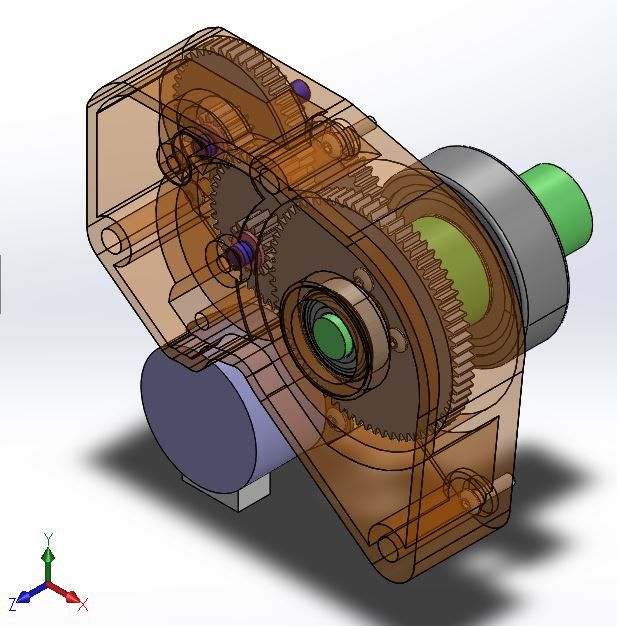
Grundfos Gearbox by SEGEV
grabcad
Motor input for the system is 500 RPM with torque of 43 mNm. A PDF file containing graph and calculation to explain the output for the main shaft has been attached. With a ratio of approximately 479.9, we achieve an output shaft speed of 1.04 RPM and torque of 20.6 mNm. Additional information about materials and design can be found in the attached PDF. A radial force of 300 N is applied to the system with no axial force present. Upon simplifying a free body diagram calculation, suitable sealed bearings for the output shaft have been identified. The gear train is designed to rotate on the shaft, with all chosen materials listed in the PDF along with reasons for their selection. Gears are constructed from POM, shafts from steel, and sliding bearings made from PTFE/TEFLON. A poly-carbonate cover completes the assembly. The system's components are assembled only in the Z direction, aside from set-screws securing the gear to the motor. The gear train and motor with all components fit within allowed space requirements. However, due to the allowance to modify the enclosure box inner surface, ribs have been extended throughout but do not encroach upon the gear train, bearings, shafts, etc., which remain within designated space. Ribs are primarily designed to transfer and/or distribute forces, mainly from the outer shaft (300 N) and gear train to the box. Each BOSS feature equipped with an M3 screw will incorporate an M3 insert – not visible in the CAD file. Hysteresis is less than 3 degrees based on a case study employing a simplified static case that considers radial force, radial force on bearings, and 20 Nm on the shaft.
With this file you will be able to print Grundfos Gearbox by SEGEV with your 3D printer. Click on the button and save the file on your computer to work, edit or customize your design. You can also find more 3D designs for printers on Grundfos Gearbox by SEGEV.