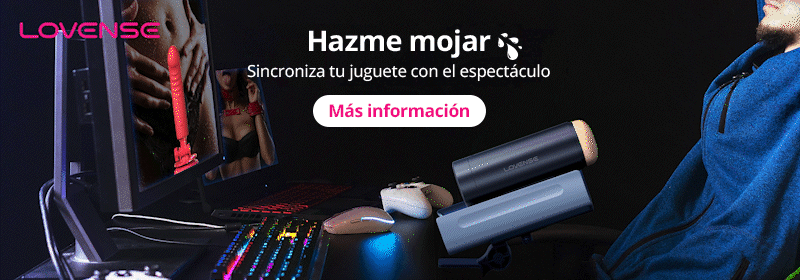
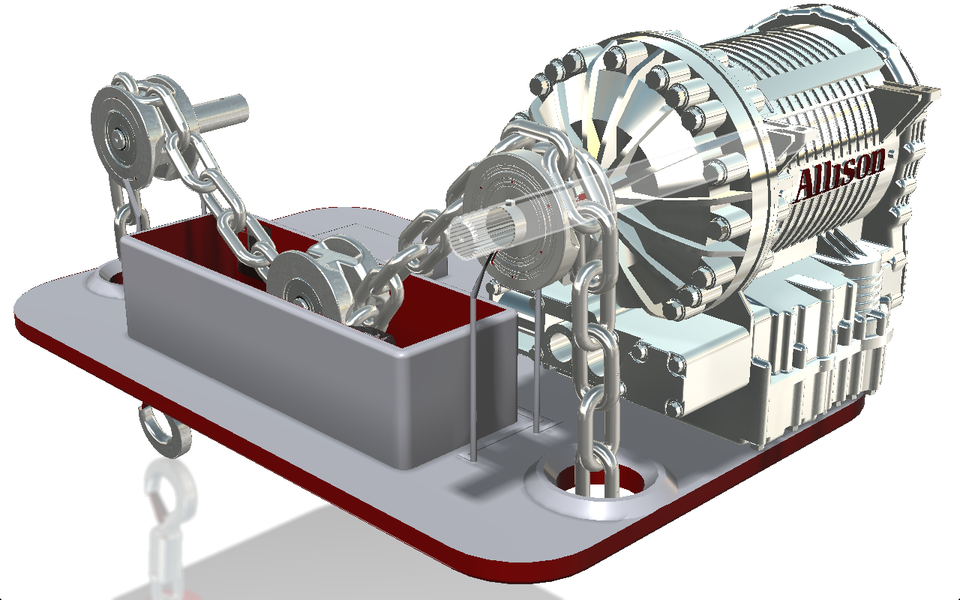
Konecranes chain analyzer
grabcad
In this design, two strain gauges are placed on opposite sides of a water container for measuring vertical water displacement; by using two strain gauges, the top surface of the water can be determined, even if the crane was on an incline. The strain gauges will be connected to a control unit (CU), which is also connected to orbital wire conductors on rollers for phase change synchronization. The CU detects any unusual resistance changes in the amplitude of sine waves when the strain gauge encounters a deficiency of chain. To minimize water-surface interaction, a superhydrophobe can be applied to the chain and pulley system. An ionic compound like anti-freeze is proposed to keep evaporation to a minimum and lower the freezing temperature for low-temperature use. The strain gauge is glued on to a waterproof sheet, which is then glued to an aerogel or sponge material that can be compressed when water presses against it. The top of the aerogel or sponge material remains unsealed for gas pressure changes, while the conductance of the strain gauge changes due to bending moments from changing water pressure. Orbital wire conductors are placed on each roller with two conducting rings – one front and one rear. The electrical signal passes through a channel in the roller, connecting the CU, rear rod, rear orbital ring, front orbital ring, and front rod. A gap on the front ring causes the electrical signal to fall to zero when directly over the connecting rod, which can be used to determine phase changes in both rollers for measuring chain section length. Optional load cells are offered for high accuracy. These load cells would give density for each chain and allow the CU to calculate roller cylinder bending errors. Load cells are connected via orbital rings, with six rear orbital rings, six load cells, and six front orbital rings. The production costs of this design are below 50€ (without load cells). The margin of error for strain gauges in volume measurement is ±0.5%, while the superhydrophobe layer on the chain has a ±0.1% error rate. The orbital wire conduction system has a ±0.5% error rate (optional load cells have a ±0.1% error rate), and potential issues include cracks, nicks or gouges in strain gauges, severe corrosion, deviations in gauge length, and rough roller surfaces indicating rapid wear.
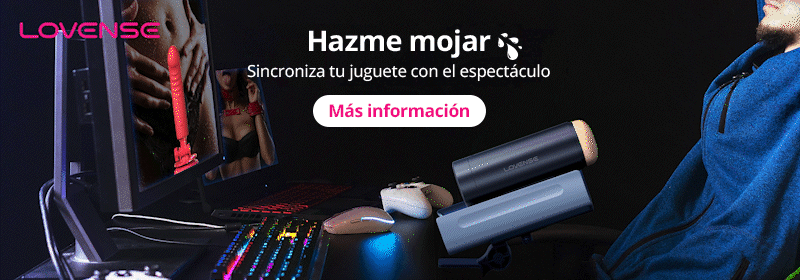
With this file you will be able to print Konecranes chain analyzer with your 3D printer. Click on the button and save the file on your computer to work, edit or customize your design. You can also find more 3D designs for printers on Konecranes chain analyzer.