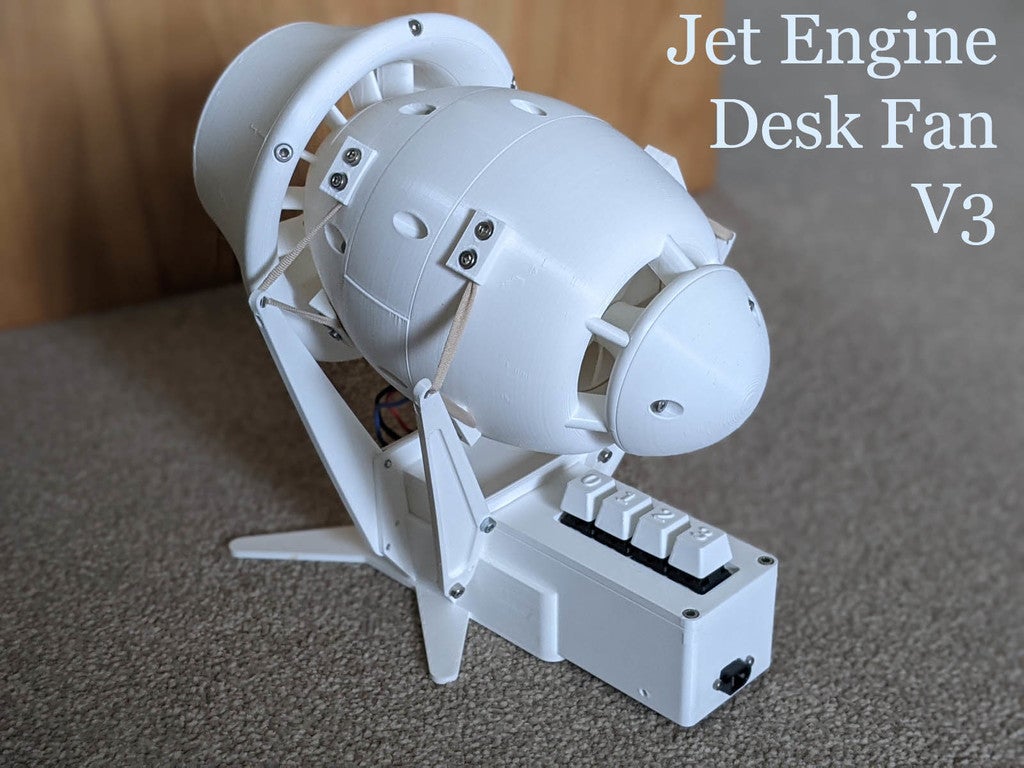
Jet Engine Desk Fan V3
prusaprinters
<p>This is the latest (maybe final?) version of my printed desk fan project and it's the first one that is actually a practical fan.</p><p>The fan uses a centrifugal compressor to generate airflow, driven by a brushless DC (BLDC) motor that is controlled by a BLDC motor driver and an Arduino nano.</p><p>Is the fan quiet? It's not <i>offensively</i> loud (in my opinion) but it is in <i>no way</i> silent or even particularly quiet; it makes a whining noise from the motor drive and there is clear noise from vibration of the rotor (this will be reduced if your rotor is well balanced). The airflow from the fan is very smooth, however. There is no choppiness that you get from open blade fans and the airflow is very directed so you can have it further away than standard open blade desk fans.</p><p>The shroud around the nozzle was supposed to help entrain more air into the jet - I'm not sure it works. The inlet probably should be larger for efficiency but I didn't want to allow a gap big enough easily to let fingers in. With that said: children's fingers might still fit in and while the distance from the intake to the compressor is big enough that people will small enough fingers to get into the gap wouldn't reach the blades I would STRONGLY suggest that you keep this out of reach of children.</p><p>Was it aerodynamically designed? No, not at all. I followed some principles in turbomachinery books (mainly this one <a href="https://www.pearson.com/uk/educators/higher-education-educators/program/Saravanamuttoo-Gas-Turbine-Theory-6th-Edition/PGM838584.html">https://www.pearson.com/uk/educators/higher-education-educators/program/Saravanamuttoo-Gas-Turbine-Theory-6th-Edition/PGM838584.html</a> in a much older version) but this is<i>all</i> eyeballed. If you can actually design compressors maybe you can make it better? At least the stators in this version point the right way, I got them the wrong way around on the first draft.</p><p>The motor is an 1806 2300kV motor, like this: <a href="https://uk.banggood.com/Flashhobby-BE1806-1806-2300KV-Brushless-Motor-Black-Edition-for-Multicopters-p-946416.html">https://uk.banggood.com/Flashhobby-BE1806-1806-2300KV-Brushless-Motor-Black-Edition-for-Multicopters-p-946416.html</a></p><p>The brushless motor controller I bought is this one: <a href="https://hobbyking.com/en_us/afro-30a-race-spec-mini-esc-w-bec.html">https://hobbyking.com/en\_us/afro-30a-race-spec-mini-esc-w-bec.html</a> it's discontinued now but the new ones seem to be smaller and so should work just as well. The BEC from the motor controller is used to power the Arduino.</p><p>The Arduino that controls the motor is like this: <a href="https://store.arduino.cc/arduino-nano">https://store.arduino.cc/arduino-nano</a> I used a perfboard sheet, sockets, pin headers and wires to connect all the parts (see the code for pins to connect).</p><p>Power comes from a 12V laptop power supply, you will need to choose the rating of your supply based on your motor controller. Mine was able to take 4S LiPo voltage (16.8V max) so 12V was comfortably in this range. The barrel jack from the supply fits in a socket in the electronics box. This was connected to the motor controller wires with screw terminals which is shonky but effective as long as you don't want to use it with proper connectors again. If you do you might want to find proper connectors that you can solder to the socket.</p><p>It uses four Cherry MX-style key switches that I had left from a project, printable keycaps are included but these take a good printer to work well. If you can't print them most standard keycaps should work if you buy standard switches. You can substitute tactile switches or any other momentary switch if you'd rather but the clicky key switches are quite nice. One terminal for all of the switches are connected to a common ground wire. The other terminal of each switch is connected to the pins that are used for detecting button presses. In the Arduino code the internal input pullup resistors are used so connecting the pin to ground when the switches are closed pulls the pins low, the code detects which pin is low and uses that to set the speed. You might need to experiment with your speed controller to find out which speeds work well, mine has low speed set to the lowest speed that the compressor would reliably run at.</p><p>Motor cooling seems to be adequate, I've monitored the temperature of the motor with a thermocouple over long periods (1hr+) and the temperature stays comfortably lower than 40degC (101degF, 313K) at all speeds so there should be no problem with PLA mounts getting soft. The motor controller doesn't seem to get hot enough to cause problems, even though the box doesn't have ventilation (you could add this if you wish).</p><h3>Post-Printing</h3><p><strong>Assembly</strong></p><p>The parts are assembled with M3 socket cap machine screws, I bought a box of mixed sizes but most holes will work with 6mm screws.</p><p>In all cases screws will fix into ~2.5mm holes, these must be reamed (ideally by hand) to exactly 2.5mm and then tapped for M3 threads. Holes that the screws pass through can be reamed to 3mm.</p><p>The motor is fastened to the mount with screws that should be included with it. The rotor is fixed to the mount plate that is fixed onto the motor. At the intake end of the rotor there is a 2.5mm hole that is tapped for an M3 screw, a ball bearing with 3mm inner diameter and 10mm outer diameter is screwed into this hole, with a washer as a spacer between the rotor and the bearing.</p><p>There is a motor balance test stand included in the parts, this should help to ensure that the rotor is correctly balanced and tuned. It is possible that the rotor will not be 100% balanced if your printer does not print perfectly square. Note that even if your bed is levelled this is not a guarantee that the axes are all perfectly square. The motor mount plate includes adjustment for the mounting to ensure that it is as balanced as it can be.</p><p>The main fan unit is fixed to the base with elastic suspensions, I used elastic that I bought to make face masks. This elastic mounting is to reduce the vibration that is transferred to any surface you put the fan on, perhaps your printer will be more precise than mine or your balancing will be better but I found it much quieter with the elastic suspension cords.</p><h3>How I Designed This</h3><p><strong>Design</strong></p><p>The parts are prepared in OpenSCAD but some of the profiles were created in Fusion 360. The OpenSCAD files will be included once they are edited and commented for clarity along with the files exported from Fusion360. I don't have access to Fusion360 any more so these parts of the design will not be included as editable CAD files, they are just STLs.</p><p>Be warned - some of the code for generating the blades in OpenSCAD is deep magic, I have no idea how it works, I wrote it years ago and I can't remember what I did any more. If you think you want to change it or try to understand it feel free but I can't help.</p><h3>NOTES:</h3><p>Not all parts from this model need to be printed or even downloaded unless you want to alter the design or re-render the parts using the *.scad file. Parts needed for printing have “Print one” or “Print two” etc. The other parts (exports from Fusion360) are <strong>not needed for printing</strong> being only processed in OpenSCAD to produce the print files.</p><p>Category: Household</p>
With this file you will be able to print Jet Engine Desk Fan V3 with your 3D printer. Click on the button and save the file on your computer to work, edit or customize your design. You can also find more 3D designs for printers on Jet Engine Desk Fan V3.