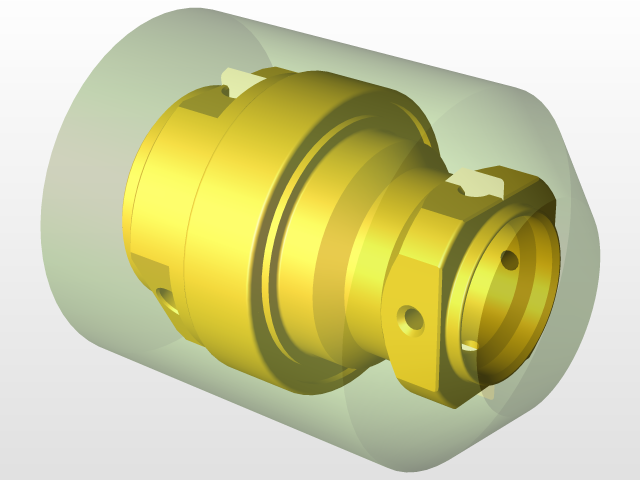
Hydraulic-Sleeve-Body
grabcad
**Setting Up a Simulated Mill-Turn Program: A Step-by-Step Guide** Establishing a simulated mill-turn process involves meticulous planning and implementation to replicate the complex movements of a CNC mill. To ensure success, adhere strictly to these comprehensive instructions. 1. **Choose a Suitable Simulator Software**: Select a reliable and user-friendly software specifically designed for creating simulated machining processes, such as Autodesk Inventor Simulation or Foresight Simulation System. 2. **Design Your Workpiece with CAD/CAE Software**: Use Computer-Aided Design (CAD) and/or Computer-Aided Engineering (CAE) tools to accurately model the part that requires simulation. This stage is crucial for generating an accurate simulation of the milling process. 3. **Define the Machine's Capabilities**: Specify the milling machine's capabilities, including its speed, power output, tooling configuration, and the material it will work with. This data is vital in determining realistic simulative conditions. 4. **Setup Machining Operations**: Configure machining operations such as facing, drilling, boring, and turning into the simulator. These tasks simulate real-world scenarios, offering insights into performance and optimization potential. 5. **Input Geometric Tolerances and Surface Roughness Specifications**: Define critical tolerance specifications and surface roughness values for simulated tool interactions with your part model, which are instrumental in evaluating performance at these microscopic levels. 6. **Implement Realistic Conditions**: Include realistic variables such as material properties, clamping strategies, vibration sensitivity, temperature changes, and lubrication factors into the simulation model to produce results as closely resembling real-world behavior as possible. 7. **Optimize Machining Strategies for Maximum Efficiency**: Apply iterative testing in a controlled simulation environment with your chosen program or set of rules designed around your project specifications to achieve improved productivity, faster processing time, increased accuracy without trial-and-error in real-time experimentation. This meticulously followed process can help establish reliable simulation programs with accurate replication. Through rigorous testing under conditions accurately matching operational scenarios and adjusting settings for improvement in both speed and performance quality within the constraints posed by physical limitations.
With this file you will be able to print Hydraulic-Sleeve-Body with your 3D printer. Click on the button and save the file on your computer to work, edit or customize your design. You can also find more 3D designs for printers on Hydraulic-Sleeve-Body.