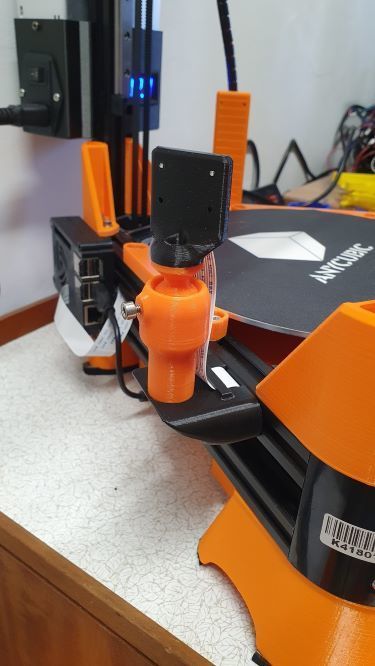
Pi Cam Ball joint mount for Kossel or 2020 frame printer
cults3d
Despite hundreds of Pi-Cam mounting models on Thingiverse, I struggled to find one that worked with my Kossel Linear Plus and the fisheye lens Pi-Cam. So here's my offering to the table, yet another Pi-Cam mount. I'd been experimenting with "Print in Place" designs and fancied a go at a ball and socket joint so designing a joint with a purpose made it a bit worthwhile. There has been a lot of headscratching, swearing and frustration before I eventually got this to work reliably but I've printed three of these out now on different printers and all worked OK so the tolerances should be good for most folk out there with half decent calibration. I have incorporated a ribbon cable management system which keeps the thing out of the path of the effector, should it decides to venture close to the edge of the bed. (I made a schoolboy error once designing a layer calibration model out to the max printable area. Unfortunately I forgot about the skirt which took it a further 5mm out and it collided with my old mount and tore out the ribbon cable. It all got emotional at that point) The design is in 3 or 4 pieces, dependent on whether you use the optional spacer and apart from a standard Pi-Cam, you will need the following fasteners to complete: 4 x M2 x 4 or 6mm Cap Head screws (Pi Cam Mounting) 1 x M3 x 12-20mm Cap head screw (Cam mount to Ball joint) 1 x M4 x 16-20mm Cap Head Screw (Ball joint pillar to Frame mount) 1 x M4 x 8mm (Ball set screw) 2 x M4 x 10mm Cap head screw (Frame mount to 2020 Frame) 2 x M4 T-Nut (Frame mount to 2020 Frame) (Optional) 2 x M4 x 30mm Cap Head Screw if using the spacer block Please note further info in Print settings as these are important. Update: 03 Sept 20. After Thingiverse finally resurrected, I've uploaded a screwless camera mount option, where tha camera module slips into a set of slots rather than being fixed with the M2 screws. Update. 01.01.2021. I've added a base for attaching the cam mount to an Anycubic Predator. Post-Printing Assembly Instructions The assembly is pretty self explanatory but a couple of tips for you from my experience. Use the M2, M3 and M4 screws as applicable to run down the threaded holes in the camera mounting piece, the ball flange, socket set screw and socket pillar to clean up threads before assembly. I recommend screwing the camera bracket mounting screw into the ball flange threaded hole (M3 x 12mm or M3 x 20mm) before applying firm thumb pressure on the side of the ball flange to break the ball free inside the socket. It should "Crack" away cleanly and a bit of exercising the ball around in the socket should have it spinning freely. Fit the M4 x 8 or 10mm screws through the frame mounting holes and fit the pair of T nuts ready for frame attachment. Assemble the ball pillar to the frame mount and secure with the M4 screw up through the base. The screw hole is threaded full length so a longer screw may be fitted if necessary. Ensure the set screw hole is facing the desired direction before fully tightening the screw. Fit the Pi-Cam to the camera mounting plate with the four M2 screws. Fit the camera mount and camera to the ball joint, securing with the M3 screw. Again, screw length up to 20mm can be used. Use a 17mm spanner on the flats of the ball flange if difficulty is experienced tightening the screw. Route the ribbon cable through the retainer bridge and up to the camera, ensuring the blue reinforcing piece of the ribbon cable termination is facing out. Ensure the ribbon cable is located in it's recess and trap between the frame and mounting face before fixing using the two screws and T nuts.
With this file you will be able to print Pi Cam Ball joint mount for Kossel or 2020 frame printer with your 3D printer. Click on the button and save the file on your computer to work, edit or customize your design. You can also find more 3D designs for printers on Pi Cam Ball joint mount for Kossel or 2020 frame printer.