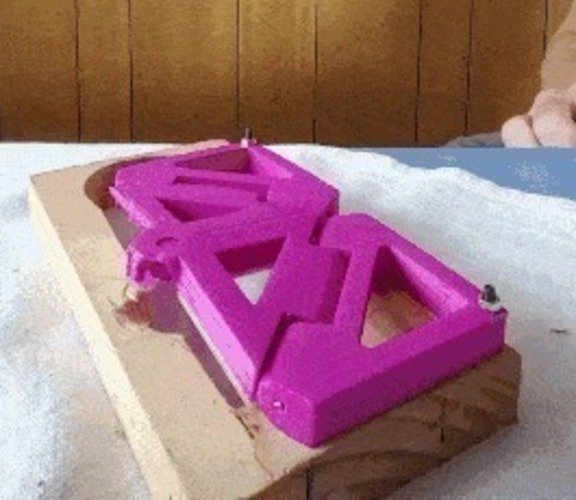
Evolution Door
pinshape
I implemented the "Evolution Door," a design inspired by Klemens Torggler's "flip panel door." Initially, I encountered this concept as an animated GIF labeled "folding gate." The idea fascinated me, and I sought to understand how it worked, leading me to create my own 3D printable version. Further research revealed that the original design was created by Austrian kinetic artist Klemens Torggler, which can be found at http://www.dezeen.com/2014/02/11/door-reinvented-with-folding-mechanism-by-klemens-torggler/. My design is available on https://cad.onshape.com/documents/56aa9d70e4b05aaf9b8ae389/w/179c3d1482a1f59f6f3a3ffa or by searching "Evolution Door" in the Public documents section of OnShape.com. A video demonstrating the mechanism is accessible at https://www.dropbox.com/s/55ulfiac9z6l4uy/20160130_133552.mp4?dl=0. The following print settings were used: Printer Brand: Printrbot, Printer Model: Simple Black, Rafts: No, Supports: No, Resolution: 0.2mm, Infill: 15% is fine. It's essential to note that in Slic3r, the "Only infill where needed" box should not be checked, as this can result in weak parts. Increasing the number of perimeters and top and bottom shells will strengthen the print. Two files are included for printing: a combined "Ball Joint" file and separate "ball" and "socket" files. If you choose to print the "Ball Joint," you won't need the individual components. However, if you decide to print them separately, you'll need to assemble them. If your print is somewhat sloppy, it shouldn't be an issue. Alternatively, pause the "socket" print when nearly complete and insert the ball before finishing. You'll require two copies of the "Triangle1" parts, which can be printed simultaneously even on a 100x100 printer. After printing, if you've used PLA and find that the socket is too loose and the ball falls out, try pouring boiling water onto the socket to bend it into place. This method may also help assemble the parts if they're printed separately. You'll need to drill through the holes, with 3mm outer corner holes in the Triangle1 pieces and 2mm hinge axle holes. The design is intended for use with 1.75mm filament as the axles but can be replaced with wire or any other material of suitable diameter. A door frame is necessary for mounting the Evolution Door, requiring two 3mm holes, 132mm apart, and a couple of M3 bolts as hinges. My primary design objective was to keep the outside of the door as flat as possible. This approach allowed me to conceal the mechanism (making it more magical) and create a more traditional door-like appearance. However, I later decided to include cut-outs in the panels to save filament. The biggest challenge for me was creating the ball joint as a print-in-place mechanism. My printer's growing looseness and lack of precision led to either parts being fused together or weak components breaking easily. In this design, the gap between parts is 1.75mm, but users with well-behaved printers can reduce this for a better product. Each side measures 66mm in length to fit on my 100x100mm printer. For those who want to scale it up, they'll need to refer back to the original source design. Scaling uniformly in all three dimensions is essential to maintain the round shape of the ball and socket. To ease printing, I kept the parts the same thickness as the ball diameter (12mm). Thinner components would be preferable but result in a smaller ball size, making it harder to print and weakening the axle connecting the ball to its triangle.
With this file you will be able to print Evolution Door with your 3D printer. Click on the button and save the file on your computer to work, edit or customize your design. You can also find more 3D designs for printers on Evolution Door.