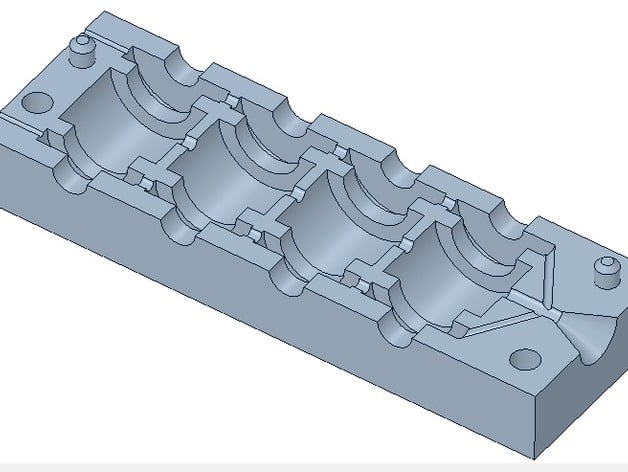
OmniMac Vibration Ball - Silicone Mold
thingiverse
This project is part of my ongoing research and development of advanced drone technologies. Check out my complete guide on Instructables, where you can find all relevant files and documentation: http://goo.gl/wD0f3K. The goal was to design a mold for making omnidirectional vibration dampers that could effectively isolate the flight controller of a quadcopter from its surroundings. I created this design based on detailed dimensions derived from a discontinued Thingiverse object. While I'm not sure what the original file looked like, it provided me with essential specifications that I adapted into my project. This particular mold features two identical halves, allowing users to simply print one part twice and assemble them together. There's a precision-engineered inlet for a syringe (a 3/4oz - 20ml BD brand syringe works well) at the tapered opening, and intricate channels connect all four isolators to this single entry point. Microscopic holes at the end of each mold allow air to escape during silicone injection. I observed that standard commercial vibration dampers lack a critical hole for mounting M3 hardware. My design addresses this issue by incorporating small knitting needles (3-ish millimeters in diameter) as a mounting aid between the two mold halves, providing secure fixation and aligning perfectly with the existing through holes on original isolators. For creating these precise parts, I chose to use SmoothOn DragonSkin 10, a flexible silicone material that resembles jelly and performs impressively well for vibration isolation. Initially, its thickness posed some difficulties in drawing into the syringe, but fortunately, this property led to an accidental bonus – air bubbles were effectively eliminated during injection, creating an unexpectedly favorable outcome. The next step was assembly of the two mold halves around these carefully selected needles, followed by clamping them securely with a Irwin QuickGrip clamp supported by a cardboard box. Mixing the silicone parts using a graduated shot glass removed air pockets and facilitated accurate dosing. Then I manually drew the mixed material into the syringe to remove excess air. The molding process continued until the mixture was filled up to just above the inlet, and as expected, silicone began to seep out of the bottom holes. A careful waiting period followed overnight demolding in the morning with moderate force, utilizing knitting needles to pry open the mold without damaging it. Overall, I found this approach highly successful. Eight attempts yielded five usable isolators devoid of air pockets, marking a triumphant end to this intricate design process.
With this file you will be able to print OmniMac Vibration Ball - Silicone Mold with your 3D printer. Click on the button and save the file on your computer to work, edit or customize your design. You can also find more 3D designs for printers on OmniMac Vibration Ball - Silicone Mold.