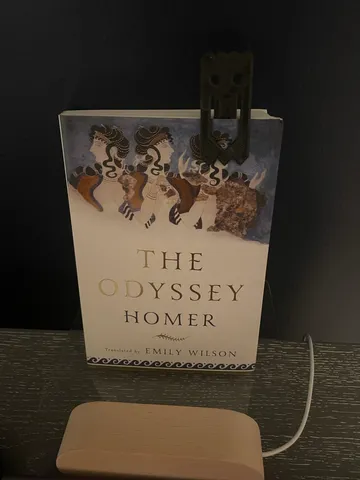
Ghost Clip by Omar
prusaprinters
Summary:Get ready for the spooky season with a mini ghost clip, useful for clipping together small quantities of paper, closing bags, or bookmarking your place in a book! Has a tight clipping portion, so it is not suggested to fit in too many papers, however, they will be held tightly together. Made with my partner Kevin Lu. Assignment:Create a ghost clip in Solidworks based off of a real life model ghost. The ghost clip must be made with both accuracy and precision, and it is also required to look the same as your partner’s printed ghost. Assembly Instructions:REMINDER: You can smart dimension all the measurements after creating the shape/object described in each step; just make sure that it is close to the distance named in each step. Also be sure to not accidentally create any automatic relations unless explicitly mentioned to do so.Draw constraint box Center rectangle on the origin, with construction lines that go through the midpoints of the rectangle30mm x 65mmSet the top and bottom lines of the constraint rectangle as construction linesPlot anchor points (AP) on both sides of the rectanglePlot points from top corners working towards bottom corners3.75mm (on diameter of arcs on the top of the ghost)11mm (runs through the center of the eyes)10mm (tangent to the top of the arc on top of smile)9mm (middle of constraint box)13mm (runs through POI of outer lines of smile)12.75mm (runs through base of the triangle)The last anchor point is the dot on the bottom corner of the constraint boxAfter plotting anchor points draw horizontal centerlines between corresponding anchor pointsSet the line between AP(vi) and the bottom of the constraint box as a construction line, on both sides of the box.Draw semicircles on top of the ghost (only need 2, mirror the other half)Draw centerpoint arc with diameter 7.5mmFirst click should be on AP(i)Second click should be on centerline (i), 7.5mm awayTop of the arc should be on the top line of the constraint boxDraw a second centerpoint arc with diameter 7.5mmFirst click should be on the end of the first centerpoint arcSecond click should be 7.5mm awayTop of the arc should be on the top of constraint boxMirror semicircles 1 & 2 across the centerline at the middle of the constraint boxDraw eyes on the ghost (only need one, mirror the other)Plot point 5.5mm away from AP(ii) on centerline(ii)Draw a center circle with center 3mm away from the previous point, with the second click on the point we just plottedUse the mirror tool to mirror the eye across the centerline at the middle of the constraint boxDraw triangles on the bottom of the Ghost (do not mirror here)Plot 6 points 5mm away from each other on centerline (vi), starting from AP(vi) until you reach the edges of the constraint boxDraw vertical centerlines with 5mm length on every other point (first point, third point, and 5th point after AP(vi))Draw diagonal lines connecting points on centerline (vi) and the vertical centerlines in a zigzag patternDraw outer smile (can mirror other side and then offset)Measure and plot a point 8.75mm up from the bottom vertex of the middle triangle, on the centerline of the middle of the constraint boxDraw a second point on centerline(v) and set it to be coincident with the outermost point on the circle of the eyesConnect the two points with a lineFrom the point on centerline(v) draw a 22mm vertical line (should go from centerline(v) to centerline(iii)Use the offset tool to highlight everything made in this step, and offset the lines by 3mm with the ‘cap ends’ option checked yesUse mirror tool: highlight everything created in this section, and mirror across centerline in the middle of the constraint box Design process: My partner and I first started off by sketching a model ghost on paper.The sketch on paper was drawn twice as large as the model ghost since the model ghost measurements could be slightly off. Since we made it larger, it also made it much easier to understand what dimensions went where and where we should specifically put each dimension.By initially drawing the constraint box, we were able to keep the area of the ghost down to a specific area. We then measured every dimension from the middle of each arc, circle, curve, or intersection of lines and placed anchor points and important construction lines at those points. For triangles, we also decided to not measure the length of the hypotenuse but rather measure the height and width of the imaginary triangle, to make it more defined in Solidworks when we would eventually sketch and make the 3D model. Our final and most crucial decision was to mirror each individual component instead of the entire ghost in case we accidentally duplicated unnecessary parts that could cause the program to crash.At first, when sketching our ghost, we followed our assembly instructions to the letter. However, we encountered our first problem when drawing the semicircles on top of the ghost.Our initial instructions said to draw center circles, and then trim the bottom to make the semicircular bumps on top of the ghost. While this worked in theory, when we attempted to replicate it in Solidworks, it did not work and nearly crashed our application. We then decided to revise our instructions to draw the semi-circles with a center point arc. This worked much better, and we encountered no issues when drawing or mirroring them. Our second big challenge was when mirroring some other elements of our ghost, especially the eyes. When mirroring the eyes, our screens suddenly turned yellow, indicating that something was overdefining the sketch, which could potentially crash the program. After we looked into it, we realized that we had accidentally mirrored a series of smart dimensions as well, which was causing the sketch to overdefine. To solve this problem, we just had to delete the extra smart dimensions and unnecessary extra lines or points mirrored. We also had to be careful later when mirroring, so we kept this in mind when moving on.Our last challenge was to make the ghost look as similar as possible to the model ghost. We knew at the beginning that our measurements had a small margin of error, so we had to compare the size of the model ghost to the sketch multiple times. We spent almost two full classes trying to match the length, width, and size of each individual component to the model ghost. Since there was no way to perfectly measure the dimensions of the ghost without the actual sketch, we had to judge the size with only our eyes. We changed almost everything about the ghost, including the total width, the thickness of the smile, the distance between the smile and the bottom of the ghost, and we also adjusted the placement of multiple anchor points as well.
With this file you will be able to print Ghost Clip by Omar with your 3D printer. Click on the button and save the file on your computer to work, edit or customize your design. You can also find more 3D designs for printers on Ghost Clip by Omar.