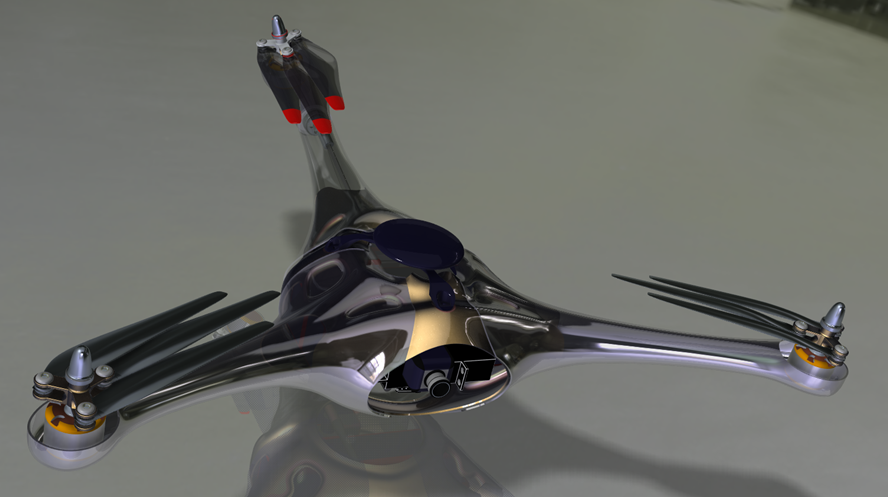
MuFly 6 Tricopter
grabcad
In my UMass Independent Study and capstone design project completed in December 2014, I showcased a 3D model of a custom-built tri-copter. The organically optimized carbon fiber body was created using a 3D printed mold. The design journey involved rethinking fundamental building blocks and finding geometric equilibrium, drawing inspiration from biology, technology, advanced materials like carbon fiber, and techniques such as 3D printing. Iterative FEA helped in stress flow distribution optimization. The tri-copter's body is composed of four parts: an inner shell (endo-shell) and three limbs inspired by biological joints with ligament and cartilage. The 'ball' acts as the pivot point, while cartilage is made of shock-absorbing foam (Poron), and the ligament is made of quick tie shoe laces. During impact, the arms disengage, absorbing immediate shock through compression and converting excess kinetic energy into heat via loosening bungee friction nuts (quick tie laces). This system isolates limbs from the heavier endo-shell, which contains a battery pack and makes up 70% of the total weight. Additionally, it shields the flight control board and camera from motor vibration. The 9443 carbon props from Hobby Power are used for the tri-copter's propellers, which auto-align due to centrifugal force and fold during impact. The dampening system simplifies maintenance, as all that's required is tightening the ties before flying again.
With this file you will be able to print MuFly 6 Tricopter with your 3D printer. Click on the button and save the file on your computer to work, edit or customize your design. You can also find more 3D designs for printers on MuFly 6 Tricopter .