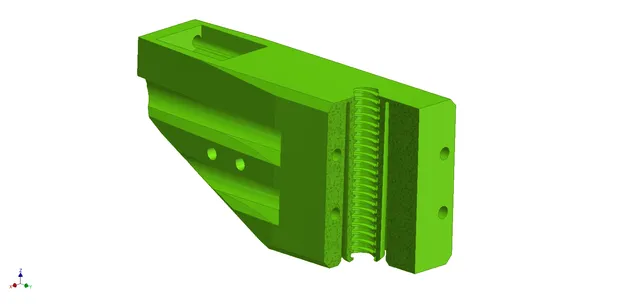
RatRig V-Core 3 Flexlink arms -> Z-wobble compensation
prusaprinters
The main purpose of these arms is to reduce z-wobble artifacts on V-Core 3 printers due to bent or not perfectly aligned leadscrews. It uses a printed acme 8x4mm nut, which is integrated into the arms. My idea was to use the natural flexible properties of the plastic material. The coupling between the nut and the arm is a 0,8mm thick link, which is strong enough to withstand the weight of the heated bed, but flexible enough to allow an amount of wobble movement of the nut relative to the arm. This way a high amount of the x-y and twist/torsion force - generated from the wobbly movement of the lead screw - can be compensated out, which will not go into the arm itself, therefore the arm body will not be dragged along by these forces and the heated bed will stay more stable during Z-movement.Basis of this modification are the original arms designed by RatRig.The rear arm is designed with a centralised leadscrew. Therefore you need to use a centralised lead screw motor cage, like Liam Venter's centralised rear anti-flex motor cage: https://www.thingiverse.com/thing:5066883Instructions: The nut is integrated into the arm via the flexlink as a one-piece print, so no additional parts are required.the arms have to be mounted to the linear rail carriage with:M3x30mm screws for the left and right armsM3X35mm screws for the rear armuse M3 washers!PLA is an excellent choice for this application, choose one with good layer adhesion and with a flexural modulus between 2500 and 3500 Mpa. My choice was 3DJake tough PLA: https://www.3djake.com/3djake/ecopla-tough-blackPETG might be a good option as well, but keep in mind the 0,8mm flexlink, which is basically responsible for the coupling between arm and the nut. PETG is a softer material, therefore creeps more, especially on higher temperatures.I do not recommend this upgrade in connection with a heated chamber! The flexlink might be get softer, breaks and the bed will fall off. I did not tried this for obvious reasons (and I also dont use a heated chamber).I do not recommend to use ABS for the arms, because the lubricant oil on the lead screw will migrate into the plastic and will cause stress-corrosion cracking. This is only the case with 2-phase plastics, typically ABS. PLA and PETG are not affected.Print the arms with 0,15mm layer height and a 0,4mm nozzle. The printed 8x4mm acme thread has a tight fit, so the level of detail matters.I printed my arms with 6 perimeters and 7 top and bottom layers for the extra strength of the arm body.Still, if the arm is too tight on the thread and it is hard to turn, fix the lead screw into a drilling machine and move the arm back and forth a couple of times with high speed. Use a small amount of lubricant on the lead screw.After 3 months passed… some update about the arms:I was lubricating the threads between arm and lead screw with regular fine-mechanics oil (sewing machine oil), but after some time the arms developed some resonance sounds during fast Z-movement. Then I switched to a PTFE spray lubricant, with wich the resonance was gone, everything went back to normal. The motors can still turn freely, no problems there.
With this file you will be able to print RatRig V-Core 3 Flexlink arms -> Z-wobble compensation with your 3D printer. Click on the button and save the file on your computer to work, edit or customize your design. You can also find more 3D designs for printers on RatRig V-Core 3 Flexlink arms -> Z-wobble compensation.