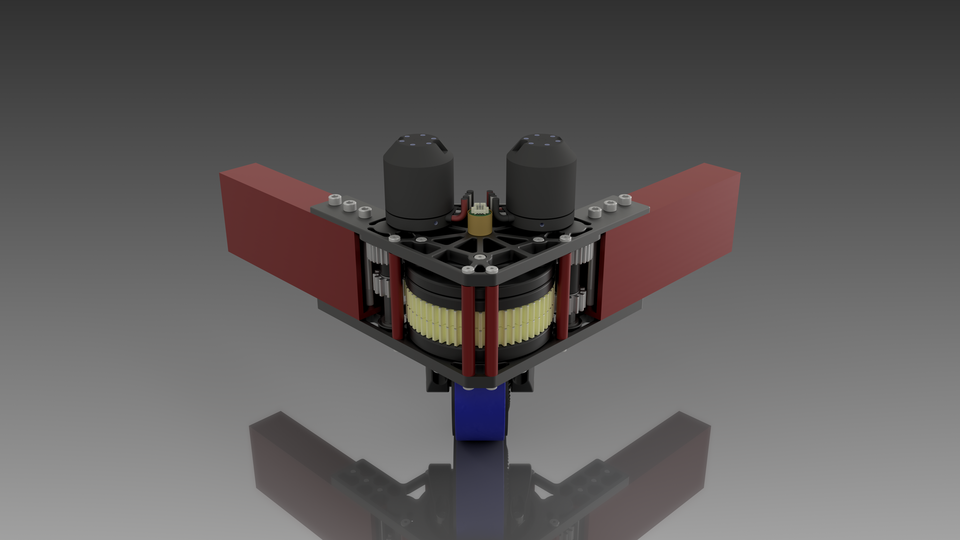
MK2 Differential Swerve (2.845lbs)
grabcad
For quite some time now, I've been eager to design a new differential swerve that improves upon my previous one (FRC 2 Neo Differential Swerve Module). The latter had some areas for improvement, and with the recent availability of free time over the past couple days, I was able to work on a new module. I'd like to share my Differential Swerve MK2 with you. There were three key areas I aimed to enhance in this model compared to the previous one: 1) Increased ground clearance, comparable to that of a traditional swerve (around 1.5in-2.5in target), and 2) Reduced weight (Sub 3lbs target), as well as 3) Reduced used space inside of frame length/width (Sub 3in in X and Y target). Along with these requirements, I also wanted to include a few other features in the design: 1) Easy replaceability in case of mechanical failure. 2) Seamless integration with the frame. 3) The wheel pivot point as close to the corner as possible for a wider wheelbase. 4) High use of 3D printing technologies. Some major differences between the MK1 and the MK2 are: - A new style of differential mechanism - Use of 2x Neo 550s instead of 2x Neos - Instead of being nested into the frame, it acts as a structural member - Use of custom bearing setup instead of COT bearings to save weight I opted for a new style of differential mainly because this setup is far easier to modify and adjust ground clearance depending on requirements. The new design also lent itself more easily to my custom bearing setup than the differential I used on my MK1. My original plan was to use two 775 Pros instead of two Neos due to their smaller diameter, but I ended up choosing to use two of REV's new Neo 550s as they are shorter and sport an integrated encoder. However, this design could easily be modified to use 775 Pros. The MK1 module was nested into the frame to reduce its footprint inside the frame. In contrast, I decided to integrate the MK2 as a structural member for two main reasons: first, to again reduce the inner frame footprint, and second, to allow the module to be able to slide out diagonally from the frame if/when it needs to be replaced. While this module has many advantages, there are a few things I will improve in the MK3 when/if I design it: 1) Reduce the total height of the module (sub 4.5in) 2) Reduce the need for ultra-high precision machining 3) Reduce the number of heavily modified/custom COTS parts (mainly in terms of gears) 4) Reduce part count 5) Allow for easy servicing of the module for repairs while installed Critics, comments, and questions are always welcome!
With this file you will be able to print MK2 Differential Swerve (2.845lbs) with your 3D printer. Click on the button and save the file on your computer to work, edit or customize your design. You can also find more 3D designs for printers on MK2 Differential Swerve (2.845lbs).