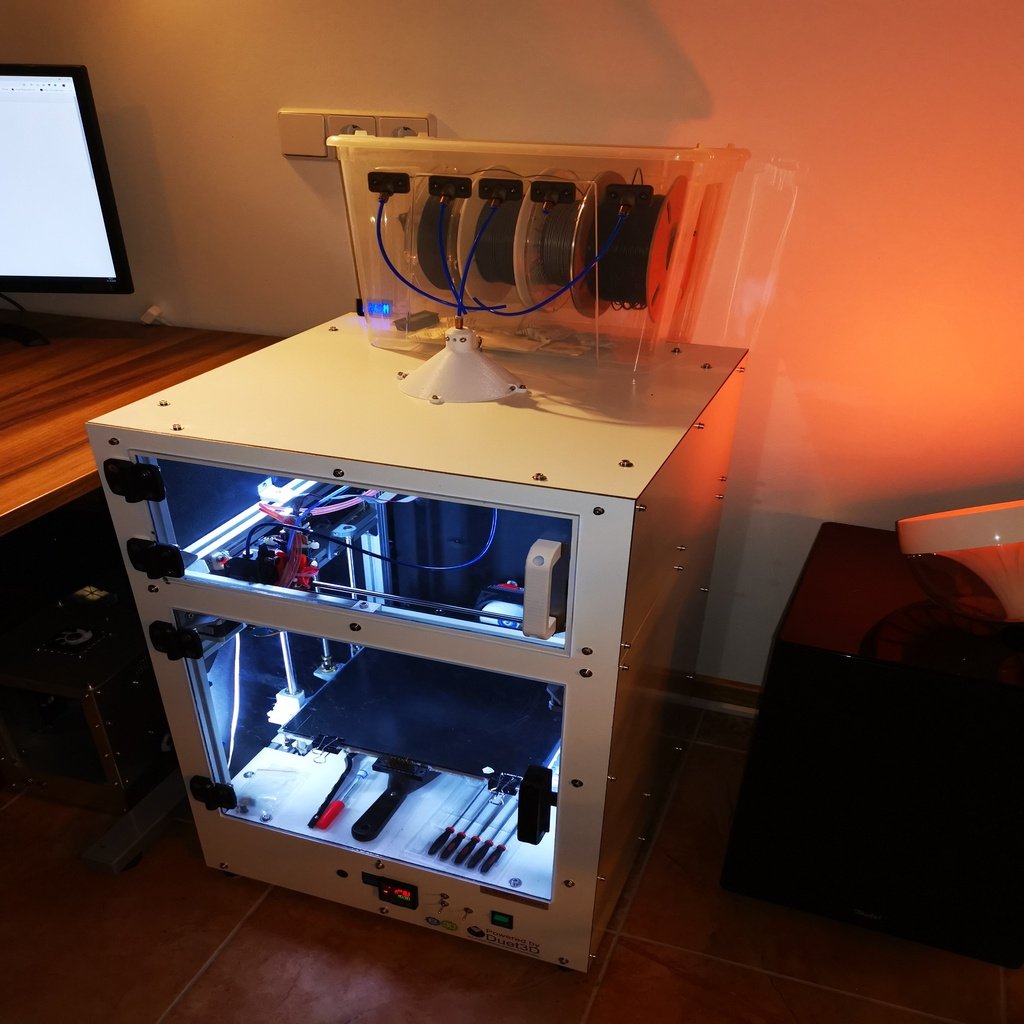
Hypercube Evolution Insulated Enclosure
thingiverse
My design of an insulated enclosure for a standard Hypercube Evolution 3D Printer with a build volume of 300x300x300mm. I've included an extra space for the electronics in the bottom, adding 100mm to the height (Stand extrusion length 600mm). 3D Printed parts: 32 x Distance 10mm (for left and right enclosure plates) 13 x Distance 25mm (for rear enclosure plate) 4 x Distance hinge (for mounting hinges to front plate) 2 x Door handle 2 x Magnet holder Parts needed: - 4 x Multi hinge for 30x30mm extrusion (https://www.ebay.com/itm/Scharnier-Kombischarnier-Kunststoff-30-30-not-hanging-48-x-59-mm-black/251637007543?hash=item3a96bc04b7:g:HxkAAOSwVFlUCOz7) - 4 x Magnet 12x8x2mm - Insulating mat 10mm thickness (https://www.amazon.com/D%C3%A4mmschaummatte-selbstklebend-verschiedenen-Gr%C3%B6%C3%9Fen-1000x500x10mm/dp/B011L30X6K/ref=sr_1_17?ie=UTF8&qid=1531299576&sr=8-17&keywords=d%C3%A4mmschaummatte) - M4 Screws - M6 Screws - M4 Nuts for 30x30 extrusion - M6 Nuts for 30x30 extrusion Enclosure plates: I've used 3mm Alu DiBond plates with a white surface, and the front door is made of 4mm Plexiglas. I've integrated a power switch (Terminal mounting diameter of 28,5x21,5mm) and two switches (Bore diameter 6mm) for switching on/off lighting and fans. Dimensional drawings can be found in the file area in the "Enclosure_cut.pdf". For milling, I've uploaded all frame parts as a .dxf file. Chamber heater: My goal was to create a heated chamber for my HEVO to print ABS, ASA, etc. without warping. The maximum chamber temperature goal was 70°C. To heat up the chamber, I integrated 2 PTC heaters in the bottom plate of the enclosure: https://www.amazon.com/gp/product/B07BK1VQTP/ref=ppx_yo_dt_b_asin_title_o03_s00?ie=UTF8&psc=1. The PTC heaters are controlled by a combination of a separate temperature controller and a heater output from the Duet mainboard. The separate temperature controller is used to limit the PTC heater temperature to 100°C, while the heater output from the Duet mainboard controls the heating process. Design updates: 2018-07-11: Updated distances to fit into the 3030 extrusion together with nuts. Uploaded a new magnet holder type for easier fixing magnets inside. Just put the magnets together with usable glue for your printed material into the printed magnet holder. Uploaded .DXF files for enclosure panels made of 3mm Alu DiBond Uploaded .DXF files for front door and magnetic steel plate mounted at the front door Uploaded .PDF dimension files 2018-07-19: Added an additional cutout in the front panel with 45x45mm for Omron temperature controller for build volume heating. 2019-10-27: Updated design with a top cover made of 3mm Alu Dibond with an integrated filament sensor and exhaust fans in the back. For the top cover, 5 additional 25mm and 10 additional 10mm distances are needed! For the front door, you also need 2 additional hinge distances and 2 additional hinges! Also, a additional door sheet and a door handle is needed! The filament sensor on the top of the cover is made to integrate the Duet laser filament monitor. To route in the filament, you need 2 M5 4mm fittings for example from SMC. For the exhaust fans, you can use fans with mounting hole diameters of 82,5x82,5mm. The additional 12mm hole in the cover backpanel is used for a mounting fitting (SMC KQE04-00) to route in air pressure for component cooling (Berd Air). If you are using water cooling, you may also need 2 more 12mm holes to integrate the same fittings which are used for component cooling, one for water IN and one for water OUT. Design for a integrated HEPA filter actually outstanding!
With this file you will be able to print Hypercube Evolution Insulated Enclosure with your 3D printer. Click on the button and save the file on your computer to work, edit or customize your design. You can also find more 3D designs for printers on Hypercube Evolution Insulated Enclosure.