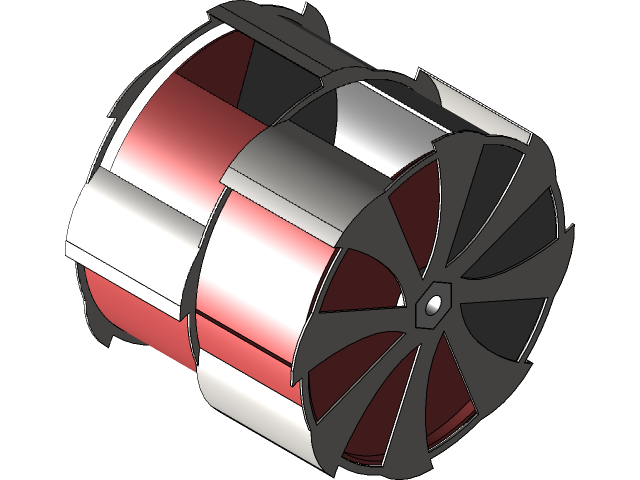
RASSOR drum Challenge Entry
grabcad
This design aims to be lightweight with a rapid dumping function, crucial for Mars missions where energy conservation is key. It collects materials in a way similar to existing designs and holds a maximum of 36.2 liters when fully filled, representing a total build volume fill ratio of 63.2%. When half the internal volume is reached, one-way locking ball bearings are designed to engage. Rotating the bin 110 degrees in reverse opens the bottom, allowing contents to be dumped in a single motion like an excavator scoop. To work effectively, this design requires a mount to secure the stationary drum to the mechanical arm, providing stability and separation during dumping operations. I've marked potential mounting holes on the drive side of the bin for easy installation. This assembly is relatively straightforward to manufacture; the scoop component poses the greatest challenge. Three 8-tooth rings can be cut from material plate stock, with scoop plates welded in an alternating pattern. Ideally, replacement blades could be attached to scoop cups for durability and long-term maintenance. The scoop assembly's approximate weight would be 1.9 kg using aluminum, leaving 3.1 kg for the remaining parts. This means the drum assembly must be composite to meet maximum weight requirements, necessitating further skeletonization. With a total volume of 3594 cc as designed, the drum assembly could be reduced to around 2000 cc, resulting in a ~3.1 kg total drum weight using carbon fiber. Material removal is possible and desirable in many areas; with more time available (I was informed about the challenge on April 18th), I would have achieved this weight reduction.
With this file you will be able to print RASSOR drum Challenge Entry with your 3D printer. Click on the button and save the file on your computer to work, edit or customize your design. You can also find more 3D designs for printers on RASSOR drum Challenge Entry.