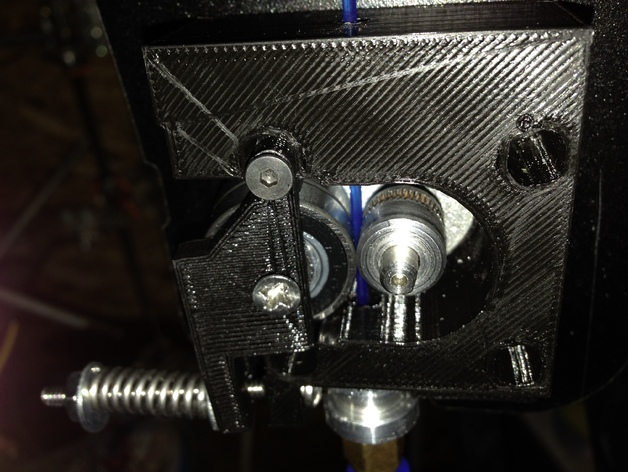
gripstruder 4x the grip force, in many cases this means extruding prints at over 800mm/m of 1.75mm feedstock
thingiverse
The Gripstruder is renowned for its exceptional grip on feedstock material. A recent addition of file xt5.stl has been incorporated to tackle prolonged use fatigue while unifying the lever, pulley arm, and motor. For optimal results, it's advisable to manufacture the arm portion from ABS, as the arm experiences significant stress due to the cycling motion induced by heat from the motor. Other parts can be made of PLA, although the arm is more susceptible to wear from heat. The hinge of the mechanism is attached to the motor, while other sections are not under load-inducing heat conditions. A video demonstration of this design is available on YouTube (link provided). Additionally, a part called 'mount_withbolton' has been uploaded as an update, featuring bolt holes that fit seamlessly onto Seemecnc mount plates. The Gripstruder requires two 608 bearings, a 2-inch 6/32 bolt, two washers, a high compression spring, and a 3mm flat bolt of approximately 6mm in length. A flat head 6/32 1-inch long Phillips bolt is also necessary. This design was inspired by the need for faster printing with a Rostock Max Delta bot and offers four times the surface area for feedstock grip compared to conventional extruder pinch grips. The pressure between two 608 bearings ensures a strong hold on the feedstock, and the R2ZZ bearing is twice as large as standard bearings, offering increased contact surface and improved force application. This design has been tested at flow rates of up to 800mm/m. To assemble the Gripstruder, push two 608 bearings onto the bottom part of the idler. The built-in groove allows the outside of the bearing to rotate freely. Attach the top idler part and thread a flat head 3mm or 6/32 screw through both parts. Next, insert a 3mm flat heat bolt into the round part of the idler, ensuring a tight fit with minimal play. Mount the big idler block onto a motor and secure it using an 8mm gear hobbled mount on the motor shaft. Feedstock should be threaded through and positioned appropriately before attaching the idler arm to the motor's screw hole with a bolt, washer, high compression spring, and nut. Keep everything loose for now. Finally, attach the Seemecnc metal mount to the bowden extruder using pliers, ensuring that the holes are unobstructed and feedstock can move freely without buckling. Images of the assembly process will be updated shortly. Enjoy!
With this file you will be able to print gripstruder 4x the grip force, in many cases this means extruding prints at over 800mm/m of 1.75mm feedstock with your 3D printer. Click on the button and save the file on your computer to work, edit or customize your design. You can also find more 3D designs for printers on gripstruder 4x the grip force, in many cases this means extruding prints at over 800mm/m of 1.75mm feedstock.