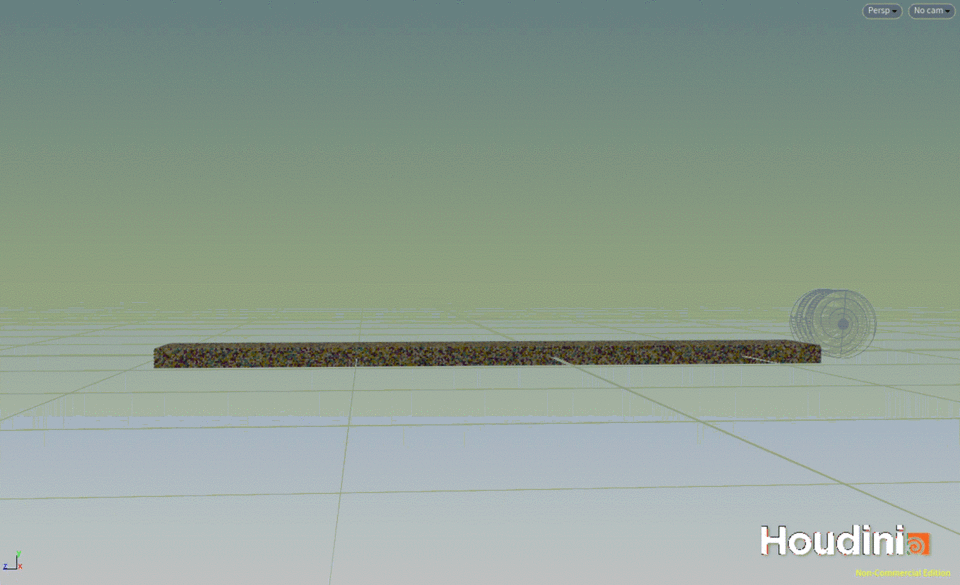
---> NASA CHALLENGE 2020 <--- NASA RASSOR DRUM - 2 spirals
grabcad
This is my second entry for the NASA RASSOR Challenge. The 2-scoops design with a spiral structure of the drum's internal space boasts an intended fill ratio over 70% (over 35 liters). The spiral layout enables two key functions: directing collected regolith deep into the drum, reducing resistance to collecting new portions at entry points and unloading regolith evenly during reverse rotation at unloading sites, thereby minimizing regolith jam and sticking. In the 2-scoops design, the scoops are intentionally shifted more towards one side of the drum. Looking along the axis, we see that the scoops are unevenly distributed around a circular section, positioned at approximately 7, 9, 11, and 13 o'clock. The excavation cycle concludes with the scoops in the upper left position, resulting in less regolith loss when the bucket is moving. This design has both advantages and disadvantages compared to traditional 3-scoops designs. A disadvantage is that excavation is done less evenly and may take longer due to asymmetry. However, an advantage is that during transportation, less regolith will be lost due to spillage. Due to the complexity of modeling and testing, we cannot make exact estimations or comparisons of these advantages and disadvantages. It's clear that 3-scoops designs are more likely to win if excavation sites are near processing facilities. Conversely, as the distance between excavation and processing sites increases, the advantage of 2-scoops designs over 3-scoops designs becomes greater. In this model, two scoops have an angle of 55° between them to meet the maximum 175 mm scoop width requirement at any given time. However, if this limit can be reduced, the effect on lesser scattering during transportation may become even more pronounced. The drum material is primarily carbon fiber due to weight constraints (calculation link: https://docs.google.com/spreadsheets/d/1ee9JULr8QjGDX7upZeuKtGVvxd2IF4I9Nd5RXKK6HgI/edit?usp=sharing), with antifriction alloys used for scoops. The 3D model was created in Blender v. 2.79b + 2.81, and the simulation of regolith grain excavation was conducted in Houdini v.18. The maximum total width of engaged scoops at any given time is less than 175 mm.
With this file you will be able to print ---> NASA CHALLENGE 2020 <--- NASA RASSOR DRUM - 2 spirals with your 3D printer. Click on the button and save the file on your computer to work, edit or customize your design. You can also find more 3D designs for printers on ---> NASA CHALLENGE 2020 <--- NASA RASSOR DRUM - 2 spirals.