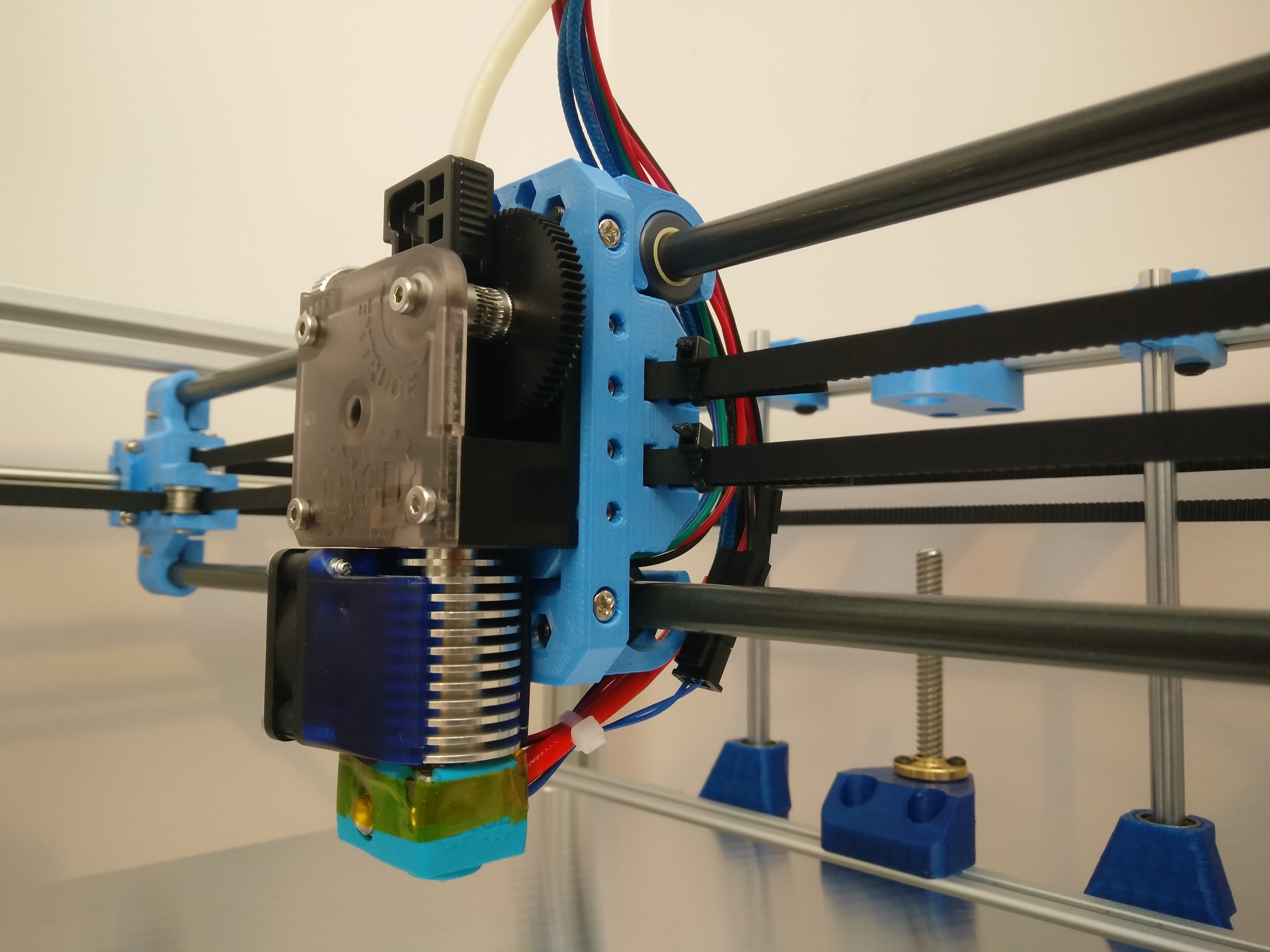
S.T.E.V.E - CoreXY 3D Printer
prusaprinters
<p>Want to know more about the design and assembly process?<br/> <a href="https://www.youtube.com/playlist?list=PLWL37f39O8e8jSmrYGKiWX6iMkNlrfwSp">https://www.youtube.com/playlist?list=PLWL37f39O8e8jSmrYGKiWX6iMkNlrfwSp</a></p> <p>Join the Facebook Group for discussion + Q&A + Future updates and upgrades<br/> <a href="https://www.facebook.com/groups/266957403761491/">https://www.facebook.com/groups/266957403761491/</a></p> <p>See the full Bill of Materials with supplied links here: <a href="https://docs.google.com/spreadsheets/d/1FVdSh7WRvvxo3kc_i1Jvbl6kwNt3XSbQIA1PcNw0xOk/edit#gid=0">https://docs.google.com/spreadsheets/d/1FVdSh7WRvvxo3kc\_i1Jvbl6kwNt3XSbQIA1PcNw0xOk/edit#gid=0</a> (some affiliate links included but buy from wherever you feel comfortable)</p> <p>S.T.E.V.E is an open source, single extruder, easy to modify 3D printer with a approx 240mm cubed build volume and CoreXY Kinematics. When starting to design S.T.E.V.E I just wanted to learn more about the CoreXY kinematics but things got out of hand, one thing lead to another, and I ended up designing an entire printer that I wanted to share.</p> <p>He was designed with the intention of every part being easy to purchase or print, and easy to build with assistance of detailed instructions with very little needed in terms of tools. (For best results a drill and 3.5mm bit plus crimping tool for red crimp terminals would be ideal. You can probably survive without.) The obvious allen keys are also needed.</p> <p>Instructions are currently in the form of PDF drawings and an extensive video guide. All the video links are down below. Some show some information about the design process, while the others explain how to assemble the printer.</p> <p>One of S.T.E.V.E's most unique features is the gantry head assembly. It ensures that the centre of mass of the stepper motor is aligned as closely as possible to the rods to reduce torque on the bearings and improve print quality. The same assembly provides a modular system for adding, changing or removing different features from around the hot end such as cable management, fans, bed sensors etc.</p> <p>While this isn't a remix, i'll give some credit to Tech2C and his hypercube printer. I did borrow a couple of design aspects such as the clamps used for round rods.</p> <h3>Frame</h3> <p>S.T.E.V.E's frame is constructed from standard 6mm slot 2020 aluminium extrusion, held together with M5 x 8mm Button head screws and 90 degree angle brackets. All easy to get and easy to assemble.</p> <p>One key design feature of S.T.E.V.E is that all the components are kept within the rigid 2020 aluminium frame so that it is simple to enclose the printer to form a heated chamber for printing of more exotic materials. (heat resistant plastic parts also recommended)</p> <h3>Steppers</h3> <p>S.T.E.V.E uses a total of 5 NEMA 17 stepper motors, a 13Ncm pancake stepper for the extruder, 4 45Ncm D shaft steppers for the X, Y and Z motion.</p> <h3>Control Board</h3> <p>The selected control board for version 0.1 of S.T.E.V.E is the RAMPS 1.4. This will be upgraded in the future as RAMPS was mostly for prototyping.</p> <h3>Heated Bed</h3> <p>The bed is 6mm tool plate aluminium which is ideal as it has high thermal conductivity and won’t warp overtime becuase of the way it was manufactured. The Heating is provided by a 330W 230V silicon heater with a built in thermal cut off at 180C for safety (set RAMPS max to 150C).</p> <h3>SSR</h3> <p>Because the bed heater is powered through mains voltage a Solid state relay is used to control power to the bed. The low voltage side of the SSR is attached to the control board as normal and acts like a switch.</p> <h3>Hotend and Extruder</h3> <p>S.T.E.V.E uses the E3D v6 full metal universal hot end and titan extruder with a 13Ncm stepper motor to provide a lightweight, versatile and reliabile print head.</p> <h3>Power Supply</h3> <p>Since the power supply is only for the stepper motors and hot end, there is no need for 300-400W power supplies. A high quality 12V unit that can supply 80-100W should be more than enough. Closet to 100W if you want some LEDs in there too.</p> <p>Special Note: Recently i have noticied that the aluminium rods for X and Y are a little too flexible. I am going to test putting Steel rods on the Y axis and see how that does. Might have to upgrade the X axis to 10mm Aluminium or 8mm steel for rigidity. Will keep you updated.</p> <p>Special Note 2: Not sure what makes these notes special but i have tested with 8mm steel on the X and Y axis. I have had good results with 8mm steel rods on both axis.</p> <p>Final Note: Work on STEVE mk2 is now starting. In order to finish off mk1 I have uploaded a zip file (STEVE update Parts) containing a number of files that I considered unfinished work. These are all parts I was working on and are probably usable but not necessarily better. Up to you what you decide to use but I thought I should share them.</p> <h3>Print instructions</h3><p>Unassociated tags: 2020 3d printer, 2020 frame, 3d printing, power supply, psu enclosure, S.T.E.V.E, silicon bed</p> <h3>Category: 3D Printers Print Settings</h3> <p><strong>Printer:</strong> Any Printer will do</p> <p><strong>Rafts:</strong> Doesn't Matter</p> <p><strong>Supports:</strong> No</p> <p><strong>Resolution:</strong> 0.2-0.3mm</p> <p><strong>Infill:</strong> 30-50%</p> <p><strong>Notes:</strong></p> <p>I'm not going to list precise details for how to print every part. They are all fairly simple geometric shapes with quite obvious indications of how they should be printed. I printed all of mine without support so you should be fine to do that too. Try to print all the load bearing parts with a good infill to ensure they will be strong enough.</p> <p>For the material it depends on what your end goal is. If you want to end up almost fully enclosed then you'll need to use ABS or perhpas ASA. If you don't want fully enclosed then PLA or PETG would be fine. Personally i'm running all PETG at the moment. It will probably be fine once enclosed too but ABS is a safer bet.</p> <h3> Who is S.T.E.V.E?</h3> <p>S.T.E.V.E is my first full 3D printer creation.</p> <p>The name stands for Superfluous Tri-dimensional Electronic Vector Extruder. The name came about when asking the 3D printing facebook group for name suggestions (yes i know, never ask the internet for name suggestions!) My two favourite suggestions were the name Steve, and making an accronym name such as JACP; Just Another Corexy Printer. So I decided to combine them into a single item and thus S.T.E.V.E was born.</p> <h3> Bill of Materials</h3> <p><strong>V0.01</strong></p> <p>In the files list there a BOM file. A full list of parts needed for the base spec of S.T.E.V.E. I highly recommend you take a look at the PDF drawing files to get an idea of what is used where. If you want to use slightly different bearings then the PDF drawings are also a great way to get an idea of what you need to change.</p> <h3> Video Build Overview</h3> <p>The whole playlist - individual videos below for specifcs</p> <pre><code> Version Notes </code></pre> <p>=============</p> <p><strong>Version Notes</strong></p> <p>X Gantry End v0.2 - Slightly increased M3 clearance hole sizes and thickness around idlers. Not compatible with X Gantry Bearing Clamp v0.01.</p> <p>X Gantry Bearing Clamp v0.2 - Split into two parts. Improved clearance to enclosure walls. Easier to print. Print in orientation provided. 4 required.</p> <p>Marlin Firmware v0.2 - Added feature to use second extruder output on RAMPS as second Z motor and fixed some bugs.</p> <p>X Gantry End - LM8LUU_0.2 - improved version of the LM8UU X gantry end. only minor changes. backwards compatible. New Bearing clamps needed.</p> <p>X Gantry Bearing Clamp - LM8LUU_0.2 - Required for X Gantry End - LM8LUU_0.2. Lower profile two part bearing clamp for each end of the X Gantry.</p> <p>Gantry Head LM8LUU Bearing Holder_0.2 - Bearing clamps for the X axis gantry that use LM8lUU instead of IGUS bearings. Use one LM8LUU and one LM8UU</p> <h3> Unofficial Mods and Remixes</h3> <h3> Mods</h3> <p>Here are some of the mods for STEVE that you might want to try if you think the standard design is not quite right for you. I have not tested them personally so if you need assistance, speak to the mod/remix designer.</p> <h3>E3D V6 Bowden Mount</h3> <p>If you want to use an e3d v6 bowden setup with STEVE, this mod will allow you to attach directly to the stepper motor mount with additional support for a bed sensor and part cooling fan.<br/> <a href="https://www.thingiverse.com/thing:2333612">https://www.thingiverse.com/thing:2333612</a></p> <h3>XY Joiner for 10mm Gantry rods and IGUS RJZM bushes</h3> <p>If you want to upgrade the X axis gantry to 10mm rods, leaving the Y axis with 8mm then this is what you need to do it.<br/> <a href="https://www.thingiverse.com/thing:2363021">https://www.thingiverse.com/thing:2363021</a></p> <h3>X and Y Modified Endstop</h3> <p>If you don't like the standard positioning of the STEVE endstops, why not try this mod that allows the Y end stop to be mounted directly to the frame, and the X endstop to be mounted on the X gantry itself.<br/> <a href="https://www.thingiverse.com/thing:2378271">https://www.thingiverse.com/thing:2378271</a></p> <h3>A-senco SSR-500 case</h3> <p>If you opt for a slightly different model of SSR then you might find this mod helpful as the original one might be just a little too tight.<br/> <a href="https://www.thingiverse.com/thing:2378306">https://www.thingiverse.com/thing:2378306</a></p> <h3>12 mm Z Axis Shaft with LM12LUU</h3> <p>I have made a 12mm Z axis option, everything else about it is the same, just the larger diameter. Print the equivalent parts with '12mm' in the name. There are two modified files for this.</p>
With this file you will be able to print S.T.E.V.E - CoreXY 3D Printer with your 3D printer. Click on the button and save the file on your computer to work, edit or customize your design. You can also find more 3D designs for printers on S.T.E.V.E - CoreXY 3D Printer.