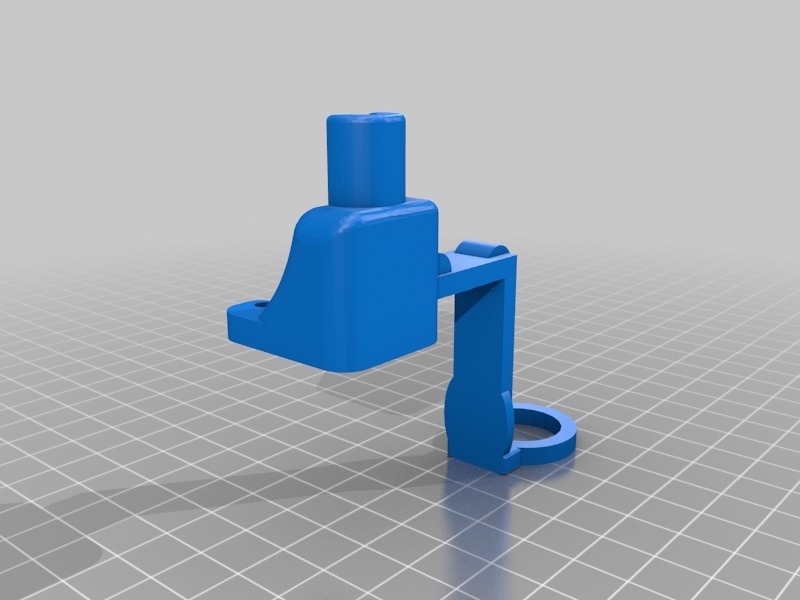
Inductive Probe Edition
thingiverse
**update*** inadvertently uploaded the prototype mount... correct ABL mount uploaded. This project is a work in progress, and I take no responsibility for any damage it may cause to electronics or starting fires. This was made possible by adapting many online resources for use on the Gen L board. I'd like to thank Mertarauh, a legend in the field, for sharing his expertise: https://mertarauh.com/ (a must-read). The goal is to add an Inductive sensor/probe to the JGAurora A5. This is the prototype, and it's fully functional but still needs improvement. Step 1: The build surface Create a flexible/removable print surface by cutting a 12 by 24 inch thin sheet of cold rolled steel in half with shears (you'll get two). Cover each half with your preferred build surface. I used PEI on one and blue tape on the other. You can find the necessary materials at a big box home improvement store: https://www.lowes.com/pd/Hillman-12-in-x-2-ft-Cold-Rolled-Weldable-Steel-Sheet-Metal/3050447 This setup provides flexibility for testing different materials. You can clamp these on or use magnets, whichever suits your needs. Step 2: The probe Install the probe mount, insert the inductive probe, and upload the firmware. Unplug the old endstop and wire up your inductive probe according to the pictures. Step 3: Making it work Raise your Z axis a bit, give yourself some room, and carefully test your probe operation. Be prepared to shut down the power if the probe fails to stop the Z travel during testing. All is working if the probe triggers (LED light up) and the Z travel stops as expected when near metal objects (I used an old set of pliers). Now, use the touchscreen to slowly lower your nozzle to the build surface. A thick paper or business card is the correct distance. Adjust your probe in the mount to trigger at that height and tighten it down. Step 4: The Z offset Any z adjustments will occur in the starting Gcode of your slicer. You'll need to dial this in. Here's my starting gcode for reference: G28 ; Home all axis G29 ; Level the bed surface (auto bed level) G92 E0 ; Reset extruder length to zero G1 F200 E1 ; Extrude 1mm at 200mm/min G92 E0 ; Reset extruder length to zero M206 Z 1.5 ; Set Z offset to 1.5mm above print surface BOM: = Inductive probe NPN NO {LJ18A3-8-Z/BZ} or similar (NPN NO gets around the MKS Gen L internal pullup resistor) https://www.aliexpress.com/item/3-Wire-LJ18A3-8-Z-BX-8mm-LW-Approach-Inductive-Proximity-Sensor-NPN-NO-Switch-DC/32843128116.html = Diode 1N5338B is what I used, but according to the internet 1N4148 will also work https://www.microcenter.com/product/392683/1n5338b-51v-5-watt-zener-diode---5-pack = 3 pin connector {male} to build your plug (save your original plug in case you ever want to go back) I used an old servo cable had from a drone https://www.ebay.com/itm/New-RC-Servo-Extension-Cord-Lead-Wire-Receiver-Cable-Male-Female-Connectors/112959837197
With this file you will be able to print Inductive Probe Edition with your 3D printer. Click on the button and save the file on your computer to work, edit or customize your design. You can also find more 3D designs for printers on Inductive Probe Edition.