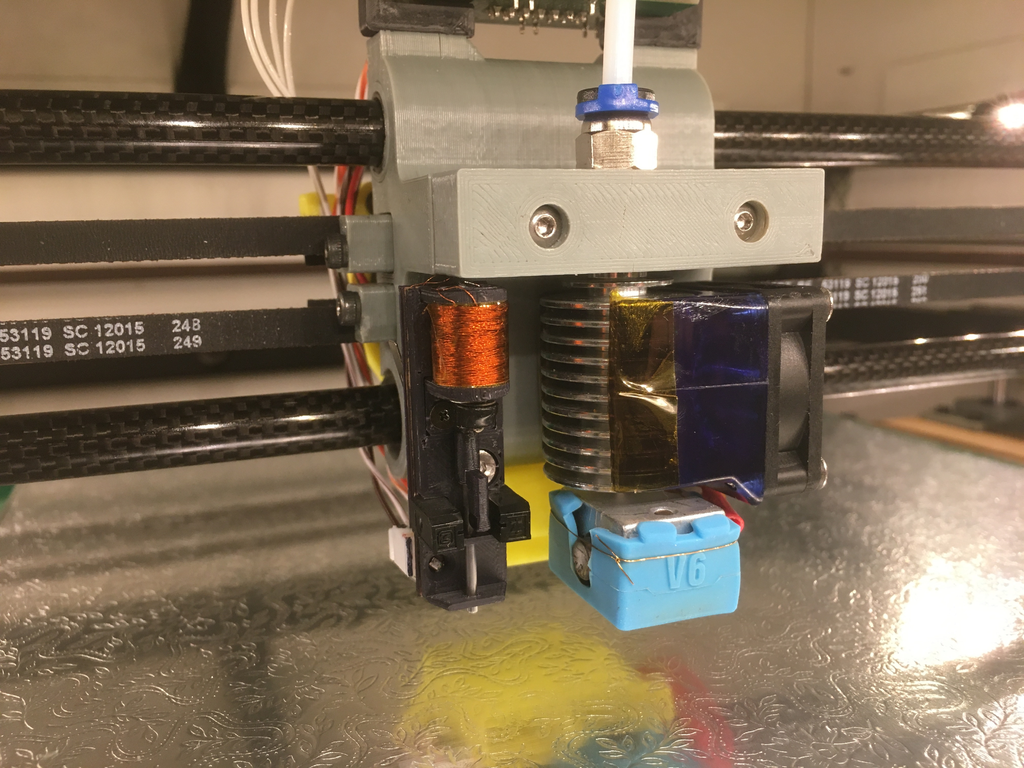
Solenoid Probe
thingiverse
This remix utilizes an electromagnet to drive the plunger. Detection relies on a photo-interrupter. The ATtiny13A controls the H-bridge, which powers the electromagnet. Plunger displacement measures 7mm. It triggers at 4mm, and retracts 3mm above the nozzle, showcasing high accuracy. Additional details: The part is not publicly available because it's highly specific to my printer setup and mounting location, making it of little use to others. The details are provided for those who want to replicate it for their own printer. **Electronics:** The circuit diagram and ATtiny13 code are included in the files. Initially, I planned to use servo signals, but in the heated chamber, the tiny13 internal RC clock drifted significantly, rendering accurate angle measurements unreliable. It's better to use an external Xtal oscillator-based part like Tiny2313 for that application. The current code simply expects a High/Low signal and stows/deploys the probe. This setup can operate at temperatures up to 80 degrees Celsius, which is the rated temperature of ATtiny13A. All other components can handle temperatures up to 160 degrees. In Klipper, I define the following configuration: ``` [output_pin PROBECONTROL] pin: ar15 pwm: False value: 1 shutdown_value: 1 [probe] pin: ^ar19 x_offset: -25.0 y_offset: 0.0 z_offset: 4.0 speed: 5.0 lift_speed: 20.0 activate_gcode: SET_PIN PIN=PROBECONTROL VALUE=0 G4 P150 deactivate_gcode: SET_PIN PIN=PROBECONTROL VALUE=1 ``` **Solenoid and Probe:** All parts are printed in ABS plastic. The printed solenoid core is a hollow 3mm diameter with 1mm wall thickness. It's wound from 0.14mm enameled copper wire, approximately 24 meters long. The coil resistance is 25 ohms, resulting in a current draw of 200mA for 100ms when the coil operates. The wound coil length measures 10mm. An M3 screw at the top secures the stowed plunger. It needs to be adjusted so that it's not touching the plunger or else the probe won't deploy - the electromagnet has less repulsive force compared to the magnetic attraction of the 5mm rare earth magnet used. **Plunger:** It's made from 2mm iron wire. A 5mm rare earth magnet is glued to the top, followed by another 10mm section, which moves in/out of the solenoid. In the fully deployed position, it's still 3mm inside the solenoid. This design choice was made because I didn't have a 2mm weak magnet that could be directly glued to the plunger's top. Care must be taken to ensure the solenoid doesn't physically touch the grab screw at the top when pulling the plunger in. Once deployed, gravity keeps it down. A flag mounted on the plunger interrupts the light path when the plunger moves up as a result of touching the bed plate. If anything else is unclear - ask away; I'll try to answer.
With this file you will be able to print Solenoid Probe with your 3D printer. Click on the button and save the file on your computer to work, edit or customize your design. You can also find more 3D designs for printers on Solenoid Probe.