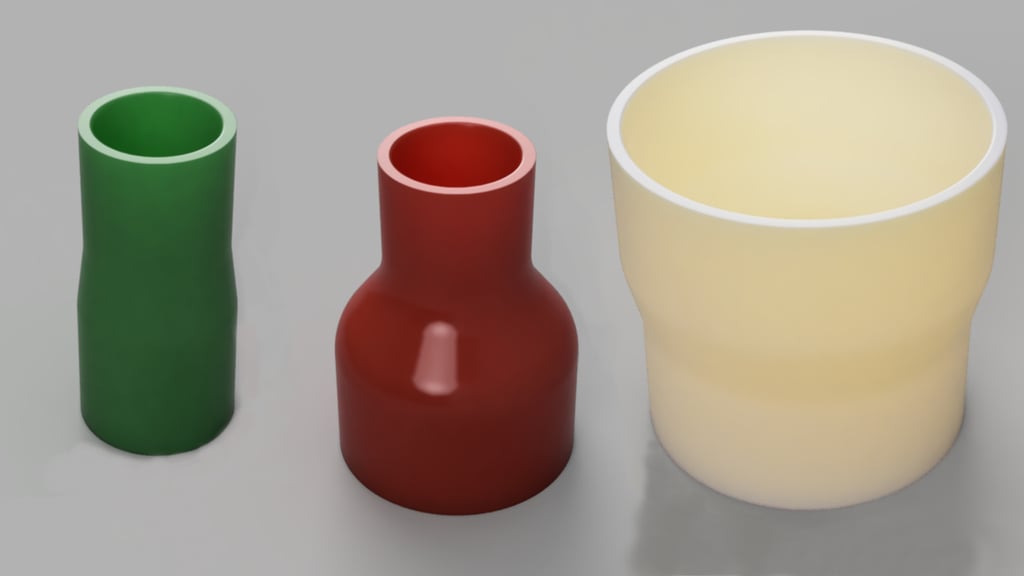
Parametric Circular Dust Port Adaptor
thingiverse
Do you need to connect two circular ports/pipes together in a workshop? (usually for dust collection)Do you use a CAD program capable of opening f3d (Fusion) files?Are you a new or relatively lazy/efficient Fusion360 user? (Or could be convinced to sign up for a free account?)Have you ever resorted to tape in connecting two differing sized pipes together in your dust extraction system?Do you want to create custom dust port (or just plain old pipe/conduit) adaptor for ANY (and I do mean, ANY) sized CIRCULAR ports/pipes you may have?Yeah, me too. That's why I made this. :-)Now, if you need one that actually, BENDS (don't worry, even the bend angle is a parameter too), then have a look at my more evolved versions here:https://www.thingiverse.com/thing:6455859and for more gently bending variety...https://www.thingiverse.com/thing:6491622But this one is good too for straight applications, and has fewer parameters that can possibly be used to break the model. (Yep, I've done that too, don't worry).WHY USE THIS MODEL?Streamline any major transition with your dust extraction:I've designed quite a few adaptors to attach circular tool dust ports (of several sizes) to certain, differently-sized circular shop vac handles, and hose ends. This is great if you just want to download a file and print without any tweaks. However, it seems there's always a slightly different sized port on a new tool, (or I may have to change everything when I get a new dust extractor/shop vac) so I just want to measure it, plug that measurement in, decide what I'm connecting it to, and plug that measurement in. Then all I need to do is export and slice that file to get it printed. I don't want to HAVE to create a new model every time..Designed to connect on the OUTSIDE of any pipe/port you connect for maximum airflow. If that doesn't suit your needs, you can easily factor in the wall thickness of either/both ends to taper it for the inside diameter if you wish, just remember that you can enter formulas into dimensions using the parameter names too in Fusion, so you won't need a calculator :~). If you do so, you'll need to REVERSE the taper so that the socket is narrower than the diameter further in. Speaking of taper... using the model "as is" for the outer diameters....Tapered sockets so you insert both the port, and whatever pipework INTO the ends of this adaptor, and get a nice friction fit and decent seal. Near complete customisation!Connecting something to a long shop vac handle and want a gentler taper? Or, just a longer or shorter adaptor to get between two points? Tweak the wide end of the socket, the narrow end, and adjust the distance between! If you prefer to connect something to a hose attachment (notoriously shorter tapers needed for a good fit) then again, tweak the wide and narrow end of the socket, then choose a suitable shorter distance in between!Used to sanding hard edges to make connections easier? Well I've added fillets on both the internal/external edges of both ends of the adaptor.Want the best possible airflow and/or smoother exterior?I've included even more fillets for every edge to minimise drag on the airflow inside, as well as the outside to ensure adequate material thickness throughout without any "cut corners".WHY WOULDN'T YOU USE THIS MODEL?Without a CAD app capable of handling F3D files, you won't get much out of this.You need to customize the model to your needs. It won't work in a simple download > slice > print. It's more download > TWEAK > slice > print. So if you're not confident with Fusion360, you'll need to read my step-by-step instructions below. It's limited to circular pipes and ports. While most ports are circular, and this will be widely compatible with many tools.... There's a TON of tools with oddly shaped dust ports on them (My DeWalt electric planer for example... it's amongst my other designs). Also, there are no wacky notches and recesses found on this adaptor either... so Festool sander users won't like this much, either. HOW DO I USE THE F3D FILE?Open the f3d file in Fusion360. While in "Design mode" Hit the FX button > user parameters... if you're not using full-screen/maximised window (or just have a low-res screen) then the FX button may well be hidden from view. In that case:Click: solid > modify > parameters > user parameters...and adjust/enter the values as needed. The parameter names are explained in my uploaded image. Simply enter your (carefully measured and noted) measurements for the EXTERIOR of your respective dust port/pipe. Adjust the diameters of all four points on the adaptor, and adjust the size of any fillets to taste. Then I just right click on the body name (in the browser section on the left side of the screen) then select export mesh > save that as an STL/3MF/whatever, and slice it up accordingly using your slicer software of choice. Please note: If you're a user of the original AnkerMake slicer instead of the beta AnkerMake Studio which is Prusa Slicer based, then please note you should export as STL because the AnkerMake slicer app doesn't handle 3MF files. PrusaSlicer and Cura based slicer users should be fine with 3MF files. IF THERE ARE ANY QUESTIONS?The parameters should be self-explanatory, please see the included diagram...but to ensure your success, I'll add some suggestions here and there:For the wider end of both sockets, I usually like to add between 0.3mm and 0.5mm to whatever outside diameter the pipe/port has to ensure it can work around whatever I have. Remember, you can extend the distance between the narrow and wide sections of each taper to make it gentler, or merely set a smaller difference between the diameters. For the narrower end of both sockets, I usually like the end diameter to be between 0.2mm and 0.4mm SMALLER than my measurements, to ensure a good seal, and tight friction fit. It also can clamp down on any worn/narrower parts in the future.If you're adjusting the adaptor to go INSIDE a dust port (not recommended since it restricts airflow) then the "wider" end, will need to become the narrower one, and the "narrower" end will need to be the wider one. (reverse the taper direction so it gets wider further in, this will be confusing, given the parameter names, so keep notes for clarity's sake) Remember to deduct the wall thickness TWICE from BOTH the "wider" and the "narrower" measurements of each socket. Why?The four major circular dimensions are DIAMETER measurements for the HOLE inside the adaptor (walls are not included). Conversely, the wall thickness is merely radius, so this is why the wall thickness needs to deducted twice.
With this file you will be able to print Parametric Circular Dust Port Adaptor with your 3D printer. Click on the button and save the file on your computer to work, edit or customize your design. You can also find more 3D designs for printers on Parametric Circular Dust Port Adaptor.