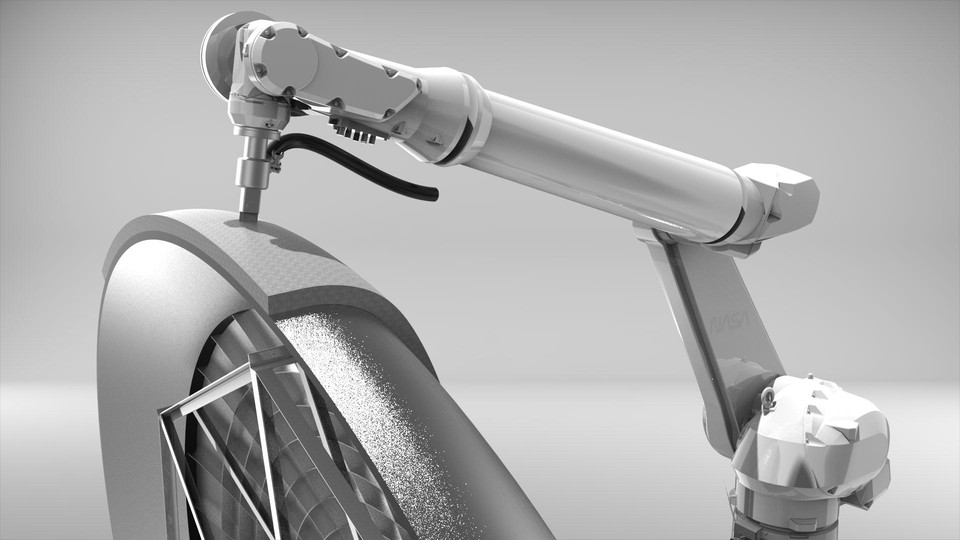
NASA Challenge: Human Rated Spacecraft 3D Printing Process
grabcad
In Angel Alvarez's suggested video (https://www.youtube.com/watch?v=XgPJdpGV8mE), I assessed the ablative material's deposition fluidity using a 3D printing technique. The material deposits optimally on flat surfaces but may slip on curved ones, like the toroidal heat shield zone. To address this, I proposed a gantry to support the heat shield with an inclination of about 90 degrees for favorable gravity-assisted deposition. The platform enables 360-degree rotation and a 90-degree tilt, with self-braking motors operated via inverters and double-stage worm gear reducers (1:10000 ratio). A six-axis robot coordinates the extruder movements, and the stand sits on an air bearing translation platform. The rotating table offers lower geometric resolution than the robot, so during additive vessel wall printing, it'll bring a circular sector into the robot's action area. Precise control software must determine the best combination of table rotation, inclination, and robot arm movements for optimal deposition accuracy.
With this file you will be able to print NASA Challenge: Human Rated Spacecraft 3D Printing Process with your 3D printer. Click on the button and save the file on your computer to work, edit or customize your design. You can also find more 3D designs for printers on NASA Challenge: Human Rated Spacecraft 3D Printing Process.