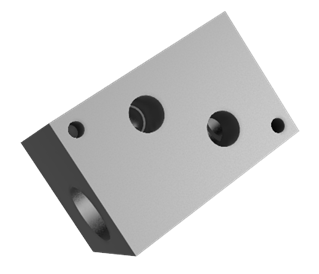
Shape optimization of hydraulic manifold in Fusion 360
grabcad
AM allows for the creation of more complicated shapes, both for surface forms and internal structures, resulting in greater product performance and weight reduction. In this aspect, AM allows for the building of highly complex structures using generative design and topology optimization to meet specific technical goals.One of the clients from a hydraulic manifold manufacturer has asked us to optimize/redesign a small hydraulic manifold block for weight reduction. A hydraulic manifold is a device that controls fluid flow between pumps, actuators, and other components in a hydraulic system, and it is frequently used at high pressures.Firstly, hydraulic manifold is inserted into the design space in Fusion 360. Then stimulation module is used with shape optimization feature.Firstly, material is selected from Fusion library i.e., Stainless steel 316L. Then structural constrains and forces are applied as required for model and operation. Further, shape optimization geometry is selected. In this section. Mass, stiffness, preserve regions and symmetry plane is used to manipulate the current design which fulfil the same functional requirement as original model. Then model is generated to get the optimized shape. Generally, mass is selected in percentage. The Preserve Region tool enables you to hide certain regions of your model from the Shape Optimization analysis.For this hydraulic manifold two models are optimized. The difference between two models is between preserve regions and mass percentages. Different models are achieved after shape optimization in terms of mass and shape of model.
With this file you will be able to print Shape optimization of hydraulic manifold in Fusion 360 with your 3D printer. Click on the button and save the file on your computer to work, edit or customize your design. You can also find more 3D designs for printers on Shape optimization of hydraulic manifold in Fusion 360.