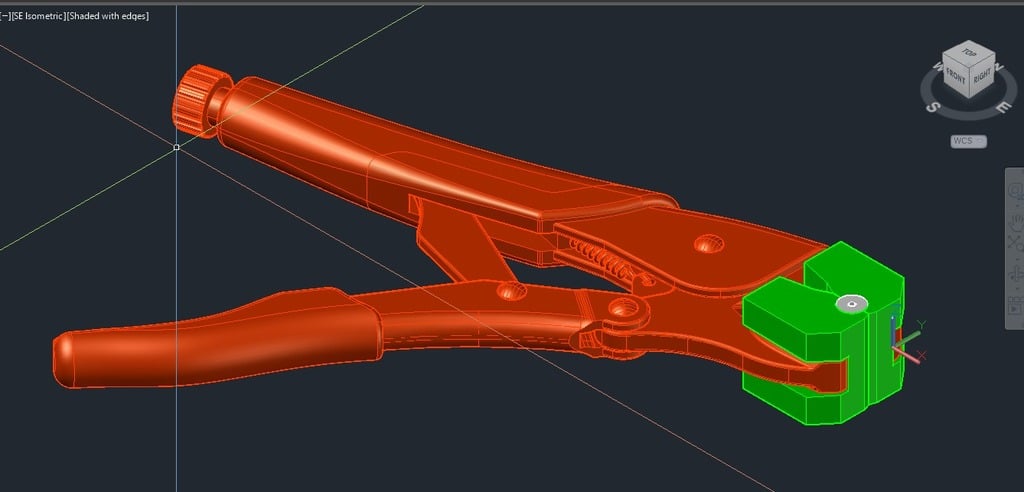
Filament Splicer
thingiverse
Cutting guide, holding jig and forming dies for filament splicing used ~25mm of oversize 1/4" PTFE tube, 1/16" ID. Drill out with #50 or #51 drill bit AFTER it's all put together. Drill bits in order of size: Number 51 - 0.0670 inch 1,75 mm = 0.0689 inch Number 50 - 0.0700 inch McMaster-Carr Part Number 8547K17 is used. As of this writing, their catalog page appears to be changing suppliers. Generic PTFE is just fine. The tube outer surface is roughed up with a coarse Dremel and sanding drum, then flame oxidized to bond with JB Weld to a pair of 3d printed jaw liners. Glue tube to the liners and liners to the Vise-Grips at the same time. A couple people have messaged me asking what 'flame oxidizing' is - this is a good introduction: https://theepoxyexperts.com/flame-treatment-plastic-substrates-adhesive-bonding/ There is enough material in the tube that you could put a few dimples on the tube to engage and key into the glue. I have found the flame oxidized bonding surface to be okay. V2.0: Renamed the jaw liners to 7" Vice-Grip, added jaw liners for ~5" Import/Dollar Store size clamping pliers, added files with hexagon bores for no support printing for hinges, and added chamfer to support the hinge pin bosses. Use jaw clamping pressure to hold it all together and set the approximate tension. Do your best not to overfill the joint - it will close up the intentional gap between jaw liners that serves as a cutting guide. Once the glue has set, run a razor blade between the jaw liners to separate the tube. Do your best to cut across a complete diameter - otherwise you may have to relieve the bore to accept the filament. Then open the jaws and clean things out a bit or excess glue. Then close it up and lock the jaw shut. Now drill it with the No. 50 bit. Try the fit on a piece of filament. If its too tight, go to a No. 51. Holding jig remixed to utilize hex shapes bores and filament holding slots to avoid printing with supports and achieve better tolerances. Screw the guide bottom plate to a board. Use a piece of 3/16" dowel or short dowel pins for the hinge pins. Heat the skived ends of the filament with a lighter / mini-torch. Clamp with the forming jig to align and form to size. If there is a bit of excess molten filament, it will ooze out and form a couple of wings at the PTFE tube joint. Its usually paper thin and cuts off with a razor blade really easy.
With this file you will be able to print Filament Splicer with your 3D printer. Click on the button and save the file on your computer to work, edit or customize your design. You can also find more 3D designs for printers on Filament Splicer.