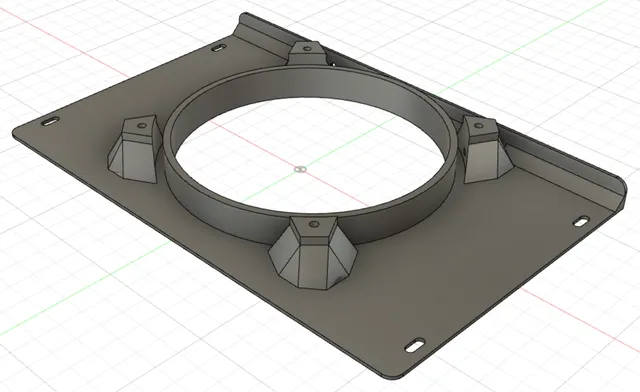
Mounting plate for 5.25" speakers in Stern pinball machines
prusaprinters
IntroductionRather than using an adapter insert, which will take up extra space and possibly create clearance problems behind the speaker, and which still leaves a 4" hole for the 5.25" speaker to play through, this mounting plate can replace the entire metal mounting plate that's in the machine and provide the necessary mounting bosses and studs for a 5.25" speaker to attach to.Update:The original version of this model didn't correctly center the speaker behind the honeycomb grid in the speaker plate of the pin. That wasn't so bad if the speaker is left unlit – it's barely noticeable. But with LEDs around the speaker, the lack of centering becomes obvious. I've updated the model to be centered properly.Which model should I use?There are a few variations on this model:LED-friendly. The main design accommodates those who might want to light the speaker with LEDs. It's printed as two separate parts, which allows you to print the speaker ring in a transparent filament, so that it acts as a diffuser for your LEDs.Even without the use of LEDs, this version has a couple of other benefits. Printing two smaller pieces is less risky, in the event of a print failure. Also, getting even the small hex key in position to secure the side screws (see below) is easier without the ring in place.This design can be downloaded either as a single STL with both pieces, or as two separate STLs. Most slicers should have no trouble letting you split a multi-object STL into its constituent objects. But if you have any doubts about doing that, go ahead and download the individual models separately. One-piece print. This version combines the speaker ring and the mounting plate into a single, solid print. Importantly, it does not have gaps between the mounting bosses and the speaker ring that would allow for LEDs to be wrapped around the ring.When I originally started this whole project, I was a little worried about the strength of the mounting bosses. After doing the “LED-friendly” version, I see that there's plenty of strength even with the bosses each standing on their own. But this version merges the speaker ring to the main plate, and the mounting bosses to both the plate and the speaker ring. This provides even more rigidity to the setup, even though strictly speaking it's not needed.Only use this version if you're sure you're not going to install LEDs at any point (or you will just print the LED version later if you do decide to). Phillips #1 screwdriver. For the first two options, you will need to get different screws for the side holes, with a hex-drive head instead of the Phillips screws that come with the machine. This is because even without the speaker ring, there's just not enough clearance to get a regular sized screwdriver into the space to turn the screws. But the small 1/16" hex key wrench fits easily, even with the speaker ring in place.But if you just happen to have a really short-shaft Phillips screwdriver, #1 or #0 (#1 fits the screws correctly, but you can get away with #0), then this option has holes through the mounting bosses large enough to accommodate the larger diameter of a screwdriver. In theory, this makes the two mounting bosses on that side a little weaker because of the larger hole, but again, there seems to be plenty of headroom with respect to the strength, and using this option means you don't have to find new screws. You do need that really short screwdriver though.I've also included smaller test print models. These are not for actual mounting, but they can be used to confirm your print settings as well as check the fit of the part that engages with the speakers, if you want to use this with a different speaker (see note in next paragraph). Each test model is just one mounting boss, which allows for: checking the fit with the speaker; verifying the through hole is large enough for the tool you want to use to secure the side screws; and letting you tune the print settings without printing the whole model (e.g., verifying that everything works okay even without supports enabled).Other combinations would have been possible to include, such as a one-piece that still had gaps for LED lights for those with multi-filament printers, but that need can be filled by the model I did provide, and all those different combinations would lead to too many STL files to choose from.NOTE: this was designed for and (so far) tested only using the Alpine S-S50 auto speaker. I don't know how will or even if this will work with other models of speakers. I'm guessing it will, since the mounting tabs themselves seem standardized, but I'd love to get feedback about whether that's actually the case or not.The Alpine speaker is not a flush mount speaker, and the speaker's mounting tabs are behind the front plane of the cone and the tweeter assembly. The clearances on this design accommodate this particular speaker's dimensions, to allow the woofer cone and tweeter assembly to remain behind the plane of the back of the mounting plate. This allows this same design to be used as the starting point in case someone wants to fill in the hole with a decorative grill; that could be done without interfering with the tweeter assembly. (The tweeter assembly on the speaker is moveable to fine-tune its direction, and this clearance accommodates the assembly even at its most extreme angle of direction).Tools NeededIn addition to your 3D printer and whatever miscellaneous tools you'll use to clean up the print…Socket driver with a 5/16" socket1/16" hex wrench or #1 or #0 Phillips screwdriver no longer than 3" total lengthSoldering iron or small-jawed pliers (e.g. needle-nose or electrical multi-function pliers) or Molex crimping tool #638190901 (this is a $300 tool…unless you just happen to already have one, you'll almost certainly go with one of the other options)Additional Hardware NeededIn addition to printing two copies of this plate, you will need some extra hardware to complete the installation. Here's a list along with some sources for the hardware.8x #6-32 ½" hex head machine screwshttps://www.digikey.com/en/products/detail/b-f-fastener-supply/HMSSS-632-0050/2618991https://www.mcmaster.com/92314A148/4x #6-32 nylon lock nutshttps://www.mcmaster.com/91831A007/https://www.pinballlife.com/6-32-nylon-insert-lock-nut.html4x #6 washershttps://www.digikey.com/en/products/detail/b-f-fastener-supply/FWSS-006/274946https://www.mcmaster.com/92141A008/https://www.pinballlife.com/6-8-10-washers.html4x #4-48 ¼" button head hex drive machine screwshttps://www.mcmaster.com/92949A327/4x #4 external tooth lock washershttps://www.mcmaster.com/98438A210/Optional hardware2x Molex 39012025 connector housinghttps://www.digikey.com/en/products/detail/molex/0039012025/9302714x Molex 39000073 connector socket (gold-plated)https://www.digikey.com/en/products/detail/molex/0039000073/3044236Hardware notes:The screw length given above is ½", but longer would be okay. One reason slightly longer screw might be preferred is it would make it a little easier to get the screw started when inserting it into the mounting plate. As it is now, with a ½" screw, the tip of the screw is just starting to engage the hole for the screw shaft when the head of the screw is starting to disappear into the larger hexagon hole. With a properly cleaned-up print, I didn't really have any trouble getting this all lined up, but I can see how for others it might be a little frustrating.You should only need 4 additional nuts and washers, because even though there are 8 screws, you already have 4 nuts and washers holding your 4" speakers in. Just reuse those.It's possible you already have enough washers. On my machine, for some reason a couple of the mounting studs for the plate itself had doubled-up washers, and on the other plate, it had extra washers under one of the clear plastic spacers that makes room for the foam screen. So, consider checking for these extra washers in your supply before you go shopping for hardware. :)If you use the alternate version of this, with the larger through holes that allow your Phillips screwdriver to fit, and you actually have a short enough screwdriver (3" or less) to be able to access the hole, you can also skip the #4-48 machine screws, and just reuse the Phillips screws that are on the machine now.The optional hardware is so that you can install the new speakers without modifying the old ones. If you don't mind desoldering the connector harnesses from the old speakers and reusing them for the new ones, you don't need the Molex stuff. Personally, I wanted to avoid making any invasive modifications to any of the stock hardware. Unplugging/plugging connectors, unscrewing/screwing fasteners, i.e stuff that was designed for easy removal or installation, is fine but I decided to draw the line at getting my soldering iron out when it came to any of the existing parts.Printing the PartSupportsYou can have success with a variety of print options. The one thing that is probably non-negotiable is do not allow supports to print in the through hole. Even that one, if you are sure you could get the supports out of the hole, feel free. But the hole is small enough that it should print fine without supports under pretty much any scenario, and I believe it would be a real challenge to get any supports out cleanly.If you're using PrusaSlicer (the only slicer I'm really that familiar with), use the “Paint-on supports” mode, choose the “Smart fill” tool type, and right-click anywhere inside the through hole. The slicer will exclude the entire interior surface of the hole from getting supports. Alternatively, at most you probably only need supports in the holes for the screws to go into the mounting bosses, so you can just set the supports only from the build plate, and the other places automatically won't get them.That said, I printed the entire thing without supports and it works fine. If anything, even the holes for the side screws came out better without supports. The hexagonal holes for the screws may or may not be an issue; I experienced a fair amount of stringing in those holes and it took a little work with a small (1/8") flat-head screwdriver to scrape the junk out. Using supports in these holes, you'll still get some scarring at the bottom of the hole (or “top” relative to the printing process), but at least with v 2.5.0 of PrusaSlicer, the supports themselves pretty much just pop right out.FilamentI used PETG. I was more concerned with strength than with rigidity, and I feel like the PETG is a bit more forgiving in that respect. But I would guess this would work fine with PLA, ABS, or even more exotic materials, and you might get something that is closer to the metal in terms of its mechanical properties. I don't really think acoustic resonance is an issue in this application, but I can't say for sure.Another reason to use something other than PETG is that PETG comes out pretty glossy. I guess you could print at a low enough temp that it gets a matte finish, but then I'd worry that the print wasn't strong enough. PLA or ABS would probably be less shiny, so fewer reflections (if you leave the foam screen out when installing this).Other SettingsI printed at 0.1 mm layer height, and 20% infill, using the gyroid pattern. With less infill, I found that the top of the mounting boss deformed a bit, pushing through the speaker's oval mounting hole, when the nut was tightened down. That issue was addressed completely with 20% infill.You're barely going to see this part, so I would guess than a 0.2 mm layer height is probably fine.There should be no need for a skirt or a raft. Just make sure the build plate is nice and clean before you start. There's plenty of surface area for adhesion on the part, and you'll appreciate the smooth or textured surface facing you (again, only really matters if you take the foam out).InstallationPreparing the Printed PartAfter printing, clean up the part to your satisfaction. The only thing that's really important is to get the screw holes cleaned out, but you may want to take care of other aesthetic issues.I used a couple of small screwdrivers to clean up the screw holes. A 1/8" flat-head screwdriver works to scrape out any debris from the hexagonal hole, while a #0 Phillips screwdriver works well to ream out the round hole for the screw shaft.It also helps to use the machine screw itself to clean out its hole. Insert it from the top/back side of the plate (i.e. the “wrong” side), so that it's easy to get the screw shaft into the hole.Once everything's cleaned up, it should not be hard to drop the screw from the front side of the plate and push it through the hole so that the head of the screw is at the bottom of the hole. There should be about ¼" of the screw sticking out when the screw is all the way in. If not, push it in more, or just put a washer and nut on it and gently tighten the nut to pull the screw the rest of the way in.Once all four screws are in, they should stick out of the back of the plate, from the top of the mounting bosses, similar to the studs that would be on the metal plate.Assembling the Molex ConnectorIf you are just desoldering the Molex connector harness from the old speakers and soldering them back to the new speakers, skip this section.The Alpine speakers come with wire pairs that have quick-connects on the speaker end, and the other ends stripped but otherwise bare. Crimp a Molex connector socket onto the end of each bare wire, then insert each connector into its Molex housing:Molex has a special tool for crimping, but with a steady hand and reasonably small pliers, you can do it without their tool. Just be careful to fold the crimp tabs over one at a time, being sure to secure the strain relief first over the insulated part of the wire, and then crimping down the tabs over the exposed conductor.When crimped correctly, no soldering is needed. But if you want to ensure a solid connection, you can still solder. Just make sure to apply the solder sparingly, just enough to flow into the copper strands and make contact with the inside of the crimp. Too much and the connector will get too fat to fit into the housing. When inserting each connector, pay close attention both to its position and its orientation.On my machine, the speaker negative goes on the side of the connector with the clip, but I don't know how standard that is. Look at your machine's wiring to be sure (the negative is the black wire and on the wiring that comes with the speaker, it's the wire with the black stripe; these need to match up when the connectors are connected).As far as the orientation goes, the connector has a couple of “wings”; these slide down the slots inside the housing. The connector also has one side that's rounded. If you look inside the housing, you'll see it also has a side that's rounded. Just line these all up, and the connector should slide easily into the housing until the wings get far enough and expand in the housing to secure the connector.Once the Molex connectors have been added to the wires that came with the speakers, just slide the quick-connects onto the speakers on the appropriate tabs.Moving the Molex HarnessIf you added Molex connectors to the wires that came with the speakers, skip this sectionInstead of using the wires that came with the speakers, you can just desolder the wires from the old speakers and use these for the new ones. Just make sure to get a good solder connection, and to attach the wires properly by soldering the black wire (negative) to the narrower speaker terminal and the red wire to the wider one (positive).Installing the PlateFirst, decide whether you want to keep the foam screen installed that the machine comes with. If you do, leave it in place while you remove the old metal plate. Either way, unplug the speaker, remove the nuts and washers holding the speaker down, and remove the speaker itself. Then remove the screws on the side of the old metal plate holding it to the metal frame for the game's display, and nuts and washers holding the old metal plate down, and then remove the plate.If you're taking the foam screen out, then also remove the plastic spacers at the top and bottom of where the foam was.Now we're ready to put things back together. Start by sliding the plate down over the screw studs, so they go through the oval holes in the new plate.The most finicky part of this is getting the side screws in. I found it helps to use small needle-nose pliers, or something similar, even just an alligator clip, to hold the screw while the tool goes through the hole in the mounting boss to engage the screw. (At this point you're using either the hex-drive screw or the original Phillips head…obviously, use the appropriate tool for the screw). Make sure you don't forget to reattach the green ground wire that's on the right side of the machine when you screw in that screw.Note that the metal frame for the LCD display floats in the drop-down door, so you may have to push it a bit to get it aligned with the mounting plate.Once everything's lined up right, screw the two side screws in, but don't tighten them all the way. Instead, get the washers and nuts for holding the plate to the door started, then push the plate up flush against the cover for the display and tighten down the nuts for the plate. Don't forget to attach the wire guide and the door support string back where you found them before you put the washer and nut on.Once the plates are tightened down and flush against the display's cover, you can now finish tightening the side screws, take care to keep the metal display frame centered so that when you're done you've got about the same tension on all four screws, with them reasonably tight, and the display is centered perfectly between the speakers.(To be honest, there's only a millimeter or so of play in the display position so you could probably get away with not being so careful about that last bit. But I figured I'd mention it anyway, for the perfectionists among us. :) )Installing the SpeakersCarefully lower the speaker down onto the screws sticking out of the back of the mounting plate bosses. Get too sloppy here and you might poke a hole in your brand new speaker!But if you do it right, the speaker will slide nicely over the screws, and then fit securely over the bosses and the circular perimeter that mates with the gasket in the speaker. At this point, the speaker should be able to move only very slightly from side to side and will be centered nicely over the plate and large hole.Put washers on the screws, then start the nuts. Tighten them down just enough to pull the speaker's mounting tabs to touch the mounting boss on the plate. Once all four tabs are down, go back and tighten each nut about a quarter- to half-turn more, just enough to get the speaker snug. No reason to over-stress the mounting boss; the nuts should stay put, and you just need the speaker to not be vibrating on the mount.Plug the Molex connectors together for each speaker, optionally securing the wiring in the wire guide next to each speaker, and close up the machine.Adjusting the Audio SettingsYou might be tempted to change the speaker impedance setting to 4 ohms for your new 4 ohm speakers. Don't bother. I don't know what the point of this setting is, but all it does is drastically reduce the volume of the audio for the new speakers. Just keep the original 8 ohm setting for the backbox speakers.You may also want to change the EQ settings to “None”. I found that I seem to get audio that is actually louder and clearer with the “None” setting than if I turned on the 10-band equalizer or used the “shelf” option.Of course, you should set these to whatever you feel sounds the best. But for me, I feel like built-in audio filtering just makes things sound worse.Indeed, before you go through all the above, you might consider making the EQ change to “None” first and see if/how it improves the sound from the 4" speakers the machine came with. :)
With this file you will be able to print Mounting plate for 5.25" speakers in Stern pinball machines with your 3D printer. Click on the button and save the file on your computer to work, edit or customize your design. You can also find more 3D designs for printers on Mounting plate for 5.25" speakers in Stern pinball machines.