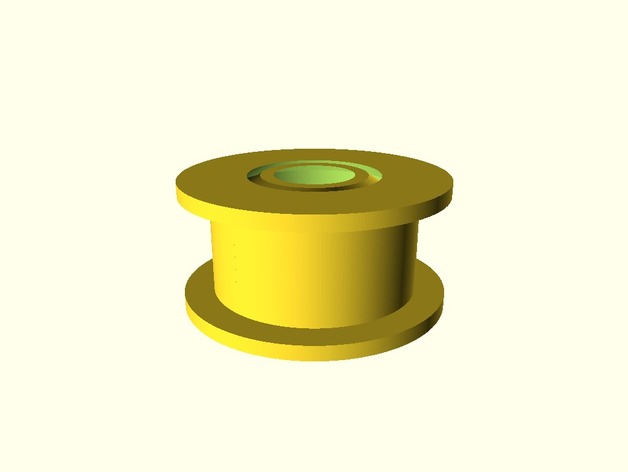
Idler Pulley Bearing, Prints Fully Assembled
thingiverse
This is a fully parameterized all-plastic bearing designed for use as an idler pulley which prints fully assembled. The provided STL file works with GT2 belts, but the OpenSCAD script can be easily adjusted to accommodate other sizes. I created this project to test if it's possible, and I believe it achieves sufficient stability and sturdiness for successful use on a printer. It rolls very smoothly, although it doesn't quite match the rigid stability of a well-machined metal part. A bit of axial wobble is a necessary consequence of leaving enough clearance for the part to print without fusing. The OpenSCAD script attempts to estimate the amount of this wobble based on given parameters. It's crucial to calibrate your printer before printing this bearing, paying particular attention to effective extrusion width and extrusion rate. Errors in calibration can cause the bearing to fuse. The included STL file is for 0.5mm clearance, and there's an additional STL file for a looser bearing with 0.6mm clearance. I obtained similarly shaped metal bearings with rims for $2.20 each, while this fully printed piece requires only about $0.03 worth of plastic. Print Settings: Printer: HICTOP 3DP-11 Rafts: No Supports: No Resolution: 0.5 x/y, 0.2 z, 1.5 perimeter, 1.0 top/bottom Infill: 50% Notes: Calibrate carefully for the resulting line widths after extrusion. Post-Printing: Conditioning the bearing: If it printed slightly fused, you might be able to wiggle it out. If this doesn't work with a little pressure and twisting, then it's unlikely to do so without damaging the bearing. Try a larger clearance or try to better calibrate your printer. Smoothing the inside: 1) Take an M5 bolt with a corresponding nut and tightly clamp them through the bearing. 2) Place the protruding end of the M5 bolt into a drill (use safety goggles and other precautions! If you don't know how to do this safely, don't attempt it). 3) Spin the inside of the bearing while holding the outside stationary. Needle-nose pliers can be used to hold the outside if you prefer not to hold it by hand, but try not to scratch it. 4) Gradually increase the drill speed and ensure it has contacted all parts of the outside evenly at high speed. This should smooth over any minor printing errors inside. 5) Unbolt it and then lubricate the inside of the bearing (you can only lubricate after the drilling step, or the drilling step won't work as well). How I Designed This: I saw many bearing designs that attempted to make bearings by emulating rolling friction or gear designs used with metal, but I think this is the wrong approach. PLA has very smooth sliding friction with circular surfaces rendered with a high polygon count, so this bearing uses this simpler principle.
With this file you will be able to print Idler Pulley Bearing, Prints Fully Assembled with your 3D printer. Click on the button and save the file on your computer to work, edit or customize your design. You can also find more 3D designs for printers on Idler Pulley Bearing, Prints Fully Assembled.