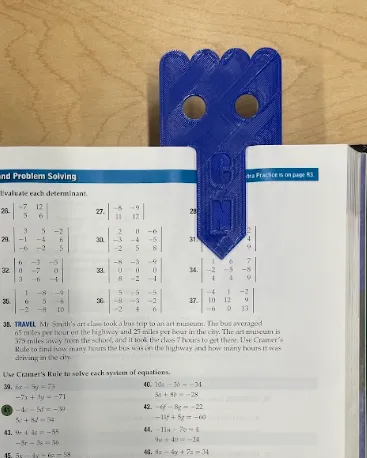
Ghost Clip
prusaprinters
Summary Section (Continued): This 6x13x0.15cm ghost will surely add personality to your office supply collection, and with zero assembly required, it is a short and easy print! Add your own flair to this fun project with custom-engraved initials! I worked with Elana Wald on this project; you can find her clip version here (add link). Objective:With a partner, you will recreate your ghost clip using Solidworks. You and your partner MUST have identical files that you create by collaborating on each step, one at a time.Assembly/Construction Instructions Section:CONSTRAINT BOXDraw a 6x13 center rectangle with the “from midpoints” option selected, centered at the originTEETHDraw a construction line (Construction 2) 1cm above the bottom of the constraint boxDraw a construction line (Construction 3) 1cm from the left of the constraint boxDraw a construction line (Construction 4) 2cm from the left of the constraint boxDraw a right isosceles triangle (Triangle 1) 1cm tall with a 2cm base at the bottom of the figureDraw a line between the intersection of the left of the constraint box and Construction 2 and the intersection of Construction 3 and the bottom of the constraint boxDraw a line between the intersection Construction 3 and the bottom of the constraint box and the intersection of Construction 4 and Construction 2Set the two lines to perpendicularComplete step 5 two more times, with each new triangle connected to the last one’s baseBUMPSDraw a construction line 0.75cm below the top of the constraint boxDraw a construction line 0.75cm from the left of the constraint boxUse the arc tool to create a semicircle with a radius of 0.75cm at the topCreate three more semicircles with the equal relation going across the remainder of the topSIDESDraw one vertical line connecting the top left point of the triangles and the bottom left point of the humps and another connecting the top right point of the triangles and the bottom right point of the humps.EYESDraw a horizontal construction line 2.8cm from the top of the constraint boxDraw a vertical construction line 1.7cm from the right of the constraint box At the intersection of the two construction lines, create a circle with a 1.2cm diameterUse the mirror tool to reflect the eye over the centerlineMOUTHDraw a horizontal construction line (Construction 5) 3.55cm from the bottom of the constraint boxDraw a vertical construction line (Construction 6) 1.25cm from the right of the constraint boxAt the intersection of Construction 5 and 6, draw a vertical line (Line 1) 4.45cm longDraw a horizontal construction line (Construction 1) 1.8cm from the bottom of the constraint boxDraw a line (Line 2) from the bottom of Line 1 to the intersection of Construction 1 and the centerlineUse the mirror tool to reflect lines 1 and 2 across the centerlineSelect the mouth outline and offset it 0.5cm inwards, capping the endsEXTRUSIONExit the sketchUse the “Extrude Boss” tool to extrude the ghost by 0.15cmENGRAVINGCreate a new sketch on the ghost’s top faceDraw a horizontal construction line from the left side of the inside of the ghost’s mouth to the right side.Use the text tool to type your initial on the line, with a size of 1.50cm and center-alignedRepeat steps 26-27 with your last initial below the first initialUse the “Extruded Cut” tool to engrave the initials 0.075cm Design Choices:NOTE: The original paper sketch does not include all sketch relations labeled; however, the corresponding planning document did.As the assignment was to copy the ghost, Elana and I decided to create a sketch of the source ghost before bringing it into Solidworks. Using a ruler, we measured each element of the ghost and copied it onto a piece of graph paper, being sure to write down all the dimensions. We then took our sketch and used it to create a plan for what we would do to replicate it in Solidworks, using all the same dimensions. However, we encountered several challenges and realizations that resulted in numerous changes to the original plan. When we originally wrote the plan, we planned to use guidelines to create the triangles on the bottom of the clip and then set certain lines to be perpendicular and equal to each other (note that the parallel relations on the paper sketch that are shown would have the same result as a perpendicular relation). However, after creating the triangles with the guidelines, when the relations were applied the sketch became over-defined. This was because the guidelines already created an environment in which the lines were fully defined, so no further relations were necessary. The second change to the original plan was to change the relations being used for the semicircles. Our plan was similar to the triangles, where we would draw one figure using guidelines and then set the rest of the semicircles to be equal. However, we realized that the second semicircle automatically used the centerline as a guideline, so the equal relation was only necessary for the two rightmost semicircles. When measuring the dimensions for the mouth in the original paper sketch, the rulers we used only had an accuracy of 1mm, which can result in a low accuracy in the measurements. Specifically, the mouth utilizes inexact measurements, and inconsistencies in source models from the 3D printing process made it difficult to gain a good measurement. On the sketch, we measured the mouth to be 1.20cm from the side of the constraint box and offset 0.5cm inwards. When we sketched the mouth with these dimensions in Solidworks, the dimensions were off when holding the source ghost up to the screen and comparing. Therefore, we changed the mouth to be 1.25cm from the side of the constraint box and offset 0.55cm inwards. However, after printing a version with these measurements, it became apparent that the mouth was too narrow, the clip went too low, and the mouth was too far inwards from the side. The only measurement that seemed to line up was the inner part of the mouth, whose vertical lines were perfectly aligned with those of our print. To make the mouth wider while keeping the inside lines stationary, we moved the outer lines 0.05cm closer to the side of the constraint box while increasing the offset from 0.55cm to 0.6cm. This also helped to move the tip of the clip upwards, as the extra 0.05cm pushed it up. Our original plan was to have the side of the mouth be 4.50cm long and 3.50cm up from the bottom of the constraint box. However, after printing the first version with these measurements it became apparent that the diagonal lines in the mouth were too horizontal. To fix this, we moved the corners slightly upwards, by 0.05cm. To compensate for this, we had to change the height of the mouth to 4.45 cm as the top had lined up vertically in the first print.
With this file you will be able to print Ghost Clip with your 3D printer. Click on the button and save the file on your computer to work, edit or customize your design. You can also find more 3D designs for printers on Ghost Clip.