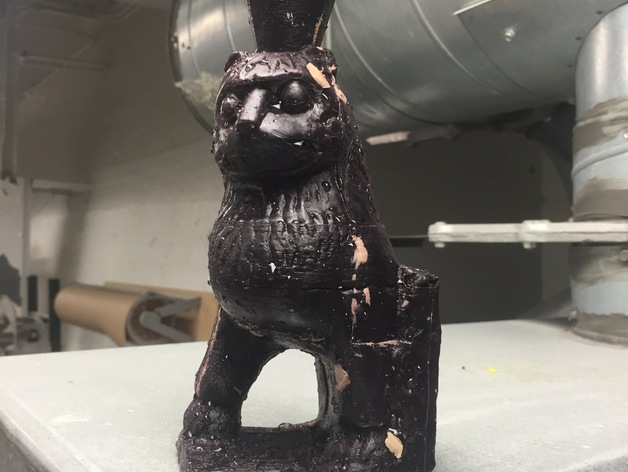
Lost Wax Mold (Lion Protome)
thingiverse
In the sweltering heat of summer, I initiated an experiment to test whether 3D printed PLA molds could be utilized to create intricate wax positives for lost-wax casting. My preliminary attempts with straightforward cylindrical forms were fairly successful. Four-part molds, 3D printed with support material, sanded slightly, and a generous dose of mold release proved effective. Two-part molds and rough plastic, however, were not as successful. Keeping this in mind, I wanted to explore if a complex 3D scanned part could also produce a lifelike wax replica for potential casting later on. This would be the elusive solution where we could circumvent the mold-making process entirely for foundry outcomes. I chose my 3D scan of the Lion Protome in the collection of the Art Institute of Chicago as my subject matter. I have adopted this lion as my go-to model for 3D printing and 3D scanning demonstrations and workshops. It's a fantastic object to scan, resulting in high-quality scans with Recap and 123D Catch using 50 or more photos. It's also an ideal object to print, boasting steep enough features that require support material but often print flawlessly without it. I believe there's much 3D print designers can learn from ancient sculpture, where artisans had to accomplish a great deal with minimal resources. Specifically, they excelled at handling unsupported overhangs and other details despite the lack of right angles throughout their creations. To share more about this process, please visit http://tomburtonwood.com/2015/10/3d-printed-mold-making-pt-4/. Print Settings: Rafts: No Supports: Yes Resolution: As low as you wish to go. Any lines will be interpreted by the wax and remain in the final object. Infill: 10 - 15% should suffice, though more is always better. Notes: Smooth out the rough areas resulting from support material. Fill any holes in the floor or sides with a soft material prior to casting. How I Designed This Rhino has an aversion to meshes. And Recap/123D Catch doesn't export NURBS/Solids either. What to do? Not perfectly, but here's my workflow: Locate the mesh/3D scan inside multiple volumes, leaving ample space top and bottom. Modify these volumes to minimize plastic usage in the printing process without compromising the part's strength. Identify the parting lines and use WireCut tool to split the solids into their respective parts. Visualize whether the mold section will detach cleanly from the model, considering friction. Create keys using nested spheres or similar volumes as needed. Attach them to one face and subtract the larger volume from the other. Solid > Union and Difference commands come in handy for adding and subtracting as required. Backup and save everything to a new layer, locking it up for good measure. Run Mesh > From NURBS Object command on each mold part individually. Run Mesh > Boolean Difference on each mold part, subtracting the model from it until each mold section accurately replicates its respective portion of the model. Be cautious not to delete any input with each difference command. Verify the part; hide mold sections – does it seem feasible? If not, add more parting lines, keys, etc (useful backup comes in handy here). Export each mold section as your preferred file format. Print with support material (if needed). Remove supports and sand down any burrs that may remain. Fill any holes with oil clay or another malleable substance.
With this file you will be able to print Lost Wax Mold (Lion Protome) with your 3D printer. Click on the button and save the file on your computer to work, edit or customize your design. You can also find more 3D designs for printers on Lost Wax Mold (Lion Protome).