bouyancy calculations and structural diagrams to get an idea where you will be at. Will you be running batteries, or using shore power? Lithium polymer or NiCad. How much weight will you need to move around. given that plastic floats, how much additional floatation will you need, and how much will that weigh depending on the depth you wish to reach. Volume calculations for expected crush depth given housing materials, etc. </li> <li>Once you have the calculations and basic plan, it's time to start printing parts and sourcing framework. A module on proper 3d printer operation, bed adhesion and surface finishing is appropriate here. This is an area where a joint project between a science class and a shop class can work well. Print all the parts, and assemble the basic bare frame.</li> <li>Additional components. now that you have a frame, you should begin rough layout of the electrical components, the wiring harness, propulsion, lighting and power subsystems. It is important to fully understand the electrical system, ensure that it is wired safely with proper grounding, provides enough wattage and voltage to do the work you wish it to do, is watertight via passthroughs or potted cables, and meets the needs you have identified for your project. You should have a working electrical diagram before you soldier any components together. Using the OpenROV core there are several assembly and instructional videos and diagrams that can simplify this process. </li> <li>Once the documentation is complete, begin mock up fabrication of the electronics, and test everything before installing it into the ROV.</li> <li>Now that the control system exists, test the thrust ratings of the motors, wet test the bare frame, test the cameras and lighting. Emphasize safety when working with electronics and water at all time. </li> <li>Begin final assembly and testing</li> <li>Perform several test dives in shallow water (pools, etc.) Once you are satisfied you have a viable ROV, begin expedition planning</li> <li>Plan your scientific expedition. Identify a target location and objectives. Obtain permission from any property owners or public agencies if necessary for access, design experements to be conducted on site, and identify reporting and presentation objectives once you return from the field. A senior presentation at the end of the year detailing the construction and resulting expedition would likely be appropriate. </li> <li><p>as an option, I am willing to design custom parts or fittings for the ROV to accomodate any needs of students, and can interact with them via e-mail to show how to collect user parameters for a project, iterate a design, modify that design based off feedback, then provide a final part to be printed.<br/> <strong>Duration:</strong></p> <p>This is a long term project, suitable for an entire simester / trimester, and may be suitible for expansion by subsequent classes (build first, add additional sensors later as needs evolve, then follow up with a science mission simester?)</p> </li> </ol> <p><strong>Preperation:</strong></p> <p>You really need at least one person very well versed in a larger (Taz or similar) bed 3d printer to make this project a success. You will also need a suitable printer. You should expect to expend between $1k-$3k worth of materials (plastic, pressure housings, thrusters, electronics, syntactic foam float beads depending on how much you can get donated or repurpose from other sources.</p> <p><strong>References:</strong></p> <p>Here are a handful of good ROV references. The ROV book listed is the difinitive resource on the subject, and is well worth owning for the instruction. The other pieces are good examples of additional resources or other similar projects in an educational setting that may be used for a ROV design project.</p> <p>http://www.amazon.com/Underwater-Robotics-Science-Design-Fabrication/dp/0984173706/ref=sr\_1\_2?s=books&ie=UTF8&qid=1463435411&sr=1-2&keywords=rov+design<br/> <a href="http://www.openrov.com/">http://www.openrov.com/</a><br/> <a href="http://www.rov.org/rov_design_propulsion.cfm">http://www.rov.org/rov\_design\_propulsion.cfm</a><br/> <a href="http://www.homebuiltrovs.com">http://www.homebuiltrovs.com</a><br/> <a href="http://seaperch.mit.edu/docs/AdvancedROV/FrameDesign.pdf">http://seaperch.mit.edu/docs/AdvancedROV/FrameDesign.pdf</a><br/> <a href="http://www.marinetech.org/">http://www.marinetech.org/</a></p> <p><strong>Rubric & Assessment:</strong></p> <p>At completion of this project, Students should have made a functional ROV and optionally designed custom attributes for it to meet a specific need. They should have printed several dozen quality 3d printed parts, integrated them into a functioning machine, and tested this machine with some scientific results. For grading criteria, if the machine catches fire and explodes, they built it wrong? If multiple ROV's will be constructed, perhaps hold speed competitions to perform scientific tasks underwater?</p> <p><strong>Handouts & Assets:</strong></p> <p>Coming soon!</p> <p>It might be useful to be able to embed links to uploaded PDF's uploaded to this project here if anyone on the dev team looks at this.</p>
With this file you will be able to print TimROV - An Open Source Scout Class Remote Operated Vehicle with your 3D printer. Click on the button and save the file on your computer to work, edit or customize your design. You can also find more 3D designs for printers on TimROV - An Open Source Scout Class Remote Operated Vehicle.