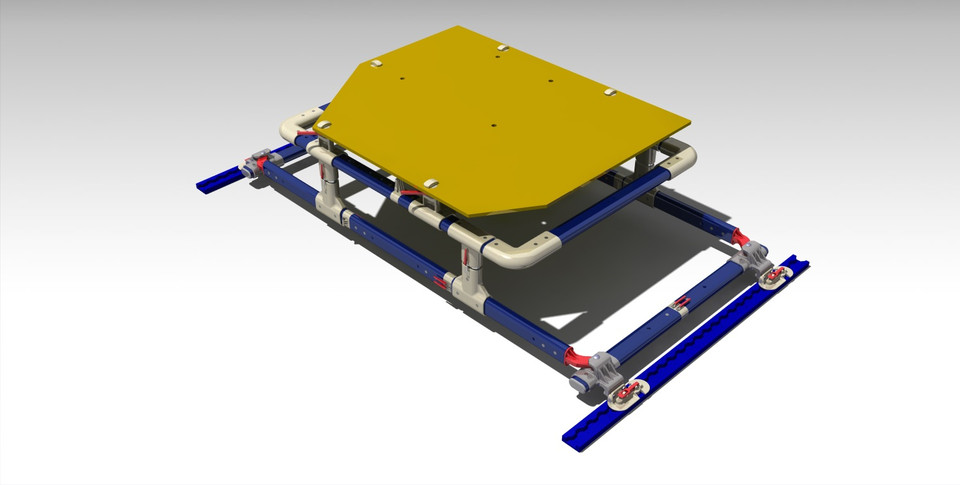
NASA EAS - Final Update
grabcad
NASA Experiment Attachment System (EAS) Challenge The EAS design focuses on simplicity and efficiency. The goal was to create a system with only two sub-assemblies, easy to use in orbit. It aligns with NASA's Logistics Reduction main objective. To achieve this, sheet metal was avoided due to its propensity for local buckling and the need for rework after laser cutting. Complex metal forms were also minimized to encourage reusability. The design incorporates handrails from a previous NASA challenge, enabling future use and reducing waste. The ABS joins allow customization and parts can be produced within the ISS, reducing launch weight. The wide surface interface with the seat track reduces moments and converts them into force, with a self-locking system to reduce tool usage. The design allows for material changes in handrails if necessary, ensuring secondary stress effects are controlled. Frictionless contact was used in FEA simulations, replicating real-world conditions while managing processing time. Memory limitations prevented mesh convergence analysis. The submission meets criteria for description, STEP/IGES, assembly procedure, sharp human edge, factor of safety, deflection, force and moment reactions, EAS envelope, launch envelope, mass, materials, captive fasteners, and retaining pins.
With this file you will be able to print NASA EAS - Final Update with your 3D printer. Click on the button and save the file on your computer to work, edit or customize your design. You can also find more 3D designs for printers on NASA EAS - Final Update.