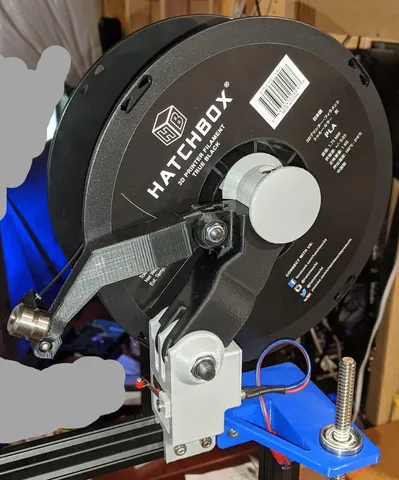
Filament Sensor Spool Holder
prusaprinters
Sorry for my poor writing, engineer, not an english major. lol. Intro: After seeing YaaJ's (https://www.thingiverse.com/YaaJ/about) initial Design for the Smart Spool Holder (https://www.thingiverse.com/thing:3383638) I had so many ideas and this a product of that, so credit to YaaJ for the base idea. I didn't list this a remix, because I did this as a ground up design and started from scratch. Challenges: The idea here is simple, solve filament shorts in a more complete way then just a simple senors attached to some tubing that doesn't catch all shorts. This design will catch both filament running out when still attached the spool and when it lets go of the spool. Mounting it. Everyone has different needs when it comes to mounting a spool holder. This design while some what limited allows for easy creation of different mounting options with different bases. I've included the 3 I've made to start and this entire design is easily mirrored in your slicer if you need the opposite hand. Two are designed to mount to 20mm extrusion (left and right) and the other is a flat base that MUST BE SCREWED DOWN or it will not work. There are 3 different plates for the flat base. 1 is for M5 flat heads, the other is for wood screws with 5mm through holes, and the last is a step file with just the M5s required for attaching it to the base so people can make their own pattern for mounting if need be. Printing. The goal was as easy as possible. While it may not come out perfect without a layer cooling fan or other upgrades. It's designed to require no support and maximum bed adhesion given the surface area available. Design Notes: All holes are designed on size, so for example a 4mm hole is modeled as 4mm. This makes it easy for me to make both a clearance hole and a hole to thread into since all of my hole always come out a fair bit small. I use a cheap set of reamers to clean out holes I need to be clearance (see tool list below) instead of trying to size things separate. Assuming your first layer mushrooms like mine does, you will likely need/want to clean up the edges attached to the build plate with a deburring tool or file since some parts are designed with a fairly close fit. Most note ably the front switch holder. The weight of the arm is the biggest problem I ran into with this design, thus why there is a 10g weight in the hardware list, this helps prevent the arm from not tripping the front switch if it doesn't drop from high enough. I ended up using 2 of the 10g weights for a little extra insurance. The swivel head arm is intended to allow the spool to feed smoother through the arm at different angles. This is still a work in progress and I'm printing my first one right now, so use at your own risk. This was designed around the Hatchbox spools I had which are a 200mm OD x 68mm wide with a 55mm ID. This should work with most other spools, but worst case the spool holder is easy to make a little more adjustable. Electrical: The back switch gets wired normally closed and the front is wired normally open and the to switches must be in parallel and NOT series. See diagram above to help. 2)Wire the switches together outside the mounting areas and not together in the back box. For strain relief tie a knot in one of the 2 wires going to each switch or use a very small viptie inside each switch pocket. See pictures above. 3)You can slide the front switch in through the back and then place it on the tray and slide both back into the front position. Firmware: You may have to do some digging on this as ever printer will be a little different. Also modding your firmware can cause problems, be aware you do this at your own risk. I am running a Tevo Tarantula with a few mods, so I won't be posting my firmware, but I am using a copy of jimbrown's easy firmware 2.x and I only had to modify 2 things. In the Configuration.h file search for "Filament_Runout_Sensor" and make sure it is defined. In the pins_RAMPS.h file search for "FIL_RUNOUT_PIN" and set the pin to 12 if it isn't already 12. Compile and upload. Board Connection: You may have to do some digging on this as ever printer will be a little different. Also connecting things to your board can cause problems, be aware you do this at your own risk. See picture of the board I'm running above. You need to connect to pins S and -. It does not matter which cable connects where. Tool List (Recommended): Reamers - https://www.amazon.com/gp/product/B07QFR4NR9/ref=ppx_yo_dt_b_search_asin_title?ie=UTF8&psc=1 Deburring tool - https://www.amazon.com/gp/product/B07CS39XCV/ref=ppx_yo_dt_b_search_asin_title?ie=UTF8&psc=1 Hardware Required: Qty:1 - SHCS M6x15mm Qty:1 - FHSCS M6x25mm Qty:1 - FHSCS M8x50mm Qty:5 - SHCS M3x5mm or 6mm (whatever is easier to get) Qty:1 - M6 Nylock Qty:1 - M8 Nylock Qty:1 - 10g counter weight (https://www.evogimbals.com/collections/counterweights/products/smartphone-gimbal-counterweights-extra-4-pack) Qty:2 - Switches (https://www.amazon.com/gp/product/B01HHPD22S/ref=ppx_yo_dt_b_search_asin_title?ie=UTF8&psc=1) Optional Hardware: Swivel Head Arm: Qty:1 - M3x14mm or 16mm Qty:1 - M3 Washer Screw Down Base: Qty:4 FHSCS M5x10mm Qty:4 FHSCS M5x (Aslong as you need to mount to your base, would say 10mm min) 20mm Extrusion: Qty:2 - SHCS M4x10mm Qty:2 - T-Nuts M4 Sorry if I missed anything, will trying to keep updating this if I did. Enjoy and happy printing. UPDATE 2020-04-29: The holes in the swivel arm for the connection to the swivel head were sized wrong and should now be on size. I replaced their STLs. UPDATE 2020-04-30: Changed the angle of the arm from 15 to 30 degs to help keep the weight over the switch, replaced the all the files for the pieces above the base. Should reduce and false positives from the filament getting yanked. Update 2020-05-02: Updated some pictures with new version that i am currently running. Added firmware updates. Made hammer area bigger on the filament arm so it doesn't get caught on the front switch when in a forward position. Added a base for wood screws. Add step file of blank base for screw down so people can make their on pattern on it. Removed work-in-progress Update 2020-08-17 Was still getting a few false positives on low spools, so changed the arm angle back another 10degs and redesigned the filament arm to work with the new angle. Print Settings Printer Brand: TEVO Printer: Tarantula Rafts: No Supports: No Resolution: 0.15 Infill: 30% Filament: Hatchbox PLA Notes: If you have trouble with bed adhesion, i would recommend adding brim. I was able to print all parts will little to no adhesion problems. I use a glass plate with hair spray. 195C Nozzle 70C Build Plate Category: 3D Printer Accessories
With this file you will be able to print Filament Sensor Spool Holder with your 3D printer. Click on the button and save the file on your computer to work, edit or customize your design. You can also find more 3D designs for printers on Filament Sensor Spool Holder.