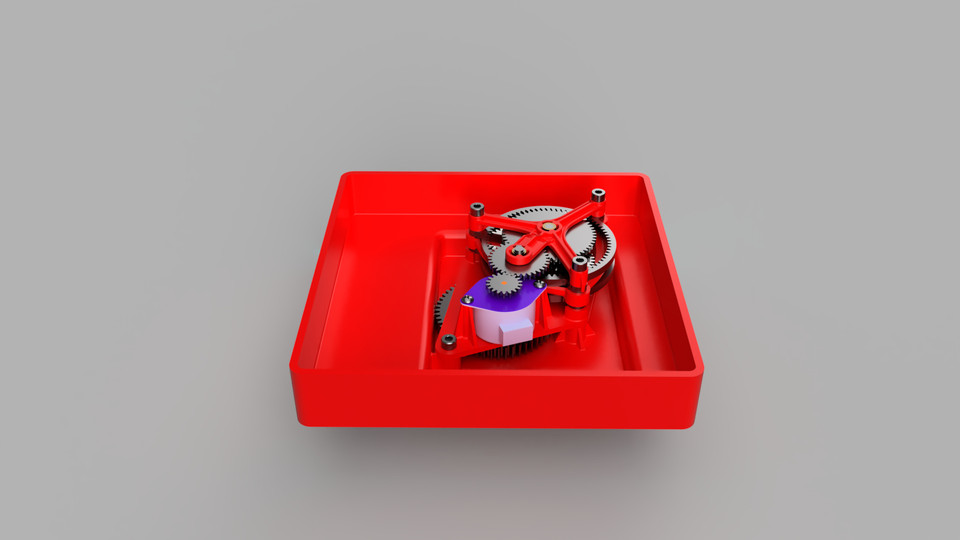
Grundfos challenge gearbox
grabcad
This is my take on the Grundfos challenge gearbox. The output torque and speed should remain in spec even when operating the motor at approximately 550 rpm, assuming a gear efficiency of 97%. Adjustments may be necessary to reflect actual efficiency levels determined through testing. Most structural parts are injection molded using the same material as for the box, which can help reduce production costs associated with operating multiple production lines. The planetary gearboxes require metal construction to mate seamlessly with sun gear axles. Rotational constraints are largely handled by oil-embedded bronze bushings, eliminating the need for lubrication. The gears themselves can be crafted from either steel or phosphor bronze, further minimizing the requirement for lubrication. Shafts should be fashioned from suitable tool steel. Standard mounting hardware is also utilized in the construction process. Precision-requiring components are designed with self-alignment in mind to ensure optimal performance. Plastic parts are optimized for injection molding using simple two-piece molds, except for the original surfaces of the enclosure box, which were left unchanged. Unfortunately, my design does not entirely conform to the specified design space envelope. As I progressed in the design process, miniaturization would have necessitated substantial changes that I did not have time to implement.
With this file you will be able to print Grundfos challenge gearbox with your 3D printer. Click on the button and save the file on your computer to work, edit or customize your design. You can also find more 3D designs for printers on Grundfos challenge gearbox.