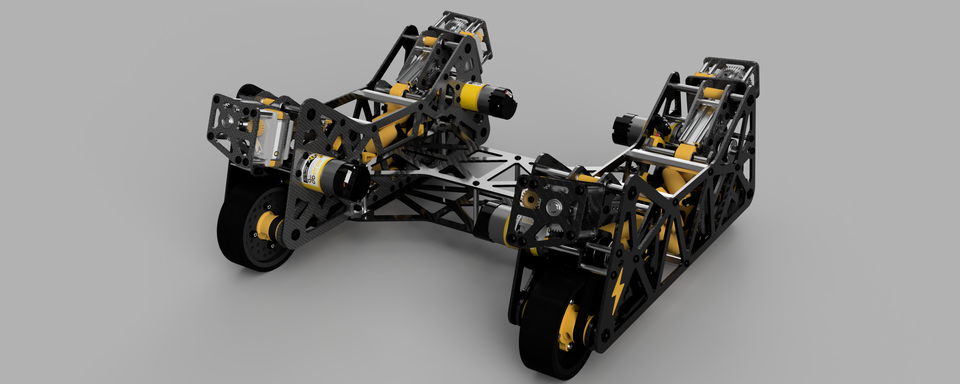
Spark Chassis (Carbon Fiber Octacanum)
grabcad
The Spark chassis is (to my knowledge) the first full carbon fiber, lead screw-driven, FTC legal octacanum design to be published on the internet. Octacanum drives work by utilizing two sets of wheels; a rubber set for traction and power, and a mecanum set for agile and holonomic movement. The greatest challenge in the design of an octacanum is the quick "swap" that needs to be made between the two wheel sets. Most designs address this aspect using DC motors, hydraulic, or pneumatic actuation methods. These systems won't work in FTC, since hydraulics and pneumatics are illegal, and using more than 4 motors for a chassis is generally considered a waste.For its actuation, the Spark uses lead screws that are driven by Gobilda "torque" servos. Taking account of these servos' stall torque and the mechanical advantage of the linear mechanism, the chassis will only stall once the robot weighs a total of 4184 pounds. Even if we assume a high frictional loss of 50%, the robot can still weigh more than 2000 pounds before stalling. Each powerful wheel module has been optimized for horizontal compactness, which creates ample room in the center of the design for a potential ground intake.Two limit switches are used for each wheel module, to accurately and reliably unsure proper contact of all four wheels. These switches are mounted in slots to allow for manual tweaking of the positions. They contact 3D printed switch pressers that are mounted on each drive module. If major changes need to be made to the "up" or "down" position, it is much simpler to adjust the design of these pressers, rather than trying to move the mounting holes of the limit switches in the carbon fiber panels.Considering the price of 2.9mm carbon fiber, the chassis is priced at at least several hundred USD. Fabrication requires at least a 3D printer, a CNC router (though preferably a CNC waterjet), a lathe, a saw that can cut metal, a drill, a tap, and a counter-bore bit. All stock components can be purchased from McMaster-Carr and Gobilda.The Spark was influenced by octacanum designs made by FRC team 5987 and FTC team 2939, and designed in Fusion360.
With this file you will be able to print Spark Chassis (Carbon Fiber Octacanum) with your 3D printer. Click on the button and save the file on your computer to work, edit or customize your design. You can also find more 3D designs for printers on Spark Chassis (Carbon Fiber Octacanum).