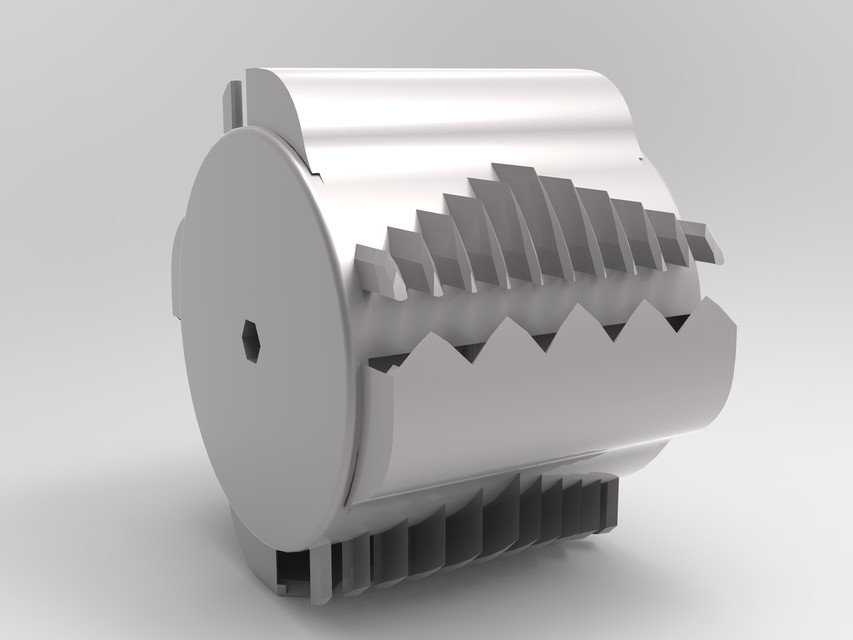
NASA Bucket Design Challenge V4
grabcad
A very simple scooping drum that effortlessly collects moon regolith, manufactured using readily available materials. As it rotates, the drum skillfully gathers regolith. The regolith is sifted by the rake in front of each scoop to guarantee large clumps and small rocks are not collected, which could clog the scoops.The forward motion of the mining cart ensures the scoop will be completely filled. Then as the drum rotates, the regolith is transferred to the internal swirl, which channels the regolith to the center during mining operations. When the drum is full (approximately 15.4 liters) and in position to discharge the regolith, the drum is reversed. The internal swirl transfers the regolith back out the scoops into the processing inlet.The drum is designed for 3D metal laser sintering printing (with an infill of 85% or higher, 95% recommended). The print should be made with powered metal that does not require supports. If supports are needed, they should be water-soluble so they can be easily removed with tap water, or some mild acid like acetone. I suggest it be printed from one end disk to the other disk. Once the print is complete and cleaned up, all that remains is to tap the two driveshaft attachment holes with an M12 tap, and attach the drive shaft(s). The metal used should be extremely resistant to the abrasive nature of moon regolith and lightweight. Since I do not know what this metal is, I cannot calculate its weight. I do not think carbon fiber is durable enough to withstand the abrasiveness of regolith, meaning a carbon fiber drum will not last unless it is coated with some protective coating, possibly electroplating it with titanium.The ends of the drum are 10mm thick, allowing it to be balanced by removing material. I recommend balancing the drum at least 40 RPMs. This ensures the drum will run smoothly at 20 RPM (as called out in the specifications). Balancing reduces wear and tear on the bearings, extending their lifespan. The 10mm thickness also acts as a flywheel (along with internal supports), storing kinetic energy that helps break up any clumps it encounters.I would like to make a recommendation. I suggest installing a flywheel between the drive motor and the gear box. This recommendation benefits in two ways. First, when the scoop encounters a hard clump, the stored kinetic energy in the flywheel helps it break through without bogging down or stalling the drum drive motor. Assuming the gear train reduces the motors RPMs to 20 RPM, the kinetic energy is converted into high torque, breaking up almost any clumps. Additionally, this means a smaller, less powerful drum motor can be used without reducing performance. The second benefit of the flywheel is its ability as a vibrator. By placing it off-center by a few mm or adding extra weight on the rim, these vibrations help loosen regolith, making scooping easier and more efficient. They also assist rakes in front of each scoop in breaking up clumps and sifting out small rocks.
With this file you will be able to print NASA Bucket Design Challenge V4 with your 3D printer. Click on the button and save the file on your computer to work, edit or customize your design. You can also find more 3D designs for printers on NASA Bucket Design Challenge V4.