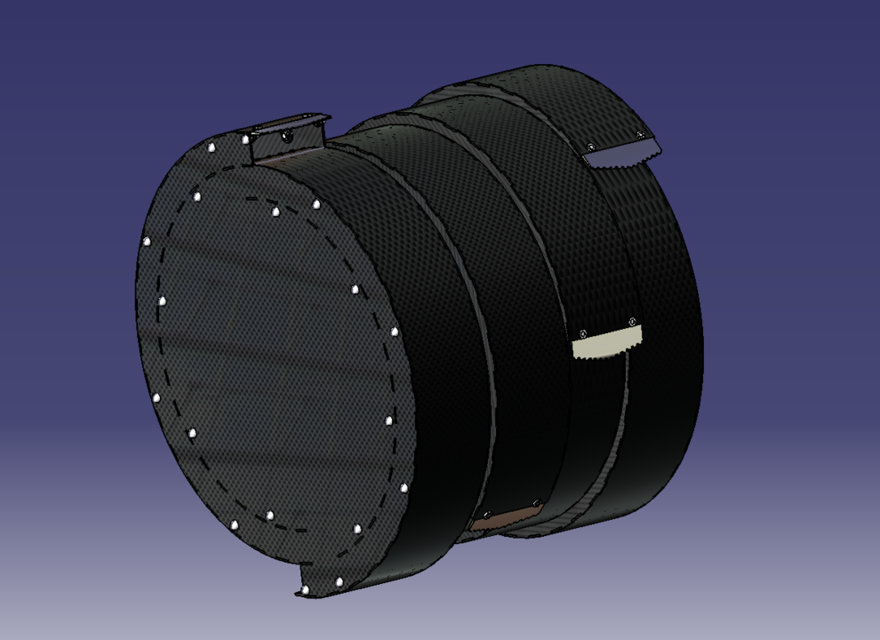
RASSOR_Challenge_Mikel_Iturbe
grabcad
HOW THE DESIGN WORKS AND INTENDED FILL RATIO a) How the design works The present RASSOR design features four drums with two scoops each. Each drum is offset by 45 degrees from its neighbors, ensuring that only one or two scoops are engaging regolith at any given time to maintain low reaction forces. The design was developed by NASA to optimize performance. Each drum boasts two channels for loading and unloading regolith. These channels exceed 180 degrees and have a constant distance between walls to prevent clogging. As the lower scoop captures regolith, it is lifted up while the upper scoop remains unloaded, preventing material from falling out. The design relies on two channels per drum and no inner connections between drums when holding material inside to facilitate loading. To combat clogging issues, structured roughness surfaces have been incorporated into the channel walls. This passive solution has been shown to effectively reduce shear stress and prevent particle buildup. b) Intended fill ratio Each drum measures 0.134 square meters in area, with scoop/channel widths of 85.5 millimeters. Calculating the total volume per drum yields 11.547 liters. The intended fill volume is approximately 8.273 liters per drum, resulting in a fill ratio of 71.6% when compared to the available space. With four drums, the total intended capture volume would be 33.092 liters. This design is feasible and can be created using readily available materials. IS THE DESIGN REAL? CAN THE DESIGN WORK? CAN IT ACTUALLY BE CREATED? The RASSOR design utilizes aluminum sheet metal for scoops with a density of 2640 kilograms per cubic meter. Bolts and nuts are constructed from carbon fiber with a density of 1500 kilograms per cubic meter, while the main structures and taps are built using polymer matrix composites with densities ranging from 1100 to 1700 kilograms per cubic meter. For this design, a composite density of 1200 kilograms per cubic meter has been selected. The total mass of the bucket drum is 4.838 kilograms. DIMENSION REQUIREMENTSSee attached blueprint for detailed specifications SIMULATION A simulation was conducted using EDEM discrete element method software to examine the loading and unloading process. Eleven seconds of simulated time were captured, with the design operating in loading mode from second five to ten and unloading mode thereafter. REFERENCES [1] Martinez et al., "The Influence of Surface Roughness Form on the Strength of Sand–Structure Interfaces," March 2017. [2] Sorell et al., "Clogging in Parallelized Tapered Microfluidic Channels," June 2016. [3] Buryachenko, "Micromechanics of Heterogeneous Materials," Springer Publishing Company, 2007.
With this file you will be able to print RASSOR_Challenge_Mikel_Iturbe with your 3D printer. Click on the button and save the file on your computer to work, edit or customize your design. You can also find more 3D designs for printers on RASSOR_Challenge_Mikel_Iturbe.