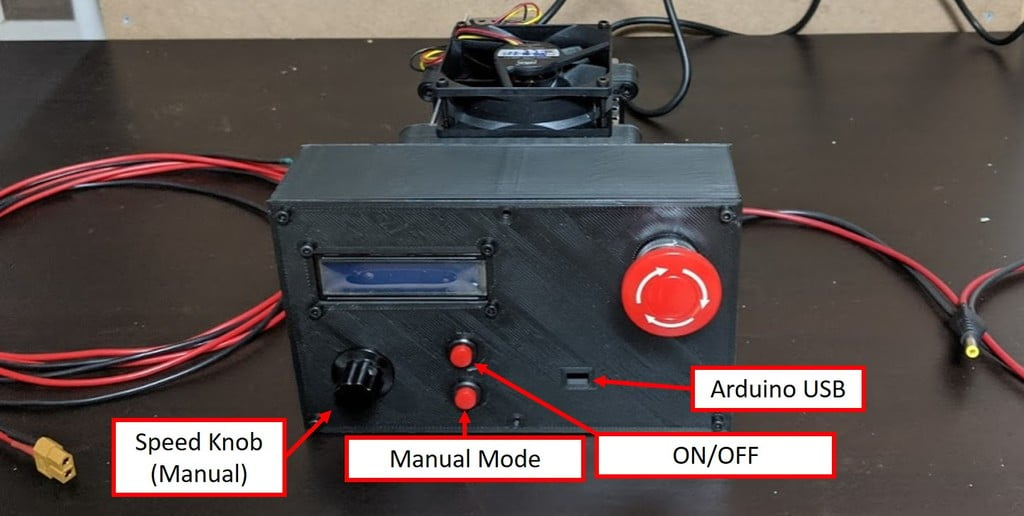
Spindle Control and Power Box
thingiverse
WARNING: This is a non-isolated PSU for the 500W spindle. Be cautious when working with high voltage, as it can shock and kill. Also, when plugged in, the back near the plug has line voltage, so always unplug before wiring or servicing. Not responsible for injury or death. I advise grounding the CNC frame to trigger the fuse instead of your body. FINAL UPDATE 1/31/2020: TLDR; Don't make this, instead make -> https://www.thingiverse.com/thing:4198567 Sometimes it's more important to admit when you did something that wasn't very useful... I learned a lot about noise and electronics. I mostly use manual mode, which negates most of the electronics. Knowing RPM isn't as useful as I thought since sound is more important than a number on an Excel sheet from the last board. As for vibrations, slap some googly eyes on your router and they start jiggling - you know you have chatter and feed-speed issues along with the sound. Eventually, I'll strip out everything but the relay and kill switch and print a new cover for just a push button, manual control knob, and kill switch. The kill switch will kill line voltage of the box. The relay will be a multi-throw 12v relay that turns on mains voltage to the drill and vacuum. UPDATE 8/26: New PCB works. I uploaded BOM and Arduino code. Still need to debug PWM reader from CNC and Hall sensor code, but that requires more parts. This point is good enough; going to take off the work-in-progress. Will update if I fix bugs. UPDATE 8/11: Updated PCB and waiting on next delivery from JLCPCB.com. Will post Build Guide after second attempt works and get the code finished. Added spacer between back plate and front plate for room to new PCB and more wires. UPDATE 7/29: You build, you learn... Optocoupler works great. I needed to adjust MAX voltage screw in PSU to get 100 volts at 100 PWM signal, but it all worked out good. I should have used a pull-up resistor configuration on my buttons. Also, the PWM signal from Ramps is actually on the ground side, so my whole voltage divider is dumb. Will design new PCB after I test to make sure I didn't screw up Hall sensor. UPDATE 5/28: WARNING: After starting into circuits, learned this is a non-isolated PSU for 500W Chinese spindle. That means you cannot connect it to your Arduino and then computer. There were some angry pixies... Hella super angry pixies. Also, at zero volts on controller, you're really floating at line voltage, so treat the spindle cabling as if it were a wall socket with angry pixies. I plan on using a relay module and optocoupler for cutoff and speed control respectively. Still working on repairing fuse and new Arduino Nano... RIP little buddy. ORIGINAL TEXT: Wanted to mount power supply boxes in a neater configuration. Was using (https://www.thingiverse.com/thing:3353444) which was great, but I had lots of boxes laying around my space with cables and all the power cords staring at me straight in the face. Consolidated two PSU boxes for MPCNC and added upgrades for spindle control. Goal is to - Allow both manual and G-code spindle control, Measure RPM directly with hall sensor on spindle and calculate load, Possibly adjust Spindle voltage to target RPM commanded, Display all this data on a pretty LCD controlled by Arduino Nano. All lofty goals requiring me to sit down and finish the circuit. So work in progress because I'd like to get back to cutting things so really Kill Switch and manual control is only implemented. Need to print 2 PSU brackets. Those are locked in place by screws attaching fan and two holes in bottom that should attach case. Then the back, spacer, and front are screwed on to bracket. As usual with me... poorly hacked together FreeCAD file attached so you can modify to how you want.
With this file you will be able to print Spindle Control and Power Box with your 3D printer. Click on the button and save the file on your computer to work, edit or customize your design. You can also find more 3D designs for printers on Spindle Control and Power Box.