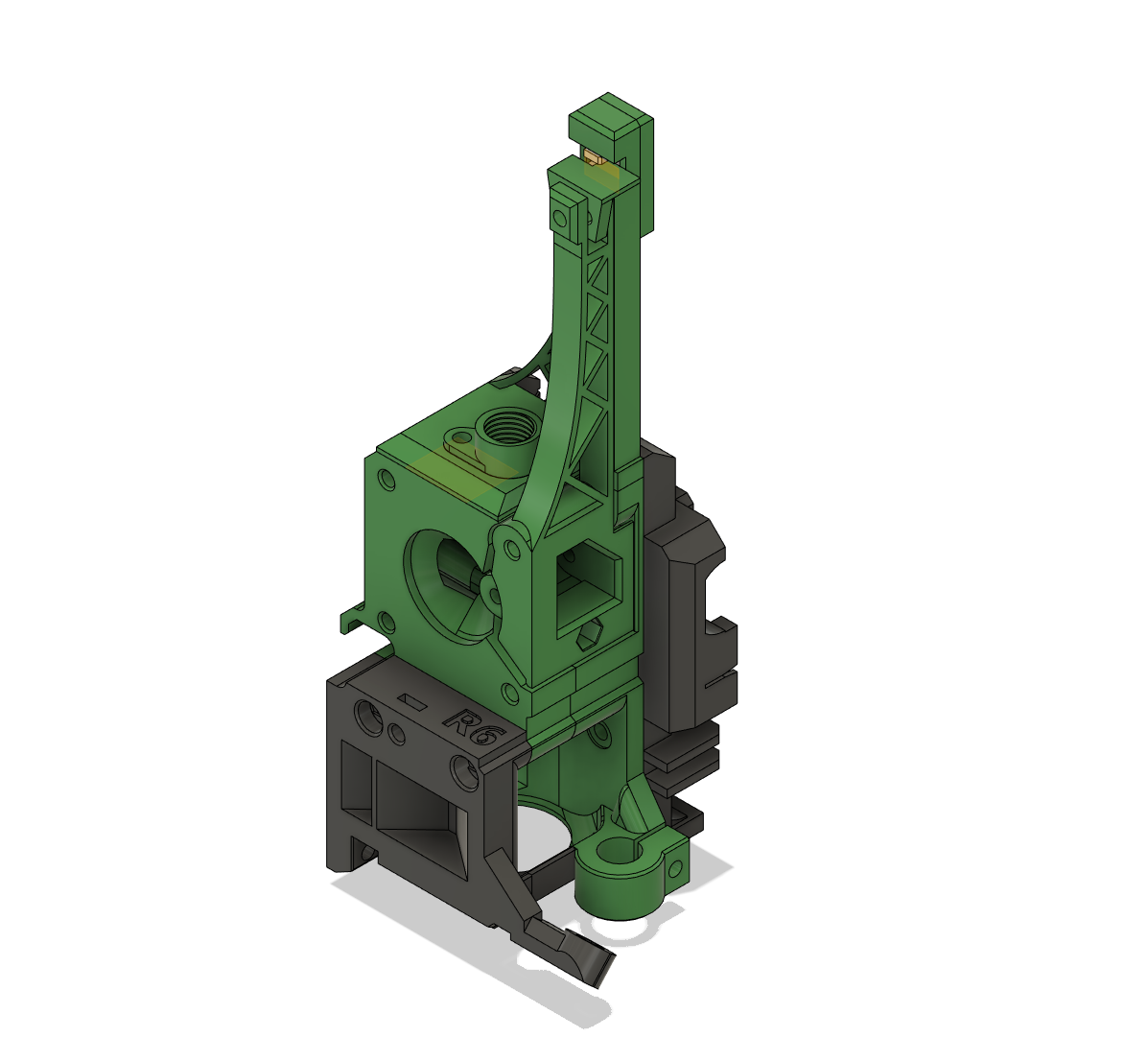
No MMU Babysitting! (NoMBa)
prusaprinters
<h3>TL;DR</h3><h4>Goal</h4><p>Achieve impeccable MMU2s reliability: printing of 5 color <a href="https://www.printables.com/model/281932-mmu-torture-test-mmutt-1000-tool-changes">MMUTT </a>(1000 tool changes) without a single user intervention. </p><h4>Hardware modifications</h4><ul><li>Extruder<ul><li>wider filament path inside the extruder above and below the bondtech gears </li><li>passthrough PC4-M10 push fitting for the extruder with filament traveling inside PTFE tube up close to the bondtech gears</li><li>bigger servicing hole in the idler door, new servicing hole from the other side</li><li>redesign of the filament sensor allowing for much more reliable filament detection </li><li>removal of the whole unnecessary non-MMU filament sensor mechanic (magnetic lever) </li></ul></li><li>MMU2s<ul><li>wider filament path through the selector and associated parts</li><li>passthrough PC4-M10 push fitting for the selector with PTFE tube starting inside the selector</li><li>improved FINDA detection with magnet inside the selector</li></ul></li><li>PTFE tubing<ul><li>use of wider, 2mm inner diameter PTFE tubes for the 5 short tubes in the MMU2s before the selector and between the selector and the extruder. Attention: standard 1.85 mm inner diameter tube inside hotend!</li></ul></li></ul><h4>Slicer setting modification</h4><ul><li>Printer Settings → Single extruder MM setup → Extra loading distance: -19 (instead of -25)</li></ul><h3> </h3><h3>The long story</h3><h4>Introduction</h4><p>I was very close to throwing the whole MMU2s out of the window. Sometimes it worked a while, then it stuck again every handful of filament changes. The filament got jammed in every possible location: deep in the extruder, in the extruder PTFE festo, inside the selector and inside the short PTFE tubes right before the selector. The following modifications are based on the R6 version of the original Prusa MMU2s parts. I narrowed the problem down to the three MMU devils. </p><h4>Devil 1 - to narrow filament path</h4><p>Tips just slightly below perfect tend to get jammed in the various narrow passages between MMU parking position and the hotend. I therefore increased the diameter of the filament path inside all the printed parts starting from the selector down to the hotend. All PTFE tubes (5 short tubes before the selector and the connection between selector and extruder) were exchanged in favor for a bigger, 2mm inner diameter. Furthermore, I ditched the standard push fittings in favor for passthrough PC4-M10 push fittings. This allows for PTFE tubing to reach both a little bit inside the selector and deep into the extruder right above the bondtech gears, hence prolonging the low friction moving distance inside the tubing. </p><p>Side note: In my overzealousness I initially changed the short tube inside the hotend too. However, this proved to be disastrous with awful filament tips. I realized that the smaller inner diameter of this tube helps to shape an nice thin tip after retraction from the melting zone. The proper inner diameter seems to be 1.85 mm as discussed <a href="https://forum.prusa3d.com/forum/original-prusa-i3-mmu2s-mmu2-general-discussion-announcements-and-releases/clarifications-about-ptfe-tubes-on-mk3s-with-mmu2/">here</a>. </p><p>Side note 2: I used 2 mm inner diameter tubing between the spools and the MMU as well and <a href="https://www.thingiverse.com/thing:3233579">this mod</a> from Thingiverse. Reducing friction seems to be a good idea. However, this led to some loading errors because the filament slipped backward out of reach of the MMU. I designed a part which can be clipped to the tubes. The clip forces a slight curvature to the tubing. This reintroduces some friction but without the difficult to control compression of the tubes. </p><h4>Devil 2 - erratic sensors</h4><p>If the filament was not jammed somewhere, then the unreliable sensors were the second most frequent problem leading to miserable experiences with the MMU2s. Especially the filament sensor proved to be rather finnicky. Based on an approach found on thingiverse (see credits) I redesigned the filament sensor with a solution allowing for a much more fine grained calibration. By increasing the length of the triggering lever, relocation of the sensor and improving the calibration method (no more moving around of the whole tower) I was able to finally get reliable results. While I was at it I also removed the whole magnet-lever-filament-sensor-mechanism not required by the MK3s+MMU2s. This allowed for an additional servicing hole from the left extruder side.</p><p>The FINDA on the other hands was prone to false reads because of the steel ball not moving freely due to filament strings stuck in the selector. This was improved by inserting a magnet into the selector pulling the steel ball away from the FINDA (see credits again).</p><h4>Devil 3 - an undervalued slicer setting</h4><p>The above mentioned modifications immensely reduced the printing errors. All the “MMU needs user attention” errors were cleared. However, every 100-200 tool changes the extruder made a grinding sound during load. The filament seemed to partly reach the bondtech gears but was never properly caught by them and was subsequently unloaded back to the MMU. This paused the print without an error message from the MMU. This drove me nuts as I couldn't really debug the problem due to its scarcity and all the sensor seemed to be working fine. A long read in the forums showed that quite a few people documented this issue. The hint for the solution was finally provided in a video in this <a href="https://forum.prusa3d.com/forum/original-prusa-i3-mmu2s-mmu2-hardware-firmware-and-software-help/load-unload-issues-some-tips-that-helped-me/">thread</a>. The “Extra loading distance” setting in the slicer defaults to -25. This means that upon reinsertion the distance of the filament pushed inside the extruder is 25 mm shorter than the distance when it was pulled out. The video suggests to set this to 0 mm to ensure proper loading. However, my test showed that this leads to small blobs on the wipe tower during load as the still molten prior filament in the hotend is pressed out. Those blobs never blocked the printhead but I was concerned that this might lead to problems down the road. A setting of -19 mm finally prevented those blobs but ensured that the filament was caught by the bondtech gears every single time.</p><h3>Printing and assembly</h3><p>All part but the NoMBa-sensor-tower can be printed without supports. I recommend the standard prusa settings (PETG, 0.2 mm layer height QUALITY preset, 40% infill). NoMBa-sensor-tower requires some supports to print nicely. If you don't know how to place support enforcers have a look or directly slice and print “NoMBa-WHOLE.3mf”.</p><p>Assembly is of moderate difficulty. Most of the steps are analog to <a href="https://help.prusa3d.com/guide/3a-mk3-extruder-upgrade_182789">this original prusa instructions detailing the extruder upgrade from mk3 to mk3s+</a> and <a href="https://help.prusa3d.com/guide/5-pulley-body-assembly_43152">assembly of the MMU2s</a>. I recommend placing the extruder ca. 1 cm above the printbed (remove the steel sheet) in the middle of the X axis. As the X carriage is not changed there is no need to remove it and its bearings. Also the wrapped cables can be left untouched as long as the filament sensor cable is long enough. During disassembly the E3d hotend and its cables can be gently placed on the printbed. </p><p>Assembly of the modified parts is guided by the pictures provided. Pay special attention to:</p><ul><li>The cable of the filament sensor should be placed as illustrated in the picture. This might require opening up the cable assembly in order to give it some more slack to reach the sensor.</li><li>The lid of the filament sensor is fastened using the same small screw as in the standard design. Inserting the screw into the appropriate hole of the sensor tower before assembly can help (dilating the hole somewhat).</li><li>Selector: insert one of the magnets provided with the MMU kit (aprox. size 10x6x2 mm) in the slot designed for it. The steel ball inside the FINDA should stick to it.</li></ul><h3>Credits and CAD models</h3><ul><li>Fusion 360 base files for the MK3s-MMU2s came from <a href="https://grabcad.com/denis.vasilescu-1">Denis Vasilescu</a><a href="https://grabcad.com/library/prusa-mk3s-mmu2s-in-fusion360-format-1"> </a>on grabcad and from the official prusa parts repository.</li><li>This is not a remix of an existing modification, but full credit for the idea of the redesigned filament sensor and the magnet inside the selector goes to <a href="https://www.thingiverse.com/thing:3554066/makes">frimmel </a>on thingiverse.</li></ul>
With this file you will be able to print No MMU Babysitting! (NoMBa) with your 3D printer. Click on the button and save the file on your computer to work, edit or customize your design. You can also find more 3D designs for printers on No MMU Babysitting! (NoMBa).