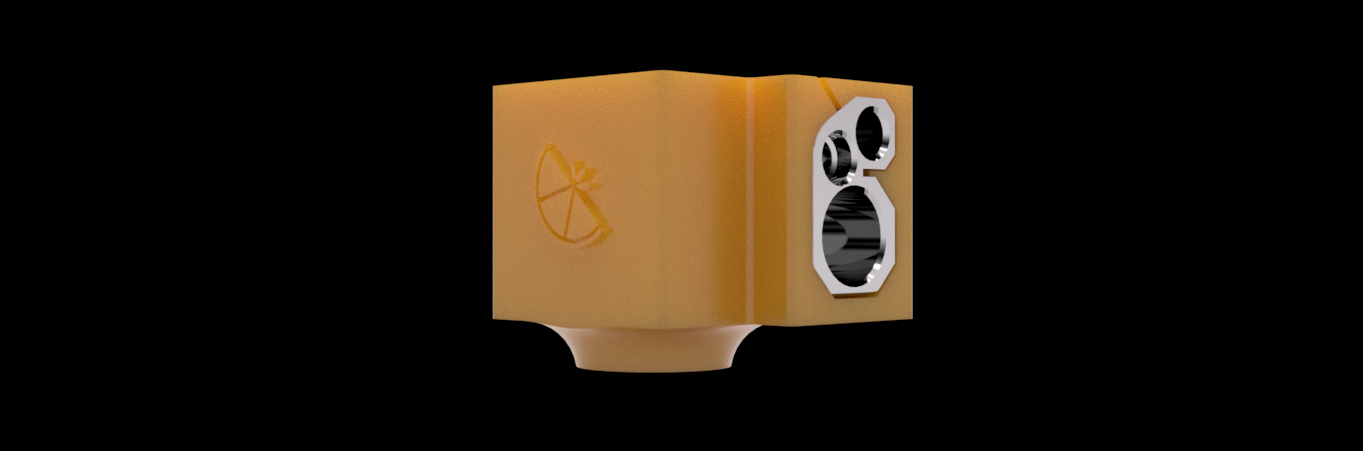
Slice engineering Copperhead silicone sock mold
prusaprinters
<p>Having backed the Slice engineering Copperhead on Kickstarter I found myself in need of a silicone sock for the hotend. As Slice do not sell socks I decided to cast my own using the ever awesome @CNC_Kitchen's video as a guide.</p> <p> <figure class="media"> <oembed url="https://www.youtube.com/watch?v=O5UiXky85hA"></oembed> </figure> </p> <p>The mold consists of 6 parts, 2 of which are optional. When designing the mold I was unsure if I would achieve a good seal between the printed PLA parts so I designed a groove to accept a printed TPU seal. After testing I found that the seal isn't really required as providing your print quality is good, the compression from the bolts is enough to generate a liquid tight seal. I have included both variants so if you are confident and don't want to use the TPU seal please print the "lid" and "side" marked with the NO SEAL suffix. The "base" and "hotend" parts are common to both.</p> <p>Instructions:<br/> Print the required parts and collect the materials as listed in the BOM below.</p> <p>The "hotend" part can be glued to the "lid" or just left as a push fit. I personally prefer leaving it push fit as I find it easier to remove the sock afterwards. Next bolt the lid and side to the base. There is no need to over tighten these, the silicon is very viscous so you don't need a huge force to get a good enough seal.</p> <p>Once assembled, mix your silicon as per the manufactures' instructions (adding pigment if desired). I recommend that you mix a minimum 15 ml of silicone even though the mold only takes about 5 ml to fill. The reason is we will have to use extra silicone to purge any air from the mold plus some will be stuck to the mixing container walls.</p> <p>Suck the silicon into the syringe (see CNC Kitchen video for tips on removing air inside the syringe) then hold the mold on its side so that the small vent hole is at the top and the injection hole is at the bottom. Insert the syringe into the 4mm hole and slowly inject the silicone. Eventually silicone will flow from the vent hole, keep injecting until you see no air bubbles escaping from this hole.</p> <p>Leave to cure as per silicone manufacturer instructions (typically 1 to 2 hours depending on ambient temp).</p> <p>Once cured, dissemble the mold and carefully pull out the sock. There will be some minor flash that will need to be cleaned up which is sadly unavoidable with printed molds.</p> <p>Fit to your hotend. The best method is to fit the front first then the rear. It should be a snug fit and should not sag at all. If not, you may have to scale the mold to match you printers accuracy.</p> <p>Enjoy keeping you Copperhead warm and gunk free!!</p> <p>BOM<br/> In addition to the printed parts you will also need:<br/> M3 x 40 bolts x2<br/> M3 x 30 bolts x2<br/> M3 nut x4<br/> 10 ml syringe<br/> High temp silicone<br/> Silicone pigment (optional but a nice touch)</p> <p>I have included the STEP files so please feel free to modify them to your needs. This is my first shot as designing a mold so i'm sure there are many improvements that could be made. If you find a better way of designing it please post it up for all to share.</p> <p>UPDATE - 06/06<br/> I've added a small finger recess on the "side" for ease of removal post cure.</p> <h3>Print instructions</h3><p>I printed the mold with a 0.25 mm nozzle @0.1 layer heights to improve the look of the finished part - Any print artefacts or layer lines in your print will also be present in you silicone sock.</p> <p>I've not tested this with a 0.4 nozzle, I assume the slice logo may degrade a little at that resolution but overall the mold should still work well.</p> <p>WARNING - The parts as designed with a clearance of 0.15 mm so if your machine struggles with tight tolerances you may have to scale the parts accordingly.</p> <p>I have included the .3MF file so you can see how I orientate the parts on the print bed as a guide but other orientations are possible.</p>
With this file you will be able to print Slice engineering Copperhead silicone sock mold with your 3D printer. Click on the button and save the file on your computer to work, edit or customize your design. You can also find more 3D designs for printers on Slice engineering Copperhead silicone sock mold.