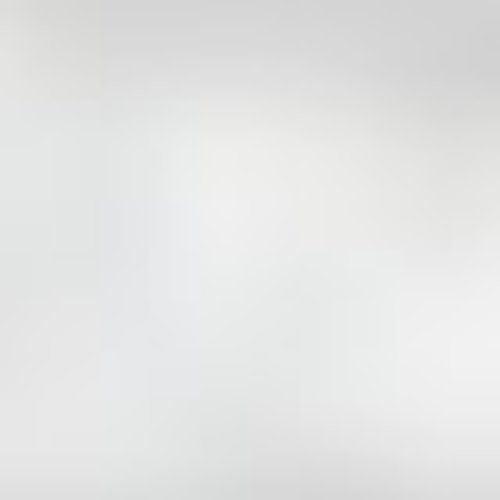
Extrusion Width Testing of 3D Printed Specimens
pinshape
I'd love to share a little experiment I conducted, hoping to tap into the collective wisdom of this community to gain deeper insights into my findings. To that end, I conducted mechanical tests on 3D printed specimens with diverse extrusion widths in order to determine the impact it had on the strength of the printed components. The results were carefully normalized to account for the inherent advantage of heavier parts and ensure a fair comparison among all tested specimens. By dividing the ultimate strength measurements by the mass of each part, I effectively neutralized any disparities and enabled a clear visual representation of the data. This led me to create the featured graph that showcases my findings. Initially, I anticipated a more predictable pattern in the results, but instead, I observed a much more complex relationship between extrusion width and printed part strength. Based on this unexpected outcome, I've come to suspect that the Slic3r program's extrusion width function is far more intricate than I initially assumed. Given these findings, my recommendation for now is to stick with the default extrusion setting in order to maximize part strength. To delve deeper into the specifics of my testing procedure and results, please refer to the attached PDF file. I'd be thrilled to hear about your personal experiences with varying extrusion widths! Have you encountered any notable differences or surprises during your own experiments?
With this file you will be able to print Extrusion Width Testing of 3D Printed Specimens with your 3D printer. Click on the button and save the file on your computer to work, edit or customize your design. You can also find more 3D designs for printers on Extrusion Width Testing of 3D Printed Specimens.