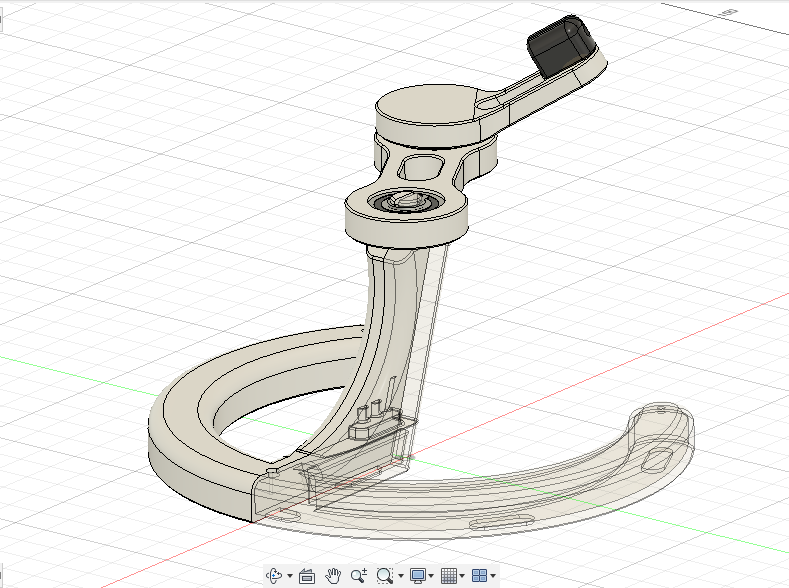
Mouse Bungee - EVO
prusaprinters
<p>To keep it simple, I modified the design to include features of commercial mouse bungees and other 3D printed mouse bungees; a <i><strong>stable heavy base</strong> <strong>(~250g)</strong></i>, <i><strong>cable held up and away (~100mm height)</strong></i> by <i><strong>non damaging</strong></i> <i><strong>rubber jaws</strong></i> & <i><strong>non-slip feet</strong></i>.</p><p>Since the base is hollow, <strong>supports that only touch the baseplate have too be used</strong>, otherwise the supports won't be able to be removed & the weights and resin can't be placed inside the base.</p><p>If you would like modify or tinker with the model further, I also <strong>included a .step file</strong>.</p><h4><strong>MODIFICATIONS:</strong></h4><ul><li><i>Hollow 2-piece base to insert weights (2.5mm ball bearings encased in resin)</i></li><li><i>Angled Bone2 & increased overall base height to eliminate cable drag </i></li><li><i>Slots for rubber feet</i></li><li><i>Silicone cable holder (over-molded part)</i></li><li><i>Shortened Bone1 & widened base to increase stability</i></li><li><i>Pins that retain the bearings have grooves for M8 circlips</i></li><li><i>Adjusted tolerances/clearances to allow for easier assembly.</i></li></ul><h5><strong>MATERIALS:</strong></h5><ul><li><i>2-part Resin (I use epoxy resin) <strong>(around 15ml was used)</strong></i></li><li><i>Any form of weights (I use around <strong>3500 of 2.5mm ball bearings)</strong></i></li><li><i><strong>HP 9470m 9480m</strong> laptop rubber pads <strong>(6 used)</strong></i></li><li><i><strong>608ZZ</strong> or <strong>608-2RS </strong>bearings <strong>(2 used)</strong></i></li><li><i>The 3D printed parts (Printed in PLA)</i></li></ul><h5><strong> OPTIONAL MATERIALS:</strong></h5><ul><li><i>Silicone rubber (I use cheap acid cure stuff for mold making, 30A shore) <strong>(5ml total used)</strong></i></li><li><i>3D printed cableholder mould parts (Collet, core, female & male halves of the mould)</i></li><li><i>M3 screw & nut for the cableholder - collet clamp part.</i></li><li><i>M8 circlips/ external snap rings <strong>(2 used)</strong></i></li><li><i>External snap ring pliers</i></li></ul><h5>TOOLS:</h5><ul><li><i>Sandpaper <strong>(120 & 320 grit)</strong></i></li><li><i>Alcohol/Solvent (to clean the parts before bonding)</i></li><li><i>Syringe (to inject/force resin into the base) (16G tip works well too)</i></li><li><i>Mixing cups & stirring tool</i></li><li><i>Clamps or Rubber bands</i></li><li><i>PPE (resin is nasty stuff)</i></li></ul><p> </p><h3>BUILD GUIDE</h3><p>The whole construction process made up of 3 chapters; making the base, making the cableholder, and finally assembling it all together. The process of construction will heavily depend on what options you would like and the tools you have.</p><p><i> For instance if you choose not to use the silicone cableholder part, then you wouldn't need to print any of the silicone mould parts. If so, you could opt to use the standard printed cable holder in the </i><a href="https://www.thingiverse.com/thing:2436684/files"><i>original model's files</i></a></p><h5><strong>1. MAKING THE BASE</strong></h5><p> </p><figure class="image image-style-align-left image_resized" style="width:48.53%;"><img src="https://media.printables.com/media/prints/233462/rich_content/c2e00d6c-b08d-4722-8953-de445d207cc6/img_20220617_160100.jpg#%7B%22uuid%22%3A%2244988dc8-d956-429b-8664-fbcb0f13870a%22%2C%22w%22%3A4000%2C%22h%22%3A3000%7D"></figure><p>The hollow base has 3 holes, a larger hole in the rear and 2 smaller ones in the front to vent trapped air. Fill the hollow bottom 3D printed part with the weights (2.5mm ball bearings in my case) up to the brim from the rear hole, and then fill it with resin. A little overflowing is fine. After that is cured, sand it flat.</p><p>Bond the top and bottom parts of the base into 1 piece. First, sand the part of the halves of the base that mate together 120-grit sandpaper (the surfaces near the pins) then clean it to ensure good adhesion. Finally, apply the same resin used to encase the weights, clamp the top and bottom together and let it cure.</p><h5><strong>2. MAKING THE SILICONE CABLEHOLDER (Optional)</strong></h5><figure class="image image-style-align-left image_resized" style="width:22.72%;"><img src="https://media.printables.com/media/prints/233462/rich_content/bb0f95ae-19ab-4007-b3ad-f3d6e530105c/silicone-composite-cableholder.png#%7B%22uuid%22%3A%22cd60c7ed-b1ba-4d94-9464-ab7a0e1a110b%22%2C%22w%22%3A550%2C%22h%22%3A554%7D"></figure><p> </p><p>The silicone cableholder is an overmolded part, a 3D printed core is to have silicone rubber cured around it with a certain shape with the help of a mould. A simple split collet clamp is used in this case to prevent rotation of the core inside the mould. To do this, insert the pin of the cableholder core into the collet clamp, making sure that the curved surface faces away slit near the screw hole of the collet clamp. Line the surface said pin flush with the surface of the clamp (the part of the core with many holes will have a gap to the surface of the collet clamp). Then, insert the M3 nut & screw into the provisions on the side of the collet clamp and tighten until the core cannot rotate anymore.</p><figure class="image image-style-align-right image_resized" style="width:33.52%;"><img src="https://media.printables.com/media/prints/233462/rich_content/ff90c183-9745-45a3-964e-578c2d9578c5/img_20220601_081405.jpg#%7B%22uuid%22%3A%22023564ac-efb7-46f9-b26a-6b686090b66c%22%2C%22w%22%3A4000%2C%22h%22%3A3000%7D"></figure><p>Assemble the female and male halves of the mold and clamp them together. Mix some silicone then fill the cavity within the recently assembled mould. Insert the collet clamp-core assembly into the silicone filled cavity, submerging the part of the with many holes into the silicone, making sure the alignment is correct (the core has follows the general shape of the silicone mould opening). Some silicone will inevitably spill out, let it be as it's easier clean when cured. Clamp the collet assembly to the mould halves and let it cure for a duration depending on the silicone you used, (I used small rubber bands to clamp it and silicone I used dried after 3 hours). After it has cured, remove it from the mould and clean the flashings.</p><p>After the cableholder is done, it is time to bond it with the angled Bone2. Insert the cylindrical section of the cableholder, that was previously used to hold it in the collet clamp, into Bone2's hole. Ensure that it is angled parallel with the whole arm, and not installed upside down. Apply resin or superglue to bond them permanently.</p><p> </p><h5><strong>3. FINAL ASSEMBLY.</strong></h5><p> </p><figure class="image image-style-align-left image_resized" style="width:45.98%;"><img src="https://media.printables.com/media/prints/233462/rich_content/df5fd65e-89ee-4bf1-aac0-04d364caf2e8/img_20220211_190024.jpg#%7B%22uuid%22%3A%2244ecac42-2a0b-4604-94dc-aa0ad545a5c1%22%2C%22w%22%3A4000%2C%22h%22%3A3000%7D"></figure><p>Insert the rubber feet into the bottom of the base, they should fit into the groove.</p><p>Each of Bone1's holes have 2 sides to keep in mind, one side has a bigger opening to install a bearing, another smaller to keep it from falling out. The 2 bigger openings are not on the same side of Bone1. With this in mind, press the 2 bearings into Bone1, ensuring that they bottom out properly into their counterbores, this will requires some force so don't worry.</p><p>By now you should have <strong>3 assemblies</strong>; the <strong>Base</strong>, <strong>Bone1 with bearings</strong> and <strong>Bone2 with the silicone overmolded part</strong>. Assembly them all together, by inserting the plastic pins of the Base & Bone2 into the holes of the bearings, until they are bottomed out on their respective shoulders. They should be inserted from the same side the bearings were pressed in (the side of Bone1 with the larger opening, the side with the smaller opening should face away from the Base and angled Bone2). This ensures that the bearings are retained properly from both sides.</p><figure class="image image-style-align-left image_resized" style="width:26.62%;"><img src="https://media.printables.com/media/prints/233462/rich_content/f0ba5f61-ec5a-4391-991b-78337612e7c1/snap-ring.png#%7B%22uuid%22%3A%22f8ea5d0d-3b57-488e-b701-881f300438f0%22%2C%22w%22%3A766%2C%22h%22%3A514%7D"></figure><p><i>Though optional, installation of the external circlips/snap rings help to further secure the bearing from coming out.</i></p>
With this file you will be able to print Mouse Bungee - EVO with your 3D printer. Click on the button and save the file on your computer to work, edit or customize your design. You can also find more 3D designs for printers on Mouse Bungee - EVO.