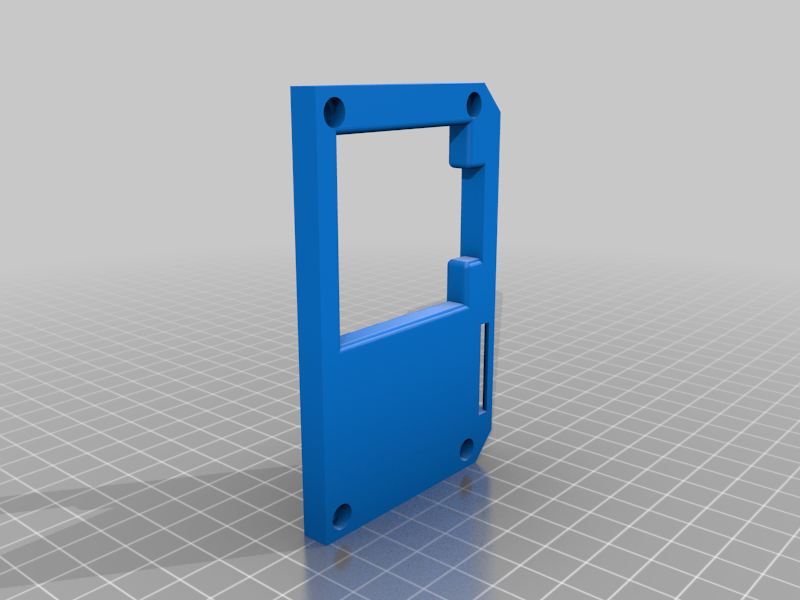
FolgerTech FT-5 Upgraded X-Carriage (piezo bed level option)
prusaprinters
<p>Update 11/15: Switched to a BMG vlone and added a compatible part cooler blower channel for BMG+V6+Volcano. Piezo leveling is still working great and I have switched back and forth between the Aero and BMG with almost no adjustment.</p> <p>Update 4/8: I received my Aero upgrade kit and converted over. The piezo leveling is still working just fine. The Aero and stock extruder require less Z correction than the full E3D v6 but other than that, nothing else needed to change.</p> <p>Since the Aero and stock extruder are so much shorter I added a new part cooler that mounts a blower behind the carriage - should work for stock extruder or aero with a volcano.</p> <p>Update 3/21: Added a version that supports piezo-based bed leveling for anything that mounts to a full size stepper motor. This is very much WIP but it is working for me at the moment. Here's how it works... You'll want to mount a 27mm piezo disk in the recess in the back of the carriage. The recess ridge should support the brass edges of the disc and the center sensor should be facing toward the FRONT of the carriage. A spot of glue on the brass can hold it in place however it will be pressure-held in the recess so I did not find it necessary. The current design has a channel that would indicate the disc could go in the with the sensor facing the back of the carriage however this negatively impacts sensitivity and will not work well. You can glue the wires in the channel to keep them out of the way if you wish.</p> <p>Next, the 'Piezo Knocker' should be positioned so that the screw holes align with the bottom screws of the NEMA motor. The longer 'knocker' end should face the piezo disk and the larger, flatter end should face the motor. Position the motor and tighten the screws fully - they don't need to be overly tight. Do NOT put in the top screws. The idea is the front of the motor should flex vertically when the nozzle touches the bed pushing on the knocker and flexing the disk. There is also an updated carriage front plate with a little more room for the motor in order to allow for the flex. The knocker is larger than the gap+piezo disk recess so there is some pre-loaded pressure on the disk giving pretty repeatable results as well as holding the motor firmly enough to prevent any negative impacts on print quality. Once you get everything assembled you'll want to tune the vrefs on the board: <a href="https://www.youtube.com/watch?v=WDHU3tRU-C4">https://www.youtube.com/watch?v=WDHU3tRU-C4</a></p> <p>I'm currently using the piezo as an end stop replacement as things seem to get wonky with the auto bed leveling. I believe that is a tuning/PEBKAC issue and not a design issue though. Here it is performing the bed leveling process: <a href="https://youtu.be/MD5Hin9Ter8">https://youtu.be/MD5Hin9Ter8</a>.</p> <p>To make this work I made the following changes to the firmware:</p> <p>In configuration.h:</p> <ul> <li>uncomment #define AUTO_BED_LEVELING_FEATURE -- this will let you use the grid leveling if you wish. You'll want to tweak LEFT/RIGHT/FRONT/BACK_PROBE_BED_POSITION. I used 20 for LEFT/FRONT and 220 for RIGHT/BACK. You can set AUTO_BED_LEVELING_GRID_POINTS as well. 3 seems to be common.</li> <li>set the X/Y/Z_PROBE_OFFSET_FROM_EXTRUDER to zero. The nozzle is the probe so no offset needed. We will need to adjust the z offset from home via GCODE as there is a small amount of flex required to trigger the sensor and left uncorrected the nozzle will be pressed against the bed for the first layer. However, that requires some tinkering and I do it through the start gcode instead of here.</li> <li>Increase the Z homing feed rate. By default it's #define HOMING_FEEDRATE {50<em>60, 50</em>60, 10<em>60, 0}. I increased to #define HOMING_FEEDRATE {50</em>60, 50<em>60, 20</em>60, 0}. The nozzle impacting the bed is the piezo trigger. We don't want to be gentle.</li> <li>Along the same lines, we don't want the 2nd bump to be too gentle. I increased the bump divisor from #define HOMING_BUMP_DIVISOR {2, 2, 4} to #define HOMING_BUMP_DIVISOR {2, 2, 1}.</li> </ul> <p>Then, in the start GCODE I did a couple things:</p> <ul> <li>First I X/Y home the nozzle - this is required for any movements:</li> </ul> <p>G28 X0 Y0</p> <ul> <li>Then I move the nozzle to the middle of the plate - I want to z home at plate center in case there are minor balance variations:</li> </ul> <p>G1 X150 Y150 F5000</p> <ul> <li>I heat the nozzle to 180 to soften any material on the nozzle. Anything crusty will press on the plate and throw off the sensor (update: I have upped this to 210 as some PETG is still stiff at 180):</li> </ul> <p>M109 S210</p> <ul> <li>I home the Z. Make sure to clean up any goo that drops:</li> </ul> <p>G28 Z0</p> <ul> <li>I set a Z offset - this is a bit of trial and error based on the amount of preloaded pressure you have on the disk. If it's more than a couple 1/10s of a mm then recheck your sensitivity and setup:</li> </ul> <p>G92 Z-0.1</p> <ul> <li>Then I move everything back to home:</li> </ul> <p>G1 X0 Y0 Z0 F5000</p> <p>I've printed a dozen or so prints with the above z homing logic and even swapped out throats without having to change anything wrt z height. I have a pancake stepper on the way and I plan on making a compatible version.</p> <p>Update 3/11: Added a bottom piece that accessories can be mounted to as well as an attachment for a 50mm blower targeted for a Volcano. I also have a beta for a regular V6 heater block if anyone wants to try it.</p> <p>This is the modified X-Carriage I have been using on my FT-5. This carriage fixes a number of inconveniences us FT-5 users endure. The differences between this upgraded carriage and the original (<a href="https://www.thingiverse.com/thing:1858771">https://www.thingiverse.com/thing:1858771</a>) are:</p> <ul> <li>Solid pieces: The rail and motor attach to the same piece. The screws are fully backed - shouldn't bend or break like the default carriage. The attachment holes have divots to ensure everything stays in place and not the straight, tight square holes. All bolt heads and nuts are counter sunk.</li> <li>Mount for a small 8-circuit terminal block (https://www.amazon.com/Blue-Sea-Systems-Circuit-Terminal/dp/B000S5Q2VS): I change my hot ends, coolers, thermistors, etc often. A terminal block is a lot easier to deal with than crimping every new wire.</li> <li>Cut out for motor plug: You can remove the motor without having to disassemble the entire carriage. Remove the rear motor screws and it will pull out the front.</li> </ul> <p>I dropped the cable chain but the stock chain should mount to the top holes. I velcroed my cable rope to the rail 'hat' from my dual bowden gantry (<a href="https://www.thingiverse.com/thing:2814954">https://www.thingiverse.com/thing:2814954</a>).</p> <p>This is still WIP. Everything works great but I will be creating a part cooler that mounts to the carriage and a piezo sensor mount once the parts arrive.</p> <h3>Print Settings</h3> <p><strong>Printer:</strong></p> <p>FT-5</p> <p><strong>Infill:</strong></p> <p>25</p> <p><strong>Notes:</strong></p> <p>Everything should print pretty easily. Use supports to keep the divots and counter sunk holes well-formed. Use decent infill for structure.</p> Category: 3D Printing
With this file you will be able to print FolgerTech FT-5 Upgraded X-Carriage (piezo bed level option) with your 3D printer. Click on the button and save the file on your computer to work, edit or customize your design. You can also find more 3D designs for printers on FolgerTech FT-5 Upgraded X-Carriage (piezo bed level option).