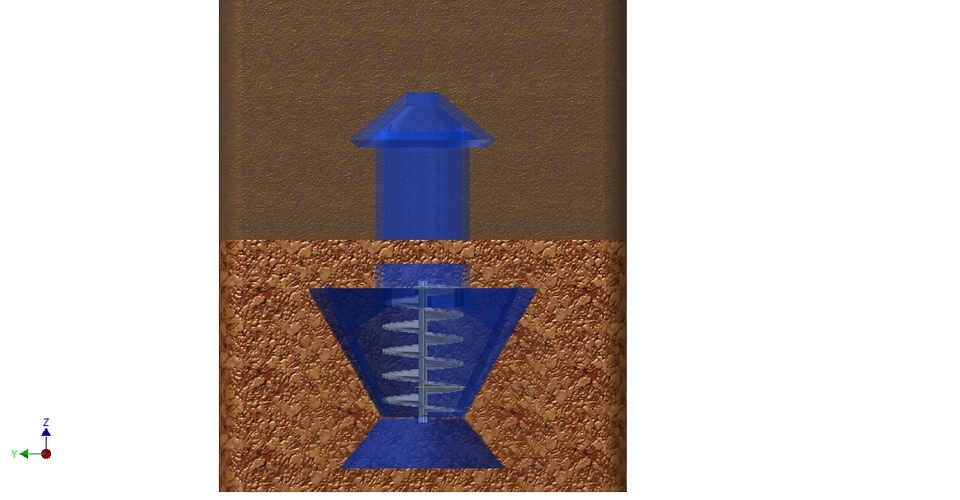
Pyrolysis mini stove in refractory ceramics with water heater, coocking place and heat storage
grabcad
A pyrolysis process means you will not burn the wood, but take it into a high enough temperature that forces it release the gasses contained within, and you burn those gasses in a separate burning chamber (not necessarily another room, the separation can be a thin empty space like in our case where oxygen is not available for the gas to start burning) To accomplish this you need a pipe in iron or ceramic wide as a 1 gallon milk boiling pot, and twice tall that you make crenelates to it on the top, than you cover it with a conic lid that had a large hole in the center top of it, so oxygen passes through the crenelates and mixes with gas coming from the wood in the pot, climbs up in the hole and burns with flame but no ashes. Fill the pipe to the top (nearly) put some fire ignition substance on it to light it on (I said fire ignition not petrol, that is fire explosion... rather use cooking oil or so) and wait until the heat acts on the wood beneath and starts gasseification, from that moment on there is no more smoke and ashes, just pure hot flame. That gives you 4 times more heat with the same amount of chopped wood, or 4 times more fire time, your choice. 1 build a pipe 100 mm or more inside diameter out of 3 mm thick iron or 10 mm thick ceramic (clay plus sand, go online to learn the correct proportion for refractory ceramics homemade) 200 mm tall with a bottom and another piece of pipe beneath the bottom, cut a fuel chops entry in the bottom, crenelate the top accordingly. 2 Build the cone to fit 10mm thick if ceramics, iron 3 mm should do. 3 build the base in 2 mm thick iron or 10 mm thick ceramics as in the drawings 4 buy the Archimedes screw plus motor somewhere to fit your diameters and pushing needs (chops size dictates them, the one you get with a branches shredder) 5 according to the drawings build the base, the fireplace and the water boiler space and the stove top and the heat storage unit, like doing pottery somehow, just bigger dimensions, more patience, and use plywood walls jigs to help you get a proper job done. 6 Ask a good welder to weld you the water boiler in no rust steel, with threaded fittings exit curves already welded on in position, not a job for any John and Jane Doe 7 When done and all is dry burn the ceramics either the classic manner to bake it to refractary, or pay somebody that has a ceramic burning oven to do it for you. 8 Than take it home and mount it 9 Chop the branches, cereals left overs, dry food, anything that is natural and burns (no plastic or rubber please) and feed your stove to stay warm and nice in the winter. Refractory ceramics is heavy stuff, ask friends for help, use car shop cranes to lift, don’t let it fall on your foot. bad made pyrolysis burners might allow return of flame with oxygen into the burner with a strong wind raffic pushing air down the chimney thus creating conditions for an explosion that might deteriorate your burner or the entire stove, make sure you put a wind self orientation protection on top of your chimney on the house. Bad mixed clay and sand might result in cracks while drying, or later on while operating the stove, make sure you mix the right proportions and pretty much perfectly homogeneous. Too big wood chops might result in the screw blocking, and too fine or wet materials (wood dust, wet kitchen garbage) might clog the screw, pay attention.
With this file you will be able to print Pyrolysis mini stove in refractory ceramics with water heater, coocking place and heat storage with your 3D printer. Click on the button and save the file on your computer to work, edit or customize your design. You can also find more 3D designs for printers on Pyrolysis mini stove in refractory ceramics with water heater, coocking place and heat storage.