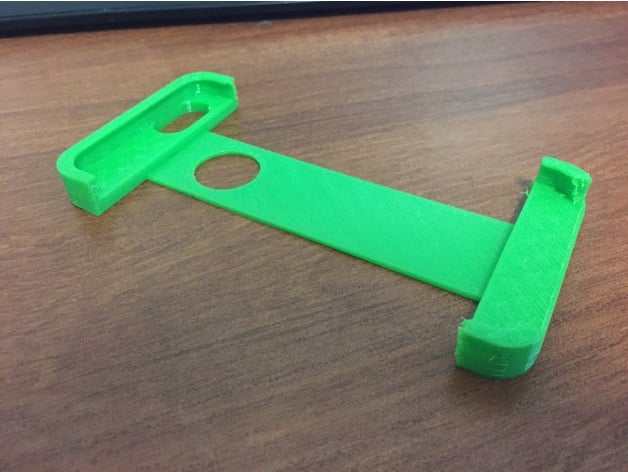
Thin iPhone Case (2 Part Design) (Socket Case) (Iteration 4)
thingiverse
For more designs like this and to see the development of this project, check out my homepage here! (http://www.thingiverse.com/Rubiks_Cubist/about) This is an iPhone 6 case with four hex sockets. The smallest one at the bottom is a quarter inch, the next are five sixteenths, three eighths, and half an inch. There are tick marks on the side of the metal to indicate where the edges of the sockets are even if you can't see them. These marks might be lost in printing. I printed this case with semiflex material and it worked perfectly. The semiflex is harder than ninjaflex so it doesn't slip off the phone case easily, but it still has a rubbery feel. I was worried that the semiflex would not be much better than ninjaflex, so I included a small piece that could fit into the charging port of the phone to add strength on the hold. I also made some design changes to this model. First, because of the ninjaflex's floppiness, I was worried that the semiflex would not be much better, so I included a small piece that could fit into the charging port of the phone, the goal being added strength on the hold. Second, after adding the lip structure, which was just an quarter-circle arc tangential to both the internal side edge and the plane formed by the front face, I would add a small fillet to make the design look better in Inventor. However, on this print, I left out that fillet to try to increase the lip size just a little bit. After printing this, I realize that only making the second change would have been likely sufficient in solving the problems posed by the ninjaflex case. In addition, I later realized that the bridging section in the middle was much thicker in the Z direction than it should have been. I printed the semiflex version with support material on a Ultimaker 2 because I thought there would be drooping otherwise. However, there was so little support material, as the channel was only one and a half mm deep, that I had to sand and scrape just to get some of it off. Eventually I just gave up on removing it and will print it in another form. However, this did cause me to check the thickness of the bridge on the Cast Body part and I was stunned to find that in both the ninjaflex and semiflex versions, the bridge was over two and a quarter mm thick! So on the next version of this, I will make the channel deeper and see if either A) that improves the validity of the support material or B) I can print it without any support material. I used Autodesk Inventor to make this design, and used 2 schematics that I found on Google Images that can be found here. (https://www.dropbox.com/sh/arr8215uvqb5ui5/AAAcxp7K8Z7l7q_B4LfcLZZ9a?dl=0) These images were used for all designs moving forward as well. Comparison of Flexibilities In the three images below, I compared the flexibilities of the three materials. This was my first project printing in a non-standard plastic and so I wanted to share my findings with the 3D printing community at large to help better inform people who are making the same decisions I have been. These better illustrate the differences in the three materials than the simple details given above. Cast Metal.stl Post-Print Details This print was less than ideal, but I was still able to learn quite a bit from it. I printed it as the STL appears in the preview picture, flattest side down. I printed it with support material on a Ultimaker 2 because I thought there would be drooping otherwise. However, there was so little support material, as the channel was only one and a half mm deep, that I had to sand and scrape just to get some of it off. Eventually I just gave up on removing it and will print it in another form. However, this did cause me to check the thickness of the bridge on the Cast Body part and I was stunned to find that in both the ninjaflex and semiflex versions, the bridge was over two and a quarter mm thick! So on the next version of this, I will make the channel deeper and see if either A) that improves the validity of the support material or B) I can print it without any support material. I was happy to see that the tick marks on the outside wall of the socket holes printed well, as I was worried that they may be too small to appear. In addition, the small bit at the top right above the power button does not appear in these pictures because it immediately snapped off following printing. So there is now a new alternative STL file for the Cast Metal design that features a large fillet on the inside corner (that will not interfere with the phone) to allow for a stronger bond. This picture highlights the inset in the back of the metal part, and allows the bridging part of the Body to sit into it and hold the Metal to the phone.
With this file you will be able to print Thin iPhone Case (2 Part Design) (Socket Case) (Iteration 4) with your 3D printer. Click on the button and save the file on your computer to work, edit or customize your design. You can also find more 3D designs for printers on Thin iPhone Case (2 Part Design) (Socket Case) (Iteration 4).