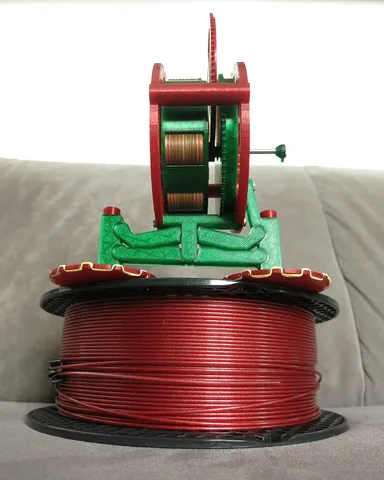
Hinged parallelogram for Gyroman 4
prusaprinters
I am very impressed by the Gyroman concept, and wanted to build one. But I was too lazy to assemble the two legs, four horizontal bars, and link part with 16 screws, so I made this version which replaces all that with a single printed part.This was also a way to demonstrate the use of the hinge library that I published some time ago, which provides customizable, vertically printed hinges.Printing and assemblyYou will need the following modified parts :1 parallelogram part2 side_for_hinges parts2 foot_with_shaft and 2 foot_nut partsPrint the parallelogram with 0.15 layer height, slowly, preferably in PLA (I used PETG but it's easier to avoid stringing and other defects with PLA, and it will be more stiff). It make require some force to loosen the hinges once printed, but then it should move quite smoothly.You will also need the original model's other parts, but you should omit the legs, bars, link, feet, and sides.The assembly proceeds as for the original model. The bottom of the sides_for_hinges parts is only connected to the parallelogram part, by mean of two M3x8 screws. The right screw must be inserted through the hole in the parallelogram's link, and it's head must be small enough (≤5mm diameter). The right leg's top hinge also has a small hole to avoid forcing on the screw head when raised completely (I didn't realize this minor issue before printing, I added the hole in the published model).No bearings optionI was also too lazy to buy some 623 bearings, so I printed them… using the provided models “bearing” and “link_bearing”. Or rather, they should be called bushings. Printed in PETG, after sanding (with a 3mm drill bit) and with a bit of oil, it kind of works, though it's not as efficient as ball bearings. The friction is especially noticeable when pulling the string, because its wrapped directly on the shaft, so the load put on the bearing will be very high with respect to the torque during this step. Maybe adding a collar to increase the string wrapping diameter would help.About the designThis was designed in OpenSCAD with the above mentioned hinge library that I already used for other purposes. I would have hoped that this would be a straightforward application of the library, but it was a bit more complicated. First, I discovered some bugs in the library, so I made an update to fix those. Second, this hinge library only provides symmetric hinges, where the leaves are a mirror image of each other, which doesn't apply here. So I had to twist the functionality, using the low-level interface. It took some work, but the result remains reasonably readable.I mostly kept the same dimensions as in the original model (leg spacing, bar spacing…) One minor difference is that the link's hinge is the same as the right leg's hing (not enough space for two hinges), so it's slightly more distant from the center, and as a result, the foot amplitude will be unnoticeably smaller. Keeping the same dimension ensured that it would work the same, but made the parallelogram more subtle due to the need to avoid the body.Next stepI also feel too lazy to pull a string just to watch the guy walk a few steps… How about an electric powered version ?
With this file you will be able to print Hinged parallelogram for Gyroman 4 with your 3D printer. Click on the button and save the file on your computer to work, edit or customize your design. You can also find more 3D designs for printers on Hinged parallelogram for Gyroman 4.