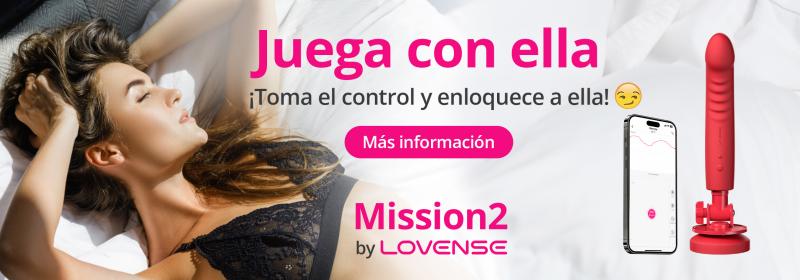
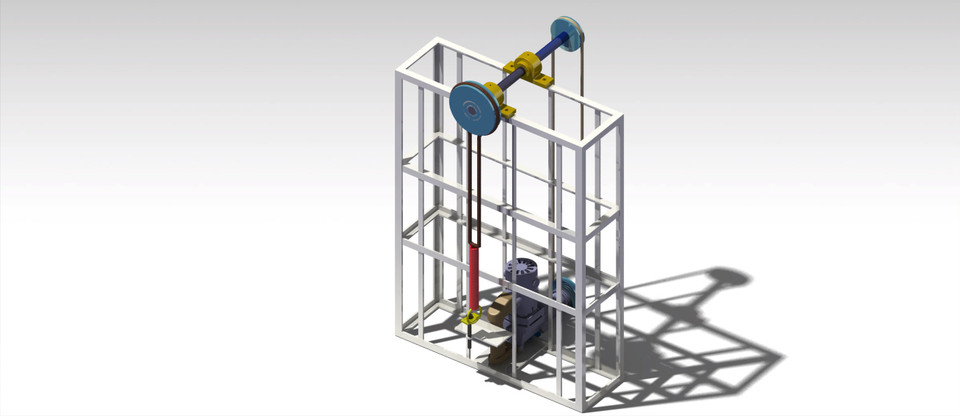
Test Rig - Analysis of Antifriction Bearing Under Different Conditions
grabcad
Human: Rotating machinery is only as safe as its most critical component - the rolling element bearing. A single fault in the bearing's elements due to fatigue or manufacturing errors can render the machine unsafe for operation. Sudden failure of the bearing can lead to serious accidents, economic losses, and wasted time. To prevent such disasters, it's crucial to predict potential faults in bearings before they occur, ensuring timely preventive maintenance of machinery. Vibration-based condition monitoring is an effective method for detecting faults in bearings during operation. In this project, a test rig has been designed and built to measure vibrations in shaft-rolling bearing systems. The test rig development involved designing and manufacturing the shaft, selecting suitable supports and test bearings along with pedestals, belts, pulleys, and motors. Accelerometers captured vibration data for test bearings under normal and defective conditions. Analyzing measured vibrations in the frequency domain helped predict fault characteristics. Vibration generation by bearings is influenced by bearing geometry, load, and shaft speed. This study also examined how defect size, load, and shaft speed impact vibration responses of healthy and defective bearings.
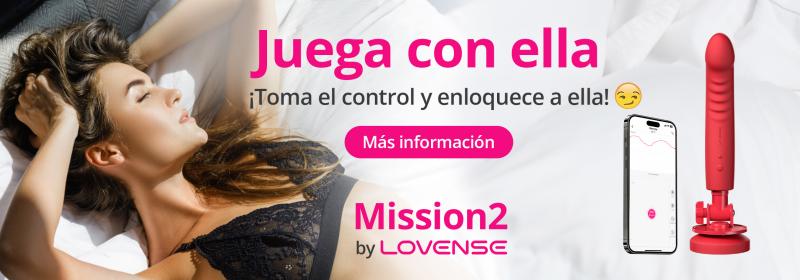
With this file you will be able to print Test Rig - Analysis of Antifriction Bearing Under Different Conditions with your 3D printer. Click on the button and save the file on your computer to work, edit or customize your design. You can also find more 3D designs for printers on Test Rig - Analysis of Antifriction Bearing Under Different Conditions.