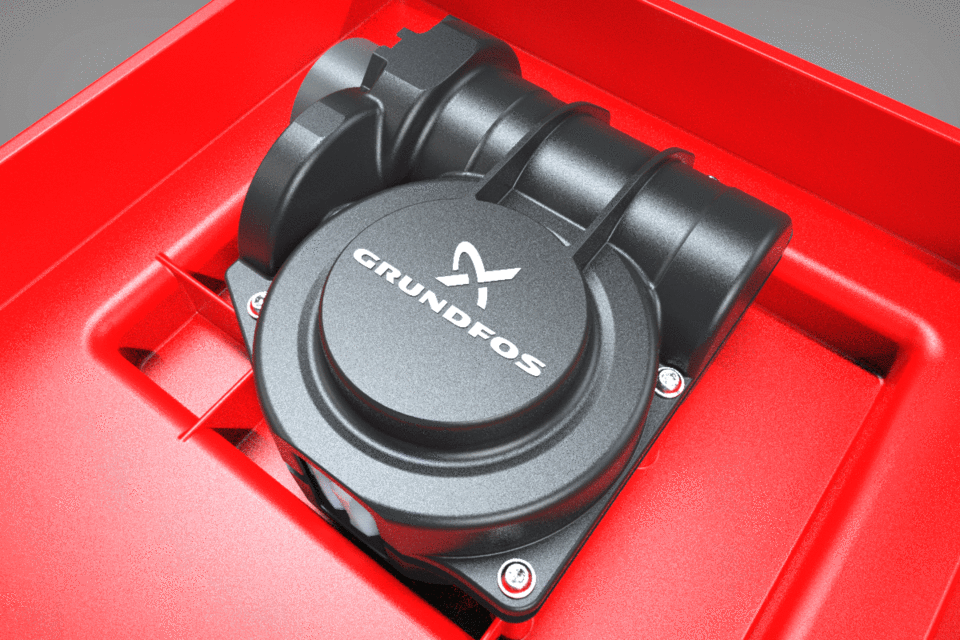
Nylon Worm/Spur
grabcad
Please read the report for full explanations. For this study, I deliberately avoided reinventing the wheel by relying on standard gears due to their well-known, proven, and predictable nature. The most significant constraint was that it had to operate without lubrication, so I opted for high-performance thermoplastic nylon-based gears (Mitsubishi MC602ST/DuPont Zytel/DuPont Delrin). This material boasts a low and predictable friction coefficient, as well as auto-lubrication properties that enable non-lubricated operation. Moreover, it allows for weight reduction and the use of injected-molded gears, significantly decreasing production costs for high-volume products. However, nylon-based gears will be weaker than steel gears, necessitating oversized components to meet system constraints. The challenge lies in designing the system within the given design parameters. Given the valve system application, I concluded that the system must be non-reversible to prevent spontaneous rotation of the output shaft. Consequently, the system will be based on a worm/gear followed by a minimum of spur gear train to achieve the desired reduction ratio. The use of nylon for worm/gears is feasible due to intermittent usage and low device speeds.
With this file you will be able to print Nylon Worm/Spur with your 3D printer. Click on the button and save the file on your computer to work, edit or customize your design. You can also find more 3D designs for printers on Nylon Worm/Spur.