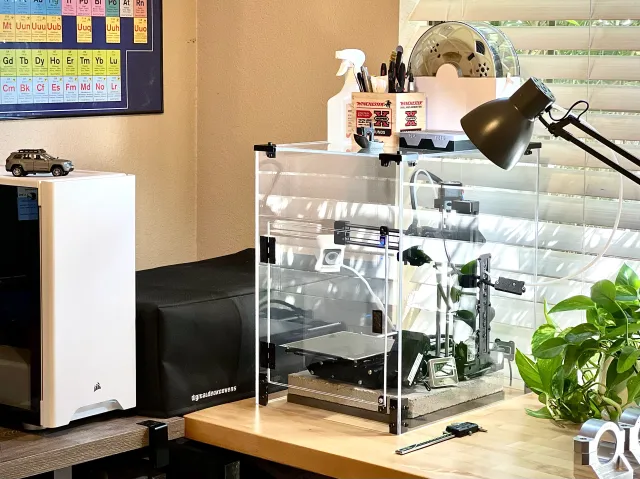
Minimalist Enclosure for Prusa Mini
prusaprinters
This enclosure was developed out of specific needs that I had that couldn't be met anywhere else, but it gained some traction and folks asked that I share it, so here we go! There’s three reasons why I designed this from the ground up: Everything out there is huge, and with my limited space, I wanted an enclosure that’s as small as possible (full clearance around the printer, including cable rubbing, was considered in the size.) I wanted an enclosure that’s easy to remove, break down, and store when not needed. Just unscrew a few bolts and the panels can be stacked and stored. I'm an engineer and I really enjoy designing, analyzing, and developing new things. I only buy something off the shelf if I can't make it myself! All parts except the acrylic, rubber grommet, and fasteners are 3D printed.IMPORTANT NOTES:This will only work with the USB port relocated to the front LCD display - or using the new WiFi/PrusaLink update. THERE IS NO ACCESS TO THE REAR USB PORT (Unless you make one 😄). I suggest you make these changes if you haven’t yet anyway. I highly recommend that you’re ”handy” for this install, meaning you’ll need to be able to cut acrylic with a good saw and have some sense of how to put things together. My instructions are just a guide - feel free to approach this however you’d like! I didn’t design this with the general population in mind and to be “IKEA” simple, but with that said, placing the holes is probably the most challenging part since that can take some precision and bit of thought. I have tried to describe things the best I can though. Have fun!! Parts List0.22” Thick Acrylic SheetsThat is thick! But it makes for a rigid, quality enclosure1,944 in^2 worth of materialI did this with (x1) 36x30” sheet and (x2) 24x18” sheets (layout below)Or use an online calculator to plan and optimize cuts depending on what’s available in your area: https://www.opticutter.com/cut-list-optimizerhttps://www.homedepot.com/p/OPTIX-18-in-x-24-in-x-220-in-Acrylic-Sheet-MC-21/202038050https://www.homedepot.com/p/OPTIX-30-in-x-36-in-x-220-in-Acrylic-Sheet-MC-22/2020380521/32” Thick Rubber Sheet for Cable Pass-Through Grommets8.5 in^2 worth (+extra if you mess up!)I purchased a 9x12” 60A durometer sheet off amazon for $10https://www.amazon.com/dp/B0B47NM4Q2?psc=1&ref=ppx_yo2ov_dt_b_product_detailsBrass Threaded Inserts and Soldering Iron for Install (Size x Length x Diameter)(x4) M5x6x7(x30) M4x6x6 (I purchased a large set of these and the M4 screws)(x6) M2x4x3.5https://www.amazon.com/dp/B08Z86Z85R?psc=1&ref=ppx_yo2ov_dt_b_product_details(Bolts/Washers/Nuts) [Drill size for clearance hole in acrylic]: Location used(x4/x4/x0) [7/32] M5x20: Top panel bracket(x30/x30/x0) [3/16] M4x10 (or longer): Top and lower brackets(x8/x8/x8) [9/64] M3x10 (or longer): Door hinges(x20/x34/x14) [3/32] M2x10 (or longer): Door stops, knob, and grommet housingshttps://www.amazon.com/gp/product/B08ZCN8L7D/ref=ppx_yo_dt_b_search_asin_image?ie=UTF8&psc=1Magnets for door(x4) 6x3mm https://www.amazon.com/gp/product/B07KXWSM4Y/ref=ppx_yo_dt_b_search_asin_image?ie=UTF8&psc=1PETG FilamentI highly recommend sticking to PETG or better (ASA, PC, Nylon, etc) so the parts don’t warp overtime from the warm enclosureLabeled parts to be printed: Build GuidePrint all the parts! This can be done while working on the next step. Cut the acrylic sheets. Below is the sizing for each of the panels. This is exactly how mine is made and it works well, HOWEVER, if I did this again, I’d make the Front/Back and Top panels .25” wider to give a little more clearance, so I’d recommend 13.94” instead of 13.69” wide for the Front/Back and 13.32" instead of 13.07" wide for the Top. Also, the overall height is 19.72” which includes space for my 2” high paver stone for sound dampening, so if you don’t have that then 2 inches can be removed, so 19.72” would become 17.72”. After tracing out the panels, I used a track saw to accurately cut out each panel.To cut out the door, I cut most of the way on each side, and then finished the last half-inch or so with my jigsaw. The door-frame gap is as wide as my saw blade (0.09", but this dimension is flexible).The grommet pass through slots can be cut out using a jigsaw since jagged edges will be hidden by the grommets (be sure to smooth them out though!). Drill a large hole in the center of the slot to make a space for the jigsaw to get started.Front Panel Door Dimensions (measurements for lines to be cut). Keep in mind, the bottom distance is to account for my 2" paver stone. If you don't have one I'd make the 1.955" about 1.0". Side Panel Filament Grommet Pass-Through Dimensions. Again, this height is precisely set for my 2" paver stone. If you don't have one, the bottom dimension should become 2.25" instead of 4.25". Back Panel Power Grommet Pass-Through Dimensions. Again, this height is precisely set for my 2" paver stone. If you don't have one, the bottom dimension should become 1.0" instead of 3.0". Sand panel edgesI used a metal file to smooth out the really rough edges. Then moved to 120 and then 220 grit sand paper. This made the edges very smooth, but didn’t look the best. YouTube videos show how the they can be made to look perfect if you keep sanding up to 800 grit with certain techniques, but this wasn’t something I needed.Install all brass inserts in printed parts using a soldering iron.The lower brackets use x4 M4 inserts eachThe top corner brackets use x2 M4 inserts on the sides and x1 M5 eachThe door knob and door stops use x2 M2 inserts eachAlso, push magnets into door stops (no glue should be needed)Drill holes in panels using the printed brackets as guides. Follow this order for ideal bracket hole placement.Pro tip 1: Place masking tape on the panels in the approximate hole location to make marks for drilling.Pro tip 2: Drill a small pilot hole first to relieve stresses in the acrylic, and **DRILL SLOW** or you can crack the acrylic!! Start with the SIDE panels by installing the lower brackets only. NOTE: The lower brackets have a long side and short side. The long side of the bracket will install on the side panels (0.625“ from the edge when flush against the vertical face). See images below for clarity. Next, drill holes for the lower brackets on the front and back panels.I’d recommend keeping the brackets installed on the side panels, and then holding the front/back panel flush to them and mark holes to be drilled. This way no measurements are needed for the holes. The front/back panels sandwich the side panels.Next, drill holes for the top corner brackets on the front/back and side panels.This can be done a few ways: 1) measuring the holes manually 2) doing just the front/back alone or 3) all together at once. I’d recommend the last one.All 4 panels should be held together at the lower corners with the lower brackets. At this point, simply slip on the top brackets, mark their hole locations, and drill. Next, drill holes in top panelThis is the easiest one: make sure all sides are secured with the top and lower brackets (slip in the top panel before securing one of the side panels). Then, mark the top panel hole locations and drill them out. Next, drill holes for the front panel door featuresFor the hinges, lay the front panel so it’s completely flat with the door centered in the frame. Lay the hinges so they’re approximately 1.25” from the top and bottom, with the hinge “pin” centered on the door gap, then mark the hole locations using the hinges as a template. Make sure the hinges are straight.For the door stops, place the corner locating feature on the printed part in the corner of the door frame and mark the hole locations. After the stops and hinges are installed, close the door and mark where the door magnets should be located with respect to the door stops. Use a ¼” Forstner bit to make a flat hole ~3mm deep in the door and glue in the door magnets (make sure you have the polarity oriented correctly!). Center the door knob on the door and mark its holes. Placement isn't critical, just make sure it's mostly centered so the force of opening the door is distributed between the magnets equally. Next, drill holes for the grommet housingsThe filament grommet hole spacing is shown below. I’d recommend locating one hole (top right) accurately, then placing the printed housing on the panel and using it as a template to mark the others. (Or just center it on the cutout) The power cord grommet hole spacing is shown below. I’d recommend locating one hole accurately, then placing the printed housing on the BACK panel and using it as a template to mark the others. (Or just center it on the cutout) Create the filament and power cord rubber pass-through grommets Use the printed grommet templates to cut out the rubber grommets using a hobby knife/X-Acto/razor blade. Make sure the rubber doesn’t slip while cutting. I did this by taping the template down on top of the rubber and onto a cutting surface. The grommet template is the exact size that the final rubber grommet should be, so cut around the outer edge for the overall size. Installing the pass throughs on the panels is a little tricky because they want to fall into the slots. Gently hold the rubber to the acrylic panel with the printed grommet housing, insert the fasteners and tighten them down. When complete, the rubber should be held tight to the panels and won’t budge. Screw all the panels together and admire your accomplishment! Slip the completed enclosure over the printer Slip power cable, the bowden tube and filament sensor through the pass through grommetsIn an effort to keep heat in, I made the pass through as narrow as possible, which results in the filament sensor needing to be disassembled to slip through the grommet. Not ideal, but it is easy. Just remove three screws on the sensor, remove the wiring assembly, pass it through the grommet, then reassemble. Done! I’ve already planned future upgrades and accessories for this project! They include: Corner mount for Wyze Cam V3Hanging tool storage UPDATES: Added top panel support brackets. I started using the top as storage more than I thought I would, and although it didn't sag much, I figured some support brackets wouldn't hurt. These are an easy add on - just center them at the top so there's very slight pressure against the top panel, then mark the hole locations and drill. Buy me a coffee or beer for my trouble - thank you! Venmo: @TuckerPorter
With this file you will be able to print Minimalist Enclosure for Prusa Mini with your 3D printer. Click on the button and save the file on your computer to work, edit or customize your design. You can also find more 3D designs for printers on Minimalist Enclosure for Prusa Mini.