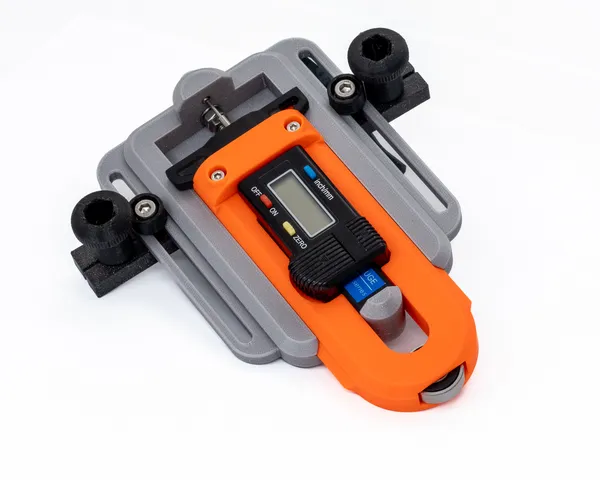
TABLESAW THIN RIP JIG
prusaprinters
Despite the way it looks, this is a very simply tool to print, although some care is needed to insert nuts and a bearing during the process. The following is a step by step set of directions for printing, assembly and use. I shouldn't have to say this, but I will: Tablesaws are dangerous. The jig is intended to safely make very thin pieces of timber veneer. Do not use it as a featherboard or as a fence or tablesaw guide - it's a measuring device! The incorrect use of a 3d printed plastic guide may (almost certainly will) cause injury. Follow these instructions and you SHOULD be perfectly fine, but the risk is yours!PRINTINGI have printed everything in PLA with standard Prusa Slicer Settings 0.2 layer height and QUALITY mode, using a .4mm nozzle.Print pauses for nut and bearing insertion are set up in the attached .3mf files. If you use them don't forget to change the printer and filament to suit your own preferences. I have included some partial files called “INSERT TESTS” so you can check that everything fits without having to print the entire piece. These are not needed for the jig.In the text below I have suggested that PETG would be a good alternative material for the base part and particularly for the slide. My model has had almost no use at this point but I don't think that PLA will be a problem in use, but consider PETG if you have it.HARDWAREUnfortunately we have limited hardware supplies where I live, so there is a strange mis-mash of sizes and kinds that I've had to work with - there's nothing particularly vital if you have to change the odd screw, as long as the embedded nuts are a similar size!The eagle-eyed will notice that some nuts are missing from the photograph below. They are the ones embedded in the part!Runner Two M6 x 15mm Countersunk with nuts and washers for the tensioning (can be longer)Two M5 x 15mm Socket Cap with nuts and washers. Longer is OK, but you'll have to use or print some more washers so the screws don't protrude.Body One M3 x 12 (or 8) Socket Cap with nut (nut to be embedded)One M5 x 65 (give or take) Pan Head with THREE nuts and TWO washers. (One nut to be inserted in Carrier body.CarrierTwo M3 x 12 Socket cap with washers and nuts(to be embedded) and one standard 608 bearing also to be embedded in the print.MEASURING GAUGEYou can easily find this online at your favourite el-cheapo trading website. A Search for TYRE TREAD DEPTH INDICATOR should bring up thousands of hits with prices ranging from a few dollars to almost twice that. Here are some key words copied from one of these advertisements if you are having trouble:<0-25mm Car Tester Checker Digital Motorbike Tyre Tread Brake Pad Depth Gauge> ASSEMBLYAssembly is pretty simple, but the photographs should make it very clear.RunnerStart with the runner. The countersunk screws go in the countersinks from the underside to enable the rail to widen at the split when they are tensioned. In use this will lock the runner.Consider PETG for a slightly more durable rail, but PLA will be quite fine in use. Next insert the washers into the screw spacers and connect the body by locating the screws into the embedded nuts in the rail. The screw spacers are a bit of aesthetic overkill, if you don't want to use them, simply make some washers of sufficient height to prevent the screws going through the underside of the rail, or use shorter screws!BodyInsert the gauge backlash screw into the embedded nut - leave it very slack for now.Insert the adjuster screw as shown below with two washers and two nuts in place.Tighten the nuts carefully. Tight enough so that their is no play fore and aft, but not so tight as to stop the screw can moving freely.Lock the nuts. Use Loktite or similar if you wish, and you will get better results if you use spanners rather than pliers. The internet is not always right!Carrier.Insert one nut for the adjuster screw in the slot in the carrier body. This slot is intentionally very tight to minimise backlash in use . If you have tried a test print you will be confident enough but the nut might need some persuasion or a little heating to sit it home. Mine needed a firm push, more than that will risk breaking the part!Now fit the carrier into the body and slide it in.Thread the adjuster screw onto the body.Snap the Tyre Tread Gauge into the recess in the carrier - it should fit perfectly.Locate the cleat and fix in place using the embedded nuts.Now SLIGHTLY tension the backlash screw. Don't overtighten - it's just to stop any movement in the slide of the gauge. I have deliberately made the base a little thin to allow for a little tension in the body- (I am not sure if that's a good thing - please let me know) overtightening will cause flex and not serve any purpose! INSTRUCTIONS FOR USEUsing the adjuster screw move the gauge until it is just touching a tooth on the leading edge of the tablesaw blade, with the rail tension slack enough so that it can be moved, but tight enough to ensure no movement. Double check that you haven't overtightened to cause the blade to deflect! Zero the scale.Slide the tool along the track until it is about 50mm (2 inches) in front of the blade and lock it into place. Now adjust the gauge (using the adjuster screw) to set the thickness of veneer you wish to cut.With the workpiece between the fence and the jig, carefully move the fence until the timber is stopped against the bearing on the jig.Note: The jig is a measuring device NOT a cutting guide - use the fence to guide the timber in the normal manner. After the cut use the fence to move the workpiece against the jig and repeat.This method is for ripping very thin veneers only where stability could be an issue ripping between the fence and blade in the manner used for normal cuts. The change-over point depends on many variables, but I certainly wouldn't be using this method for cuts of more than say 8-10mm where normal featherboards and pushsticks can be safely used.Here is the result of the first cut with this jig. An accuracy of .01mm was a fluke and not realistic in normal use in my opinion, but I have a need to share my joy! A tiny splinter lifted from the grain will create greater inaccuracy than that, BUT it does work and enabled me to quickly make repeated cuts within ± .05 (a 0.1mm range) was impressive. NOTE that this was with a very short sample piece on a well tuned saw using a fine toothed blade - as they say in the brochures - your results may differ!
With this file you will be able to print TABLESAW THIN RIP JIG with your 3D printer. Click on the button and save the file on your computer to work, edit or customize your design. You can also find more 3D designs for printers on TABLESAW THIN RIP JIG.